談工匠精神?小胖帶你看哈蘇是怎樣製造數碼相機的
要問關於哈蘇的關鍵詞,「貴」「高端」「信仰充值」等等形容詞一定是甚囂塵上,很多人還以為哈蘇跟徠卡蔡司一樣是德國品牌,實際上哈蘇是土生土長的瑞典品牌,總部位於瑞典第二大城市哥森堡,哈蘇1841年就成立了,但直到1941年才開始製造相機,後來也成為了NASA的合作夥伴,膠片時代哈蘇的中畫幅單反可以說是獨步天下,直至今日,哈蘇也是中畫幅數碼相機的絕對主力之一,中畫幅除了本身原料成本較高之外,哈蘇的價格為什麼無法做到親民呢?今天小胖就從哈蘇相機的製造來說起吧。
首先,比起在大分、宇都宮、長崎、2019年的宮崎,以及中國大陸還擁有多個工廠的佳能來說,哈蘇的經營規模實在是小得可憐,佳能僅僅宇都宮工廠就有1700名員工,僅加工車間就佔地20畝,而整個哈蘇在全球也就180名員工,哥森堡工廠只有40人左右,其中30人負責製造哈蘇相機,所以哈蘇相機,還真是不折不扣的純手工組裝。
當然,組裝相機的配件是外包給瑞典本土的工廠製造,為了提高生產效率,H6D和X1D的不少零部件都是通用的,但即便如此,這麼少的人全手工組裝,產能可想而知,而且瑞典的人工勞動力成本又非常高,再加上裝配機身可不是隨便街上抓個人就能做,所以這一切就決定了哈蘇相機不可能賣得很便宜,規模經濟的定律是無法違背的。
接下來我們看看一台哈蘇相機是如何誕生的吧,首先是鏡間快門,這是中畫幅相機常用的快門模組,比起焦平面快門來說同步速度不設限,快門是多少就能做到多少,而目前的焦平面快門同步速度主要是1/250秒,純電子快門甚至只能做到1/20秒。不過鏡間快門也會影響通光量,尤其是大光圈時。哈蘇HC、XCD鏡頭均是鏡間快門,原始配件就是上面這個做好了安裝孔位的圓形塑料基座,X1D用的是20mm直徑快門,配備1個壓電馬達來控制光圈(如下圖),28mm快門需要用2個馬達,再次提醒,這些安裝步驟都是人工操作的!
快門組裝完成後,工人會先手動測試快門彈性力度(如上圖),在快門測試達標後就進行光圈的鉚接,每一片光圈都是手工鉚接,清潔灰塵後加裝到剛剛做好的快門組件上。然後就使用準直器對快門精度和穩定性進行測試,同時還會檢查、測量光圈形狀和尺寸,每一個光圈都會以多個不同快門速度來進行測試,除此之外還會在測試台上不停觸發快門一整天來檢測穩定性,僅僅是關於快門這一個部分的穩定性測試就要進行一周,所以哈蘇才敢說H6D系列的快門壽命高達100萬次,2厘米的快門行程0.65毫秒就能實現開合。
接下來是手柄部分,主要是各種按鍵功能的布線與電池倉,當然,依然是全手工。甚至連5000萬像素中畫幅CMOS的安裝與連線也都是全手工完成(如下圖),系統校正和固件的體積非常大,需要一塊32GB的TF卡來進行傳導,遠比我們升級固件時下載的文件要大很多。
上圖的HTS 1.5移軸轉接環也是全手動安裝,每一顆螺絲都用螺紋鎖固粘合劑固定,這個移軸轉接環可提供18mm的平移和10°搖擺,但厚度相對比較大,所以安裝後的有效焦距有1.5倍換算係數。
H系列機身在反光鏡與CMOS之間還有一個橫走式的副快門,同樣是手動把部件一個個逐步安裝上去,然後用測力計進行測試,數值必須穩定在0.9牛,要知道每一顆螺絲的鬆緊都會影響到這個數值大小,所以純手工製造需要非常豐富的經驗,也相當花時間,培訓一名新裝配工需要的時間就更多了,而這一切最終也都體現在了它的製造成本上。
雖然像H6D這樣的機身會給人比較龐大的感覺,但它的內部其實非常複雜,需要把裝載CMOS的PCB、副快門、反光箱、自動對焦模塊、鋼製卡口都塞進去,同時還有一大堆連接線……安裝完成後再放到外殼裡,並組裝手柄。而且為了不影響自動對焦的工作,機身的長度公差不能超過0.02mm,安裝完成後還得在檢測儀上檢測自動對焦模塊和反光鏡位置
在機身安裝完成並通過人工測試後,就需要與機器校準,畢竟大多數時候哈蘇都是生產力工具,有些太精密的光靠人工還是不行。每一台相機都會單獨針對CMOS進行清潔、檢測壞點並進行色准、動態範圍和亮度回饋測試,每台相機都有專屬的校準數據都會在工廠進行記錄,方便出廠前和售後返修使用,這個校準過程每台機器都需要1小時左右,如果出現問題,就需要返回到前序產線進行調整檢修。
除此之外,每台相機的色彩校準文件也都保存於機內,所以每次啟動的時候需要等待一小會兒進行載入,而這個色彩校準需要在實驗室拍攝700張左右的照片來進行調試。
通過這一系列測試後,工人還會對它的進行一些實拍測試,順便對音頻系統等周邊功能進行檢查,還會把機身放入黑匣中,人工檢測機身裝配接縫是否密實,LCD是否會漏光。最後再交由專人進行機身的最後檢查並清灰裝箱。可以看到在整個製造流程里,人工幾乎佔據了90%的工作任務,所以哈蘇相機的產能很低,成本很高,此消彼長之後,價格自然水漲船高。相對而言小胖還可以給大家簡單介紹一下佳能的鏡頭工廠,比起機身,即便是L級紅圈鏡頭,也會大量利用機械加工,甚至在工廠內為產線配送元件也都是由機器人代勞(如下圖)。
以16-35mm F2.8 III為例,它除了非球面鏡片之外,其餘鏡片均是全程機械自動打磨,裝配的過程也有50%是由自動化流水線完成(包括精度要求非常高的對焦定位電刷),佳能預計在1年內,也就是今年2018年中旬就把這條產線的裝配自動化比例提升到80%,全部生產步驟里只有10%需要人工干預,這無疑會非常大幅提升生產效率。
但小胖想說的是,高度機械化與高度手工化其實都有著自己的可取之處,就說佳能,也並不是所有產線都是高度自動化,廣播級、電影級鏡頭就因為製造工藝過於複雜,而必須以人工裝配為絕對主力,這類產品算是專機專用,從設計到生產都以那非常小的一小戳用戶需求為主,比如電影鏡頭,都不說在呼吸效應、暗角、畸變等方面都需要通過鏡頭端來增強設計而不能依賴後期,甚至長度都得做到類似,如果鏡頭長短不一,那麼每次換鏡頭就需要調整遮光斗和膠圈的位置,在使用斯坦尼康的情況下一旦改動遮光斗的位置,整台系統都需要重新調平衡,所以越是高端鏡頭對設計的細節就抓得越緊,這時候機械加工只適合做單純指令高度重複工作的特性就不太好使了,所以還得靠人工,因此這些行業級產品即便是佳能索尼尼康大疆,價格也完全不輸哈蘇的,這一點大家可得拎清了。

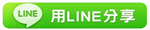
※HiFi是玄學?從小胖9000塊新買的音頻播放器說起
※從對焦看單反末路:佳能尼康轉型無反只是時間問題
※披著運動相機的外殼探索未來:索尼RX0相機評測
※續談索尼A7R3:操作體驗、高感、抖像素與4K視頻
TAG:玩機小胖 |