二氧化碳液化裝置與碳捕集研究
眾所周知,溫室效應是大氣保溫效應的俗稱。溫室效應是由於大量的燃燒煤炭、石油、天然氣放出來的二氧化碳(CO2)進入大氣造成的,CO2具有吸熱和隔熱的功能。
有資料顯示,全球大氣CO2濃度已從工業革命前的280ppm升高到370ppm,且仍然以0.5%每年的速度遞增。預計到2050年前後,將達到450—550ppm之間。
溫室氣體不僅僅只有CO2一種,還有其他的氣體包括:氟氯烴、甲烷、低空臭氧、水蒸氣和氮氧化物氣體。
碳捕集是世界各國政府和研究機構都在加大力度研究減少CO2排放的問題焦點之一, 各大石油公司都將目標集中在 EOR(提高採收率技術)上,既減少了CO2對環境的影響, 又提高了油氣的採收率,在世界能源日益缺乏的今天,這一技術具有重要的應用前景。
為了達到注入CO2提高採收率的品質要求,提高液化、儲存和運輸效率,通常需要將CO2進行地面處理,將CO2從天然氣或廢氣中分離(或捕獲)出來,然後再進行二氧化碳液化 (或壓縮)和儲存,最後將CO2運輸到現場後注入到地層,這是處理CO2的方式之一。其分離方式有變壓吸附、膜分離及低溫液化法。
當前低溫法液化CO2一般有三種:即氮氣循環膨脹機製冷液化法,液氨蒸發法和氟里昂蒸發法液化CO2。
在工業生產領域,CO2提純液化設備可利用製造水泥、化肥、乙二醇、發電、釀酒、制氫等裝置所排出的CO2廢氣,生產出純度最高可達99.99%的食品級CO2,變廢為寶。能廣泛應用於飲料、焊接、滅火、大棚栽培、油田、糧食貯存等行業。可達到工藝簡單、投資低、能耗低、成本低、產量高的目標。
1
食品級CO2要求
「
求:
國際質量標準食品級CO2生產工藝通常,為了運輸和使用方便,生產中一般都把CO2製成液體或固體產品,從理論上講,只要CO2達到臨界溫度31.06℃以下,在特定壓力下即可液化。
生產中CO2的分壓直接決定了CO2液化的難易程度。由於原料氣來源的不同,其CO2的純度不同,CO2原料氣中含有的烴、醇、醛、苯、各種形態硫等多種對人體有毒有害雜質也不同,因此採用的生產工藝也會有很大不同。
(1) 石灰窯氣、鍋爐煙道氣等低CO2濃度原料氣
石灰窯氣、 這類CO2原料氣的主要特點是CO2濃度低,一般在 30%左右,有機雜質少。由於濃度低,要想在淺低溫下液化,如-12℃液化,則要求CO2必須具有約2.5Mpa(絕壓),那麼,液化時的總壓至少應>8.3Mpa。要求的設備壓力等級高、氣耗高、動力消耗大。由於操作壓力高,雜質分壓也高,會大量溶解在液體CO2中,產品純度低。
一般採用原料氣預處理提濃的辦法將原料氣CO2濃度提高到98%(濃度越高越有利於高品質CO2的生產),原料氣預處理提濃的方法主要為溶液吸收法和變壓吸附法。
溶液吸收法所得的CO2純度高,由於採用的溶液大都為有機物質,所得的原料CO2中會增加含有對人體有毒有害雜質。
變壓吸附法預處理提濃雖然不增加對人體有毒有害雜質,但受其工藝影響,所得的原料CO2純度較低,且不穩定。
目前我國針對石灰窯氣、鍋爐煙道氣等低CO2濃度原料氣的預提濃方法一般採用溶液吸收法。
(2) 合成氨廠變壓吸附脫碳排放的CO2原料氣
此類原料氣CO2濃度一般在 80~90%,主要是合成氨廠變壓吸附脫碳氣,其最大的特點是原料中烴、苯等對人體有毒有害的雜質都嚴重超標,一般都超出指標幾百甚至幾千倍。
特別是原料的變化,對原料CO2中的烴、苯等對人體有毒有害的雜質的影響很大,此類雜質通過一般物理吸附法難以穩定和確保合格。唯有採用燃燒法才可徹底去除,並不受原料變化影響。
此外,由於合成氨廠變壓吸附脫碳氣中含有大量的氫和一氧化碳,如不進行預處理,直接進入脫烴凈化塔時,不但浪費大量的氫和一氧化碳等合成氨生產原料,同時需要大量氧氣,對沒有空分裝置的企業,將很難實施。
外購氧氣,費用大,操作複雜。
如採用加空氣的方式補氧又將因空氣加入量太大降低原料氣純度,造成各種消耗急劇上升而不經濟。
我們根據此類原料氣主要雜質成份沸點比CO2低的特點,採用預提純工藝將其與CO2分離並回收,提高進脫烴凈化裝置的CO2純度。由於此時的CO2純度高達 99%以上,且可燃雜質很低,脫烴催化劑的使用空速可以大幅度提高,脫烴凈化塔及催化劑投資大幅降低。
(3) 高濃度CO2原料氣
此類原料氣的純度一般都在98%以上,雜質少,特別是可燃性的氫、一氧化碳雜質少,在脫烴凈化補氧時,可以採取加空氣的形式補氧,少量的空氣對各類消耗影響小,流程相對簡單,投資省,有尿素生產的企業特別適合生產生產國際標準食品級CO2。
(4) 酒精廠發酵氣
一般來說,以澱粉質為原料的酒精發酵氣中CO2的濃度可達99%以上,純度較高,同時含有少量的其它雜質,含量分別為:醇類0.3%(V)醛類0.05%(V)、有機酸類0.03~0.04%(V)、酯類0.01%(V)及微量烴類和氧氣,這些雜質均比新國家食品CO2和國際飲料技術協會標準高出幾百甚至上千倍。
雖然這些雜質有一定的水溶性,但要靠洗滌和洗附達到ppm 級、難度大,不易穩定,新國家食品CO2和國際飲料技術協會標準中要求醇類<10×10-6(V)、醛類<0.2×10-6、其它含氧有機物<1.0×10-6(有機酸類、酯類、酮、醚等)。
(5)CO2氣田氣
CO2氣田原料氣純度相對較高,雜質種類,特別是對人體有毒有害的雜質含量高。除甲烷、氫、氮等組分的沸點低於CO2外,還含有乙烷、硫化氫,是沸點與CO2的沸點接近的雜質,也有沸點高於CO2的油水等其他組分。
當前國際上食品級CO2生產工藝較先進的採用催化氧化脫烴凈化與精餾組合工藝,工藝成熟,技術可靠。採用該技術建成投產的數十套食品CO2生產裝置均成功運行,產品經化學工業氣體質量監督檢驗中心和國家標準物質研究中心以及美國大西洋實驗室(ALL)檢測,質量均能達國際飲料學會(ISBT)標準和國標 GB10621-2006,是可口可樂公司首選的CO2生產工藝。
該工藝採用JTL-I先進工藝進行精脫硫採用目前先進的JTL-1精脫硫工藝,採用專用脫硫劑和水解劑,使有機硫等難脫除的各種硫化物也得以徹底脫除,確保了產品總硫含量小於0.1ppm。
採用催化氧化專利技術凈化有機雜質採用該項發明專利技術,通過催化氧化的方法,可以將對人體有毒有害的烴、苯、及醛、醇等雜質進行有效的脫除。
實踐證明,催化氧化反應與其它方法相比,脫除上述雜質是最為徹底的,完全能使產品達到國際飲料協會標準和我國新的國家標準。
2
氟里昂蒸發法液化CO2工藝過程簡述
「
述:
2.1工藝簡述
工藝機理:原料氣中醇等可以溶於水,可用水吸收除去,用活性炭脫除氣味和部分雜質,分子篩進行乾燥,精餾除去一些輕組分及不凝氣,壓縮冷卻冷凝使CO2液化。
工藝過程如下:
(1)壓縮與冷卻過程:來自用戶的CO2氣體,進入壓縮機(帶有中間冷卻及末級冷卻),CO2經三段壓縮冷卻後,在壓力3.0MPa,常溫狀態下去下游繼續加工處理。
(2)分離與除雜質:自壓縮機來的CO2經冷卻、再次分離遊離水,CO2去凈化床,其中可吸附的雜質被除去,CO2從床層上部排出去乾燥器。
(3)乾燥與過濾:經凈化後的CO2進乾燥器,CO2從上部進入分子篩床,CO2經分子篩床層吸附脫除其中的水分之後在粉塵過濾器中除去粉塵及其他機械雜質;乾燥器為切換操作,即當一台處於8小時的吸附狀態時,另一台則處於再生冷吹狀態,再生氣為低壓殘氣,來自後續工段的低壓常溫殘氣經電加熱器加熱後,從再生床的下部通過分子篩床層,加熱脫除分子篩中被吸附的水分雜質,經再生,以備再次轉入到吸附狀態。
(4)冷卻與精餾過程:經前述凈化處理的原料氣進冷卻器的管內,在此原料氣被管外來自殘氣總管的低壓殘氣冷卻之後在液化器中被管外蒸發的R717繼續冷卻冷凝,進CO2精餾塔,在塔內利用精餾的方法脫除原料氣流中的不凝氣體等雜質,在再沸器得到液體CO2產品,產品再經節流至1.7MPa,溫度約-25℃去原裝置產品貯罐,塔釜的熱源為來自冷凍系統冷凝器上部抽取的氣體,為塔頂迴流冷凝器提供冷源的是節流後的液體氨,控制塔底CO2含量≥99.9%為前提,未被冷凝的,含不凝氣雜質的氣體則從冷凝器頂排出,並經壓力調節閥節流為低溫殘氣去冷卻器回收冷量。
(5)產品貯存:來自再沸器塔釜的液體CO2經液位調節閥減壓至壓力1.7MPa,溫度約-25℃後去CO2貯罐,由於來自再沸器的液體經節流後必然產生少量氣體,這部分氣體連同在貯存過程產生的蒸發汽體一併從罐頂上部的出口管排出,並經壓力調節閥減壓成低溫殘氣去殘氣總管,在冷卻器中回收冷量。
2.2系統組成及配置(以900m3/h為例)
(1)CO2壓縮機
型號:ZW-15/30,氣量:15m3/min,出口壓力:3.0MPa,出口溫度:
(2)冷凍機組,型號:JJZLG16
供貨範圍:壓縮機,形式:半開放式噴油螺桿,型號:JJZLG16,製冷工質:R717;能量調節方式:無級調節;能量調節範圍:10-100%;電機功率:100KW。
冷凝器,貯液器,集油器,空氣分離器,氣液分離器。
(3)主要設備(CO2提純液化部分)
換熱器,1台;水分離器,1台;CO2凈化床,1套;CO2乾燥器,1套;預冷器,1台;CO2液化器,1台;CO2再沸器,1台;CO2精餾塔,1台。
(4)主要設備(CO2儲存部分)
CO2儲罐(卧式雙層),1台,主要技術參數指標:型號:CDW-100/22;有效容積:100m3;最高工作壓力:2.16Mpa;絕熱方式:聚氨脂發泡;使用介質:液體CO2。
3
液氨蒸發法液化CO2流程
「
程:
3.1工藝簡述
流程簡述:凈化原料氣進入預冷器(E1),用液氨蒸發進行冷卻自5∽10℃,預冷後的凈化原料氣進入蒸發器(K1)進一步冷卻,冷卻後的凈化氣經過節流精餾塔,此時凈化原料氣有少量液化。
同時由精餾塔底部來的液體在蒸發器中蒸發,蒸發的蒸汽進入精餾塔,作為上升蒸汽。在精餾塔中精餾後,精餾塔頂部氣體進入塔頂冷凝器進行冷凝,冷凝由液氨蒸發提供,冷凝後液體返回精餾塔作為迴流液,廢氣放空,在精餾塔底部得到液體產品,液體產品在過冷器(E2)過冷後進入液體貯槽,冷源由液氨蒸發提供。
(1)工作原理:
CO2液化設備的工作原理:凈化原料氣中含有CO2、H2,O2,N2,CO,CH4等組分。依據各組分沸點的不同,經過加壓、預冷,並利用由氨冷機組提供使之液化再進行精餾從而獲得高純度的CO2產品。
(2)設計工藝條件
加工氣量:1000m3/h,氣體壓力:2.0∽2.5Mpa,溫度;常溫;原料氣體主要成分:CO2≥98.5%,N2≥0.4%,H2≤0.3%,O2≤0.3%,CO≤0.3%,CH4≤0.3%。
產品技術參數:CO2≥99.99%,CO≤10PPM,O2≤30PPM;輸出壓力:1.9MPa(A)進貯槽。
(3)成套系統
氨冷機組,原料氣凈化系統,精餾系統,液體貯存系統。
3.2運行操作
啟動操作:吹掃的目的是為了消除系統中任何雜質和使分餾塔中所有設備、閥門、管道充分乾燥,要求每個吹除閥門必須吹掃至不得再出現灰塵和遊離水為止。吹出氣體露點在-30℃以下。
緩慢打開V1,閥,V3閥導氣要慢。按照工藝流程打開吹除閥V2、V4,在吹除達到要求後關閉,在吹除時閥門不得開啟過猛。
系統的冷卻:此階段的操作要求是:必須保證凈化原料氣壓力的穩定和氨冷機組的穩定運行,當K1冷端溫度接近液化溫度約259K時,此階段便告結束。
操作準備:原料氣凈化系統運行正常。按照氨冷機組使用說明書,啟動氨冷機組的穩定運行正常。打開冷凝器(K2)氨通道閥門,使K2處於工作狀態。微開V2,微開V4待結霜後關閉,打開V5冷卻E2及貯槽,待冷卻好後,關V5。當TI-3達到259K時,即開始有液體出現時,本階段告結束。
液體積累及生產工況調整:調整液氨蒸發壓力,使蒸發溫度在246K左右,稍開V4,檢查是否有液體出現,當有液體時應排放,並查看是否乾淨,如不幹凈,應反覆排放多次,直到乾淨為止。微開E2液氨管路閥門,使E2處於工作狀態,稍開V5。當精餾塔有阻力出現時,對精餾塔進行純度調整,調整V3及液氨管路閥門,使得純度逐漸達到要求。
當精餾塔液面逐漸增高,漸開V5,使精餾塔液位穩定在1000mm。同時通過控制E2的工作負荷,保證輸出液態CO2的過冷度。隨著氣體的大量液化,進入精餾系統的氣量越來越多,因此根據工況變化應注意原料氣凈化系統的保壓。
設備正常運行後,要求調整各參數如下:TI-1預冷器後溫度指示:5∽10℃;TI-2過冷器後溫度指示:243K;TI-3精餾塔頂部溫度指示:250K;LI-1精餾塔液面指示:1000mm;PI-1精餾塔下部壓力指示:22.1bar;PI-2精餾塔頂部壓力指示:22bar;A-1:CO2≥99.99%,O2≤30ppm;CO≤10ppm。
4
煙氣中的CO2液化方案
「
述:
富氧燃燒技術又稱空氣分離/煙氣再循環燃燒技術或O2/CO2燃燒技術,該技術採用空氣分離製取得到的較高純度的氧氣(一般為95%)與再循環煙氣及攜帶的煤粉一起送入燃燒室燃燒,富氧燃燒方式可以使煙氣中的CO2濃度高達90%以上,其餘為殘餘N2、O2及硫氧化物(SO2+COS+O2S+O3S)、氮氧化物NOx、CO、煙塵等雜質。
儘管在富氧燃燒環境下,燃燒產生的硫氧化物、氮氧化物NOx大大減少,但煙氣中的質量濃度均在1000mg/m3以上,如果排放到大氣,會對大氣環境造成巨大的危害。
因此,對富氧燃燒產生的CO2進行捕集,脫除CO2氣體中的SO2、NOx等酸性氣體以及N2、O2等惰性氣體,獲得高純度液體CO2,形成食品級、工業原料氣以及埋存CO2,既能減排CO2又能進行資源回收,具有重要的意義。
CO2的純化主要有鉛室法、塔式法和接觸法,有漸被取代的趨勢。
傳統脫硫脫硝技術採用濕法煙氣脫硫和NH3選擇性催化還原技術脫硝的組合,其工藝工程龐大,初投資和運行費用高,易形成二次污染。
本文以加壓鉛室化學工藝為基礎,探索新型的脫硫脫硝技術:富氧燃燒煙氣中同時含有H2O、O2、SO2和NOx,在一定的壓力和溫度條件下,SO2和NOx能通過化學反應轉化成H2SO4和HNO3從而被脫除,該化學反應已經被證明是可行,反應壓力正好可以利用液化CO2的壓縮功。
(1)CO2壓縮純化技術
壓縮純化技術以加壓鉛室化學工藝為基礎,在一定的壓力和溫度條件下,富氧燃燒煙氣中的SO2和NOx能通過化學反應轉化成H2SO4和HNO3從而被脫除,如下圖所示,該化學反應已經被證明是可行。
壓縮純化反應裝置包括:壓縮機、接觸塔、低溫分離裝置等關鍵設備及其他必要設備。
反應基本原理:2NO+O2 2NO2
(1)NO+NO2 N2O3
(2)SO2+N2O3+H2O H2SO4+2NO
(3)在鉛室中,用氮的氧化物作遞氧劑,把二氧化硫充分氧化而成硫酸,同時,還進行以下反應把氮氧化物轉化成硝酸2NO2+H2OHNO2+HNO3
(4)2HNO2HNO3+2NO+H2O
(5)根據化學反應動力學機理,可以從反應物的濃度、反應壓力、反應溫度等方面研究化學反應速率及反應過程,從而得到CO2氣體中SO2、NOx等酸性氣體轉化析出特性。
(2)富氧燃燒煙氣中的N2、O2等惰性氣體的脫除方法
理論上有:低溫分離,變壓吸附脫除。
吸附法是利用固態吸附劑選擇性吸附的特性,吸附煙氣中的N2、O2等惰性氣體和水分等雜質,從而得到純度較高的CO2氣體,而要得到液態CO2,還需要進一步壓縮冷卻變成CO2液體。
吸附法工藝、設備、操作簡單,但要定期更換吸附劑,解析加熱再生需要消耗大量熱量,最重要的是吸附法目前處理量小、成本偏高,不適用於大規模的工程應用。
低溫分離技術是氣體分離中一種重要的方法,低溫分離法(又稱深冷分離法)是通過低溫冷凝分離CO2的一種物理過程。一般是將混合氣壓縮和冷卻,以引起CO2的相變,利用低溫下CO2與N2、O2等雜質沸點不同的特點,通過精餾完成N2、O2與CO2分離,從而得到高純度、食品級的CO2產品。
低溫分離可實現大規模操作,運行過程不需要化學試劑,運行費用較低且對環境無二次污染。
低溫分離技術大規模用於CO2回收的關鍵在於能夠以低能耗獲得低溫冷源、使CO2分離能耗降到可以接受的程度,同時應盡量避免CO2的凍結。
低溫分離不僅能生產高純度的達到國家食品級標準的CO2產品,同時能直接得到液態CO2。
(3)CO2壓縮純化及液化、精餾流程簡述
裝置包括前述的原料氣煙氣壓縮系統、SO2、NOx脫除系統(鉛室),以及氣體乾燥系統、CO2液化及精餾系統、液體貯存系統等。
由於壓縮純化中原料氣壓力已經得到了提高,液化CO2的正好可以直接利用,使CO2的液化更容易進行。
乾燥系統:經前述壓縮、凈化處理後的富氧燃燒煙氣,先經分離器除去遊離水,然後進入吸附式乾燥器進行微量水脫除,確保乾燥後的CO2原料氣水分≤20ppm,以保證CO2在液化、提純過程中,不因水分在低溫下結冰堵塞管道及設備。
液化與精餾系統:乾燥後的CO2原料氣先在預冷器中與提純塔放空氣換熱後,進入冷凝器中用液氨在-25—-30℃下蒸髮帶走熱量使CO2原料氣冷凝成液體。
液化後的CO2進入精餾塔,根據CO2與雜質組分的沸點不同,利用精餾原理將雜質加以分離,在塔釜得到合格的液體CO2產品;精餾塔頂部冷凝器用液氨作為冷源,液氨蒸發吸熱使CO2冷凝產生迴流。
未被冷凝的,含不凝氣雜質的氣體則從冷凝器頂排出,經冷卻器回收冷量。流程如下圖所示。
CO2液化精餾部分主要設備:(1)分離器(2)乾燥吸附器(3)換熱器(4)液化器(5)精餾塔(含再沸器、塔頂冷凝器)6)氨壓機(可用液氨代替)。
CO2的捕集
CO2捕捉和封存很可能成為未來溫室氣體立法的一個關鍵要素。
現在設計中的完整氣化聯合循環工廠有規定,在升高壓力下分離CO2。
燃煤工廠面臨非常困難且成本昂貴的任務——只在高於大氣條件下分離和壓縮CO2。
對於典型粉煤發電廠而言,任何CO2捕捉和封存系統必須在將CO2穩定並封存於地下之前,需對從廢氣中捕捉的一種相對純的CO2施加壓力,使之達到超臨界液體狀態。
這種按比例實施CO2捕捉和封存有可能在將來成為一種需求,以便用於減少安裝成本,並使這種工藝固有的營運成本減到最小。
今天的CO2捕捉被典型優化為化學過程,通常與發電廠必須的CO2壓縮機分離。
這意味著CO2壓縮機技術被不正確地看作一個既成事實,而不是值得更多研究和開發的一個技術機會。
CO2捕捉系統與發電廠規模和類型不同。現有絕大多數發電廠和很多今後新建的電廠是粉煤電廠。典型情況下粉煤電廠採用胺或者氨基CO2捕捉和封存工藝設計。
這種胺工藝生成一種相對純的CO2氣流,在15.0-21.9 lb/in2的壓力下,在70-100F入口溫度範圍之內浸透水。
氨基捕捉工藝也可以生成一種相對純的CO2蒸汽,但是在30-300 lb/in2之間的升高壓力下;入口溫度是標稱100F。
胺和氨基CO2捕捉和封存系統必須把CO2壓縮到一種超臨界狀態,用於運輸和儲存。發電廠當地的儲存壓力需要一個標稱1600 lb/in2,而當前的管道規範是2215 lb/in2。
使任何一項CO2捕捉和封存系統的可變運行與維護(O&M)成本減到最小的關鍵,是把最有效和可靠的壓縮技術與捕捉工藝結合起來。
上圖比較替代方案這個流程圖說明了典型的壓縮過程(A到B)和典型的液化過程(A到C)作為CO2捕捉系統的設計方案。兩種過程從低壓壓縮機和熱回收中間冷卻器(1到A)開始。
Ramgen電力系統採用與超音速飛機進氣道系統相同的衝擊壓縮技術,來開發一種高效氣體壓縮機。
衝擊壓縮技術是目前唯一適合壓縮大容量CO2的技術,由美國能源部國家能源技術實驗室進行技術投資,與Dresser-Rand合資,承諾可以明顯地減少在CO2捕捉和封存系統中的氣體壓縮輔助負載。
碳捕集與封存方式
CCS(碳捕集與封存)技術可以分為:捕集、運輸以及封存三個步驟,商業化的CO2捕集已運營了一段時間,技術已發展較為成熟,而CO2封存技術各國還在進行大規模的實驗。
CO2的捕集方式主要有三種:燃燒前捕集(Pre-combustion)、富氧燃燒(Oxy-fuel combustion)和燃燒後捕集(Post-combustion)。
(1)碳捕集與封存燃燒前捕集
燃燒前捕集主要運用於IGCC(整體煤氣化聯合循環)系統中,將煤高壓富氧氣化變成煤氣,再經過水煤氣變換後將產生CO2和氫氣(H2),氣體壓力和CO2濃度都很高,將很容易對CO2進行捕集。剩下的H2可以被當作燃料使用。
該技術的捕集系統小,能耗低,在效率以及對污染物的控制方面有很大的潛力,因此受到廣泛關注。然而,IGCC發電技術仍面臨著投資成本太高,可靠性還有待提高等問題。
(2)碳捕集與封存富氧燃燒
富氧燃燒採用傳統燃煤電站的技術流程,但通過制氧技術,將空氣中大比例的氮氣(N2)脫除,直接採用高濃度的氧氣(O2)與抽回的部分煙氣(煙道氣)的混合氣體來替代空氣,這樣得到的煙氣中有高濃度的CO2氣體,可以直接進行處理和封存。
歐洲已有在小型電廠進行改造的富氧燃燒項目。該技術路線面臨的最大難題是制氧技術的投資和能耗太高,還沒找到一種廉價低耗的能動技術。
(3)碳捕集與封存燃燒後捕集
燃燒後捕集即在燃燒排放的煙氣中捕集CO2,如今常用的CO2分離技術主要有化學吸收法(利用酸鹼性吸收)和物理吸收法(變溫或變壓吸附),此外還有膜分離法技術,正處於發展階段,但卻是公認的在能耗和設備緊湊性方面具有非常大潛力的技術。
從理論上說,燃燒後捕集技術適用於任何一種火力發電廠。然而,普通煙氣的壓力小體積大,CO2濃度低,而且含有大量的N2,因此捕集系統龐大,耗費大量的能源。
高純氮雙塔雙冷凝內壓流程、高純氮單塔內壓流程、氣相壓縮低溫壓縮機流程、無外耗電全液體LNG冷能空分流程、LNG冷能空分液空連續補冷流程、方形水冷卻塔、先進的峰谷電利用空分流程、一鍵啟動無人值守控制系統、空分遠程操作與監控系統、液氮補冷雙塔制氮流程等十大技術的成功研發(雙塔返流制氮、三塔低純氧自增壓帶精餾塔流程為第八代空分技術),表明我國空分科學家的研究處於世界空分技術的最前沿水平,在世界上佔據領先地位。
同第八代空分技術相比,上述十大空分技術節能較大,標誌著第九代空分技術在我國已經研發成功,開始大面積推廣應用。
CO2的存在相當廣泛,主要有自然存在於CO2氣田、石油溶解氣、天然氣等和工業生產廢氣。
在工業廢氣中,主要有煙道氣、化工廠尾氣、生物發酵氣。隨著人類社會生產力的高速發展,不斷地消耗掉大量的天然含碳資源,同時使大氣中CO2迅速增加,全球每年排放的CO2量高達200多億噸。
大量的CO2排放,不僅對人類生存環境帶來惡劣影響,不斷加劇「溫室效應」;也造成了CO2這一寶貴資源的嚴重浪費。CO2用途非常廣,可廣泛用於食品加工、機械製造、化工原料、精細化工、沙漠大棚種植等行業,要將CO2變廢為寶,造福人類,關鍵在於CO2的回收利用技術。
我國的CO2排放量約佔全球總排放量的10%,為全球CO2第二大排放大國,如何回收利用好CO2顯得意義尤為重大,也是貫徹我國實施科學發展觀、能源再生利用、保護環境、構築和諧社會的一項重要工作。
我國的CO2作為一個新生產業近幾年也因此得到了突飛猛進的發展,但各廠因原料來源不同和採用的工藝技術不同,產品質量和效益差別甚大。
所以發展先進的技術並帶動CO2相關產業的發展對未來及我國氣體分離行業而言意義重大。

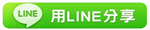
※地球上還有大型的未知物種嗎?
※保鮮膜的不正確用途
※權游里的全場最佳:提利爾家的老奶奶
※BBC記者愚弄滙豐銀行語音識別系統
※我們應該如何看待「地平說」的支持者
TAG:煎蛋 |
※油菜聯合收穫機脫粒裝置優化
※凈化器環境測試艙的污染源發生裝置詳解
※粉色的金屬裝置柔化混凝土的灰色質地,墨爾本公寓
※「變廢為寶」的裝置藝術
※第三代核能關鍵技術——燃料轉運裝置
※科學家研究出專吸海里塑料垃圾的巨型裝置,將改善海洋生態
※延安能化聚丙烯裝置打通全流程出合格產品
※綠色環保、便宜高效的光化學凈水裝置
※三款產品,重新定義空氣凈化裝置
※石化緣推薦:煉油化工裝置常用的壓縮機分類及特點!
※零售與裝置藝術結合
※心血管植入式電子裝置的圍手術期管理
※RTO助力綠色金屬印塗——兼談金屬包裝業空氣凈化裝置的選型和評價標準
※新型輻射供冷末端裝置的開發與數值模擬研究
※植物博物館的互動裝置
※中國單套最大高效合成氣制乙二醇裝置成功投產
※美國研究人員為柔性機器人研製出可模仿生物肌肉運動的柔性自愈裝置
※石墨烯裝置讓物體紅外「隱形」
※俄測試厭氧動力裝置:採用獨家氫氣製取技術 潛艇可水下充電
※「蜂巢」裝置——義大利雕塑裝置景觀