鈑金柔性製造系統應用案例
王勇,技術總監,工程師,主要從事軍用機箱、機櫃、控制台等產品的銷售、設計開發等工作;組織完成了多項神舟飛船指控大廳控制台的總體設計及安裝工作,配合多家院所完成機櫃、控制台的設計工作。
作為一個現代化的鈑金企業,柔性製造技術是企業得以長久發展的必然趨勢。只有運用柔性製造技術,控制生產成本、縮短生產時間、提高生產效率,企業才能在競爭日益激烈的鈑金製造行業站穩腳跟,才能快速響應客戶、適應客戶和市場的需求,為企業、為員工在行業內贏得一席之地。
柔性製造系統簡稱FMS(Flexible Manufacture System),是一組數控機床和其他自動化的工藝設備,由計算機信息控制系統和物料自動儲運系統有機結合的整體。柔性製造系統由加工、物流、信息三個子系統組成,在加工自動化的基礎上實現物料和信息的自動化。
目前國際上知名的鈑金柔性生產線主要以歐美廠家為主,包括義大利薩瓦尼尼(SALVAGNINI)公司的S4+P4、義大利普瑞瑪(PRIMA)公司的PSBB和午夜快車、荷蘭威莫(WEMO)柔性線、法國迪美高(DIMECO)柔性線、芬蘭比瓦迪(PIVATIC)柔性線等。這些鈑金柔性生產線都有著共同的特點,就是生產效率高、產品質量優、工時費用低、產能穩定、應變能力強。
我司於2003年引進義大利薩瓦尼尼公司的MD+S4+P4全自動鈑金柔性生產線,是集合了衝壓、剪切和折彎等工藝,無需人工操作的全自動化系統。其快速送料系統可高效、及時完成大批量、小批量或是成套產品的生產。
MD——立體料庫
料庫採用前入式、吸盤自動後上料結構,分成九層放置不同規格、材質的板材(最大3噸/層),極大地節省了材料倉儲空間。料庫與S4對接,根據S4程序的材質和尺寸要求選用板材,同時對料庫中各層板料的規格、數量進行實時監控,可依據監控數據及時補充板料,確保了生產的連續性。MD系統作為鈑金柔性生產線的第一個環節,充分體現了柔性生產中的物料自動儲運要求。
圖1 MD立體料庫
圖2 倉儲數據
S4——柔性沖切複合系統
SALVAGNINI的S4系統具有複合沖頭庫和獨有的一體化直角剪,直角剪與其他數沖設備的模具沖切不同,而是用剪切方式進行加工,加工間隙根據材質、板厚自動調節,剪切無鐵屑,其最大剪切長度X向和Y向均達400mm,而普通的模具沖切刀為110mm(E工位),直角剪一次加工長度是模具切刀的3倍,而且直角剪還可雙向同步動作,有效地提高了沖切效率。
圖3 SALVAGNINI S4柔性沖切複合系統
在零件下料方式上單機數控沖床只能整板加工完畢後對零件進行分揀處理,而S4卻可以沖剪結合交替工作,每個零件一旦加工完畢即可被卸下,而其他零件繼續加工,這樣就為後續工序提供了加工零件,尤其為P4折彎提供了加工零件,實現了真正的柔性流水線作業模式,有效地減少了工序間等待時間。
P4——柔性多邊折彎中心
與傳統的邊定位折彎不同,P4折彎採用產品成形尺寸定位原則,從加工之初就確保了零件的外形尺寸,可有效消除因零件下料偏差而導致的折彎誤差。
P4折彎無需更換模具,而是採用一套萬能模具和多組分段輔助模具來進行折彎加工,做到了真正的「零」秒換模,柔性加工特點極為突出。
圖4 SALVAGNINI P4柔性多邊折彎中心
產品應用實例
下面以我司生產的兩種零件為例,來說明SALVAGNINI柔性生產線和AMADA單機設備在加工效率上的區別。
箱體零件
某箱體零件,為2.0mm覆鋁鋅板,零件展開尺寸:825mm×912mm,見圖5;其使用S4加工程序見圖6;使用EM 2510加工程序見圖7;使用兩種不同設備下料加工時間對比見圖8;使用P4折彎加工程序見圖9。
圖5 箱體零件圖
圖6 S4加工程序圖(3件排版)
圖7 AMADA EM2510加工程序圖(3件排版)
圖8 箱體零件下料加工時間對比(3件排版)
圖9 箱體零件P4折彎加工程序圖(1件)
框架零件
某框架零件:2.0mm覆鋁鋅板,零件展開尺寸:860mm×520mm,見圖10;其使用S4和EM 2510兩種不同設備下料加工時間對比見圖11;使用P4折彎加工程序見圖12。
圖10 框架零件圖
圖11 框架零件下料加工時間對比(4件排版)
圖12 框架零件P4折彎加工程序圖(1件)
從這兩種零件的加工數據(表1)可以看出,SALVAGNINI柔性生產線不管在生產人員數量、設備數量還是生產時間上均優於單機設備,整體上降低了產品的加工成本,為公司的競價銷售提供了有效的支持。
從這兩種零件的加工數據可以看出,在沖切下料時間上AMADA的EM2510數控沖床比SALVAGNINI的S4柔性加工系統要長,同時在作業人員上投入多出一倍,其主要原因在於設備的自動化、模具結構等多方面因素:
(1)設備的自動化。
SALVAGNINI的S4由MD系統通過機械手供料,板料在S4上由13個夾鉗裝卡、用直角剪修邊確保板料尺寸,這些動作全部只需1人操作、機床全自動完成。而單機設備只能通過多人或藉助輔助上料裝置進行板料供給,板料在沖床上的定位一般依靠人工作業確定,在工作效率上明顯低於S4。
(2)模具結構。
S4模具沖頭均由獨立的液壓系統控制,而傳統的轉塔沖床則為單點伺服或液壓系統控制沖頭,這樣就增加了模具的切換時間,再加上S4獨有的直角剪,S4的沖切效率絕對佔優。如上述箱體零件的S4沖切時間為192秒/件,AMADA的為227秒/件,S4較其短35秒/件,整板(3件/張)加工短105秒,具有較高的生產效率。
(3)下料碼垛。
鈑金件與結構件在零件加工上最大的不同就在數量上,鈑金材料沖切工序為一次加工多個零件,而結構件只有一個零件,這就對鈑金沖切下料的效率提出了要求。S4的每個零件一旦加工完畢即可被卸下,如與P4聯動可直接進行折彎加工,無工序間等待時間。表1中的箱體和框架零件,在S4下料後通過傳送帶直接轉至P4進行折彎,做到了真正的「零」工序轉運。
表1 箱體零件和框架零件加工數據對比表
這兩種零件從折彎難度上箱體零件較為複雜,但從P4系統的折彎時間來看,時間相差並不多,箱體為45秒、框架為36秒,其根本原因在於P4系統的自動化、柔性化。
(4)自動化。
P4作為全自動折彎系統,只需一人作業即可完成零件的折彎加工,其上料、折彎、下料均為自動裝置。而傳統折彎機則需多人作業完成折彎,在人力、設備上投入較高。
(5)柔性化。
P4的萬能模具及多組分段輔助模具在柔性加工中極具特點。箱體在P4上只需1人45秒加工完成,而在單機上由於零件的折彎特點,需要3台折彎機(2人/機)上配裝直劍刀(整刀)、彎刀(分段刀)完成,完成1件需125秒,加工時間長、佔用人員多。
SALVAGNINI鈑金柔性生產線以其高度自動化而見長,但也因自動化程度過高造成一些短板,如對板材的平面度要求較高、加工的板材厚度一般以3.0mm以下為主、不易加工過於細長的零件、反向折彎成形邊要求高、設備複雜維修成本高等。這就要求我們的工藝設計人員必須了解設備的加工特點及局限性,設計出更加符合設備生產的產品。對於鈑金製造商而言,不管是自主產品還是OEM產品,優化設計、優化工藝、適宜自主生產永遠是無止境的。
結束語
作為一個現代化的鈑金企業,柔性製造技術是企業得以長久發展的必然趨勢。只有運用柔性製造技術,控制生產成本、縮短生產時間、提高生產效率,企業才能在競爭日益激烈的鈑金製造行業站穩腳跟,才能快速響應客戶、適應客戶和市場的需求,為企業、為員工在行業內贏得一席之地。
——摘自《鈑金與製作》 2017年第4期P12-16頁

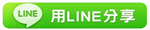
TAG:鈑金與製作 |