計算機「化」系統中的「計算機控制系統」的確認與驗證
你是在編程嗎?
你只是在編好的程序裡面進行功能組態與二次應用開發而已!
對製造商而言,是可配置系統
對終極用戶而言,是不可配置系統
計算機「化」系統驗證,本身就是設備和系統的確認與驗證,關鍵詞不是計算機控制系統,而是被計算機控制的「系統」
當然我們應該關注計算機控制系統的確認與驗證,甚至計算機軟體的驗證,但是,專業的事兒還是專業的人來做吧!
一、計算機化系統中的計算機控制系統的確認與驗證策略
1、對於嵌入式計算機和HMI+PLC控制系統(單機控制)
l作為設備、系統的一個操作部件或者一個組成部分,進行必要的評估、確認、操作、測試、校準、維護就可以了。
2、對於其它可配置非定製較複雜計算機控制系統
l可進行單獨的計算機系統的生命周期的確認與驗證。
l一般的DQ/IQ/OQ及功能性測試就可以了。
3、對於其它定製較複雜計算機控制系統
l可進行單獨的計算機控制系統的生命周期的確認與驗證。
l設計審核
l源代碼審核
二、法規生效前已投入使用的計算機化系統確認與驗證策略
已投入使用的計算機系統應該也經過了嚴格的測試、驗收、短時間或長期的生產運行,運行中發現的問題,也應該已經進行了維修、改進,影響關鍵工藝參數或者影響關鍵質量屬性的缺陷,應該按照偏差、變更流程進行糾偏和變更。
重新進行全流程的確認與驗證可能某些測試「無法重現、沒有必要」或者需要停工停產投入大量資源造成「浪費」,使「成本、收益、風險」嚴重不一致。
所以,可以基於風險原則採取如下措施:
1、對所有涉及計算機控制的設備、系統登記造冊、做好分類台賬,制定確認與驗證策略。
2、收集建設期及現有的計算機化系統的工程文件、技術資料、運維記錄、歷史數據、偏差、變更活動的記錄……進行回顧審核。
3、採用差距分析的方法對照計算機系統相關法規進行「法規符合性審核」,如果有缺陷項就納入整改。
4、對於生產工藝、產品質量、數據完整性方面的風險進行回顧審核或者風險再評估。
「回顧、審核、差距分析、自檢、風險再評估」活動中發現的「不符合項、缺陷項、不可接受的風險」進行處理(CAPA、偏差、變更),然後根據評估結果對必要的、相關的、部分項目或者部分變更項目進行「確認和驗證」。
基於生命周期的持續的回顧審核與評估!
三、計算機化系統生命周期的驗證(新系統)
1、驗證計劃(Validation Plan)
l可以納入公司或者項目的驗證主計劃中。
2、用戶需求說明(URS)
l需要計算機幫我們做什麼?(功能清單)
l每一個功能的控制方式,執行過程?(工藝流程圖)
l每一個功能的感測器輸入、執行信號輸出(輸入輸出方式)
l操作人員對人機介面的操作要求?(人機介面輸入輸出方式)
l系統的安全性要求?(許可權設置)
l安裝空間、位置、所處的環境?
l硬體、軟體的基本配置要求?
l測試、驗證、培訓、質量控制、變更控制、文件記錄要求
l預算、貨期、合約等商務要求
3、功能說明(Function Specification)
l系統供應商對企業URS的回復說明。
l硬體配置方框圖與功能說明。
l軟體流程方框圖與功能說明。
4、設計說明(Design Specification)
l供應商對自己系統的設計思路與計劃
l硬體整體框架與系統結構圖
l軟體整體框架、模塊化系統結構圖
lIO清單與詳細說明
5、系統工程設計
l用戶可以不參與
6、設計審核(Design Review)
l設計審核一般由用戶技術人員與QA完成,通過比較URS與FS、DS的一致性,檢查系統是否滿足需求,針對不能滿足的部分,需要和供應商進行協商,尤其是涉及到GMP要求的地方要更加註意。
7、風險評估(Risk Assessment)
l風險評估工作貫穿用戶需求到設計回顧。
l主要考慮系統功能、系統安全性對生產工藝、產品質量的影響。
8、系統工程製造和工程調試(用戶可以不參與)
9、出廠測試(FAT)
l供應商在系統出廠前進行相關測試,並記錄測試項目和結果,判斷是否符合標準(可以反覆測試)。
l模塊測試(白盒法)集成測試(黑盒法)
l功能測試
10、現場測試(SAT)
l安裝到企業時,也需要進行相關的測試,並記錄測試項目和結果以及是否符合標準,更多的是計算機完成的功能測試。
11、IQ階段
l確認硬體配置、軟體版本
l確認現場安裝環境、安裝條件、安裝結果
l確認供應商審計的文件報告
l確認系統開發的技術文件和報告(審核開發過程、而不是審核每一條程序、指令的正確性)、確認模擬模擬與調試階段的文件與報告(更多的是一種形式審核與確認)
l確認安裝後的各種測試、調試的文件、記錄和報告(更多的是一種形式審核與確認)。
l確認各種技術資料、編程軟體、應用軟體備份、密碼保存
l確認輸入輸出(I/O)清單、電路圖、接線圖……硬體和軟體手冊,包括安裝、操作、維修保養手冊。
12、OQ階段
l按照操作SOP進行各種操作、測試,包括系統的安全性、三級密碼、操作許可權、IO輸入輸出的測試、人機介面、錯誤輸入、報警、聯鎖、斷電恢復……
l確認每一個正常的工作步驟、每一個操作部件(包含硬體操作部件和模擬操作部件)、每一個輸入輸出之間的動作關係
l模擬運行的過程測試
l全自動運行的過程測試確認。
l正常環境下,模擬生產環境下的測試。
13、PQ階段
l確認系統運行過程的有效性和穩定性。
l測試項目依據對系統運行希望達到的整體效果而定,如對生產出的產品質量各項特性進行測試。
l測試應在正常生產環境下。
l相當於隨著正常生產的工藝驗證過程進行測試。
14、風險管理矩陣(Risk Management Matrix)
l從前期的風險評估,到貫穿於IQ,OQ,PQ的風險控制,最後需要對風險進行回顧,確認通過測試以及修改是否已經將風險降低到了可接受的水平。
15、最終驗證報告(Final ValidationReport)
l總結整個驗證過程,是否都正確完成,沒有未處理的偏差。正式批准系統投入運行。
16、周期性的系統檢查及風險回顧。
四、自動裝盒機生命周期的驗證案例(新系統)
1、用戶需求說明(URS)
l需要計算機幫我們做什麼?(產品裝盒)
l標籤打碼、貼標、說明書打碼、折說明書、塞說明書、自動開盒、自動裝盒、自動封盒、盒噴碼……
l無產品、無說明書、無標籤、說明書錯誤、標籤錯誤……報警剔廢
l無產品、無紙盒、無說明書、無標籤、開盒不到位、裝盒不到位……報警停機
l標籤、說明書、瓶、盒……自動計數
l自動生成批包裝記錄
l每一個功能的控制方式,執行過程?(工藝流程圖)
l每一個功能的感測器輸入、執行信號輸出
l操作人員對人機介面的操作要求?
l系統的安全性要求?(許可權設置)
l安裝空間、位置、所處的環境?
l硬體、軟體的基本配置要求?
l測試、驗證、培訓、偏差、變更控制、文件記錄要求
l預算、貨期、合約等商務要求
2、功能說明
l機械、電氣、硬體、軟體,供應商提供
3、設計說明
l機械、電氣、硬體、軟體,供應商提供
4、系統工程設計(供應商設計)
5、設計審核
l設備部分DQ,計算機定製系統DQ,用戶參與
6、風險評估
l基於裝盒機對工藝參數和產品質量的風險
7、系統工程製造和工程調試(供應商工作)
8、出廠測試FAT
l基於裝盒機本身的功能測試和測試條件下的計算機系統IQ測試,供應商與用戶合作
9、現場測試SAT
l基於裝盒機本身的功能測試和運行條件下的IQ測試,供應商與用戶合作
10、IQ階段
l確認各種技術資料、編程軟體、應用軟體備份、密碼保存,輸入輸出(I/O)清單、電氣原理圖、元器件布置圖、接線圖……硬體和軟體手冊,包括安裝、操作、維修保養手冊。
l確認供應商審計的文件報告、系統開發的技術文件和報告、模擬模擬與調試階段的文件與報告。
l確認硬體配置、軟體版本、軟體安裝位置,確認安裝後的各種測試、調試的文件、記錄和報告。
l確認安裝環境、安裝條件、各機械、電氣部件安裝結果。
l確認產品、紙盒、說明書、標籤的規格與設備的規格匹配。
l確認各種外接公用介質的質量條件
11、OQ階段
l簽名確認表、文件檢查
l在線儀錶的校準、測試儀錶的校準
l開機前的檢查與材料準備
l開機,三級密碼、操作許可權的確認
l按照操作SOP在觸摸屏上進行每一級別菜單的參數設置、手動操作、模擬測試
包括IO輸入輸出的測試、人機介面、列印輸出,錯誤輸入、報警、聯鎖、剔廢、斷電恢復、數據備份、數據轉移、數據刪改……
l確認每一個正常的工作步驟、每一個操作部件(包含硬體操作部件和模擬操作部件)、每一個輸入輸出之間的動作關係、模擬運行的過程測試、全自動運行的過程測試確認。
lPLC程序步驟的確認
l生產能力
l剔廢功能(人為的各種錯誤剔廢)
l安全聯鎖(人為的各種安全事件)
l成品合格率/紙盒/說明書/標籤上機合格率
l更換不同規格產品的測試
12、PQ階段
l確認系統運行過程的有效性和穩定性。
l測試項目依據對系統運行希望達到的整體效果而定如對生產出的產品質量各項特性進行測試。
l測試應在正常生產環境下。
l相當於隨著正常生產的工藝驗證過程進行測試。
(完)

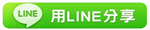
TAG:製藥GMP工作室 |