汽車發動機製造加工中硬質合金鑽頭的修磨
作 者:張志勇
單位名稱:哈爾濱東安汽車發動機製造有限公司
文章來源:《金屬加工》(冷加工)2017年第8期
隨著汽車製造業高速切削技術的發展,原有的普通高速鋼刀具已不再能適應這樣的高速高效加工,取而代之的是大量的硬質合金刀具的應用。
1.硬質合金的組成及牌號
硬質合金是一種主要由硬質相(碳化鎢、碳化鈦等碳化物)和粘結相(鈷、鉬、鎳)組成的粉未冶金產品。其常溫硬度可達78~82HRC,能耐850~1000℃的高溫,ISO中分為K、P、M三個牌號系列。K類主要加工短切屑的黑色金屬、有色金屬及非金屬材料,例如缸體、缸蓋大部分使用K10牌號的硬質合金。P類主要加工長切屑的黑色金屬,例如曲軸使用P20牌號的硬質合金。而M類具有了前兩類硬質合金的優點,因此又稱通用硬質合金牌號。
2.硬質合金刀具磨削的重要性
硬質合金刀具雖優於高速鋼,但硬質合金製成的整體刀具成本也相應的升高。為控制生產成本及對加工效率和加工質量控制的要求,刀具的修磨就顯得由為重要。據統計,刀具修磨可有效降低刀具本錢的30%~50%,並能有效降低消費本錢的1%~2%。刀具修磨時要保證刀具獲得技術規範要求的前角、后角、刀尖角、橫刃、前刀面和後刀面的形狀精度、表面粗糙度以及所需要的刃口處理,對於多刃刀具要保證各齒的跳動量一致。不同的刀具修磨要求是不同的,需根據不同的刀具採用合適的修磨方法和進行相應的控制。
3.機床及砂輪的選用
目前市場上應用比較廣泛的數控工具磨床多數源於進口,品牌主要來自德國等工業發達國家。面對眾多品牌知名、功能強大、價格昂貴的機床,如何才能根據自身的需求做出適合的選擇,這就需要對數控工具磨床的本身有所了解。在國內一些大型機械加工,汽車等領域的企業引進很多知名品牌。如:德國生產的瓦爾特、德克、舒特、薩克;美國生產的哈斯、星牌;澳大利生產的安卡;瑞士生產的伊瓦格等。我公司採用瓦爾特和薩克進行發動機生產中刀具的修磨工作。
刀具的修磨的過程,實際上也是一個強力磨削加工的過程,因此砂輪的選擇是否合理直接關係著刀具修磨後的質量及加工效果。修磨硬質合金刀具的砂輪磨料為金剛石,結合劑為樹脂結合劑、濃度為C100、而粒度的選擇要兼顧修磨表面粗糙度、磨削效率,原則上是在滿足表面粗糙度要求的條件下,選用儘可能粗的粒度。例如修磨後刀面砂輪粒度一般為D64,而修磨前刀面粒度就要小一些,為D46或微小磨料。鑽頭磨削所使用的砂輪形狀一般為平形砂輪代號為1A1、1V1修磨容屑槽、前角、階梯;碗形砂輪代號為11A2、12A2修磨刀具后角。
4.鑽頭的修磨
在機械加工中,鑽削約佔25%,是發動機切削加工中修磨需求最多的刀具,也是最適合修磨的刀具,設計時就考慮了修磨的需求。對預加工或一般的孔精度而言,鑽頭的修磨次數可多致20次,對精度要求較高的情況一般能修磨5次。鑽頭修磨的狀況和質量控制水平的高低對切削加工過程的影響特別明顯。鑽頭修磨需按不同加工需求對鑽頭的橫刃、主切削刃進行修磨,而主要是刃磨鑽頭的後刀面,通過修磨後刀面恢復鑽頭主切削刃的切削能力。鑽頭修磨過程中,要跟據鑽頭加工的工件材料選擇修磨不同的橫刃,在實際使用中有如圖1所示幾種橫刃形式。
(1)缸體鑽頭的修磨。缸體的材料是鑄鐵,鑄鐵是典型的脆性材料,切削生成崩碎切屑。在修磨過程中後刀面一般修磨成2個后角。第一后角一般為8°~15o,第二后角一般為20°~32o;前角一般為o或較小的負值。在實際加工中鑽頭一般為直槽鑽,所以取o。
需要值得注意的是第一后角的寬度,對於鑽頭來說由為重要。因為鑽頭鑽心處切削刃前角為負,切削時產生擠壓,切屑呈粒狀並被壓碎,導致鑽削軸向力增大。如果第一后角寬度修磨成整個橫刃寬度,橫刃區的前角絕對值較大不利於延長刀具壽命。例如我廠原4G1缸體刀具的第一后角寬度就為整個橫刃,刀具在加工到壽後出現鑽尖崩刃偶發折斷現角。後將第一后角寬度改為橫刃的1/2,由於第二后角大於第一后角,橫刃區的前角絕對值變小,減小了軸向力此問題不再發生。
缸體鑽頭橫刃的修磨一般採用N形修磨,起始角度一般為5o,容屑槽的切入角度為20o,容屑槽切入角過大會導致切屑排出困難,使鑽頭折斷。鑽頭在修磨完成後還需要進行刃口處理,因為剛修磨的鑽頭切削刃過於鋒利,其強度減弱,在較大的切削力作用下會破損。一般缸體鑽頭會用含磨料的毛刷進行輕微的倒圓處理。
(2)缸蓋鑽頭的修磨。缸蓋的材料是鋁合金。鋁合金強度和硬度一般較低,塑性較小,對刀具磨損小易於加工。但由於鋁合金熔點低,在切削高溫高壓下容易粘刀,產生積屑廇嚴重,阻礙切屑順利排出。為避免積屑產生,刀具的后角較大,前角為正值。一般第一后角為15o、第二后角為32o、前角為3o。這樣磨出的刀具切屑刃鋒利,切屑較薄,減小切削變形,抑制積屑廇產生。鋒角要比缸體鑽頭大,一般取130°~140o,鋒角加大後,切屑層公稱厚度增大,切屑變形小。
同時,使切屑流出方向有利於沿刀槽排出。橫刃採用X形加圓弧形式修磨。橫刃盡量磨窄,減小軸向力,降低切削負荷。修磨時小角度切入圓弧退出,圓弧退出是為了讓刀具排屑槽處空間加大,因為鋁合金的切屑比較鬆散,所佔空間體積較大,如果排屑槽處空間太小不利於排屑。在修磨橫刃排屑槽時砂輪粒度一般較小,因為這樣可以使前刀面修磨的表面粗糙度值變小,以減輕積屑廇產生,必要時可做鏡面處理。加工缸蓋的鑽頭需要切削刃較鋒利,以減小積屑廇產生,所以大多數情況下不對修磨後的刀具切削刃進行倒鈍等處理。
(3)曲軸鑽頭的修磨。曲軸的材料是鍛鋼。鍛鋼強度和硬度較高,屬長切屑黑色金屬,切削不易折斷,對刀具磨損較大。刀具後刀面一般採用鏟磨方法修磨成圓弧后角,后角為10°~14o。前角一般為負值,有利於切屑折斷。
例如曲軸平衡鑽,最初前角為3o,切屑不易折斷,加工過程中極易纏繞在鑽頭上導致無法加工。後將前角改為-6o,切屑效果如圖2所示,此問題不在發生。鑽頭鋒角一般為140°,鋒角加大有利於切屑沿螺旋槽排出。刀尖處進行倒角,一般為90o,刀尖角增大後刀尖的強度和散熱條件得到改善,但倒角寬度不易過大,如果太大切削厚度減薄,不利於切屑折斷。橫刃採用R形修磨,主切削刃處為圓弧狀,各點的刃傾角不同有利於切削的折斷排出。
由於為增加切削刃強度和承受切削力的能力,修磨後的鑽頭需要用油石鐾出負25o的倒棱,或對切削刃進行倒圓處理。倒棱寬度和倒圓半徑要小於鑽頭的進給量,總之刃口一定要強化處理。加工曲軸的鑽頭到壽後,往往磨損比較嚴重,以原有的刀具修磨量(0.3~0.5mm),已無法將由鑽削過程中的高溫而引起局部材質變化加工性能下降的部份磨掉。那就需要先將刀具前端截去一段,一般約為1~2mm,再進行修磨,生產實踐中已有多次實例表明,如果不截去前端已受影響的部份,重新刃磨後的鑽頭即使刃形磨得再好,也很容易發生崩刃,導致鑽頭折斷或生產出不合格品。
5.結語
在實際生產過程中,鑽頭的修磨一定不要局限於刀具圖紙的幾何參數。修磨人員必須要了解刀具切削的材料特性,加工位置的形狀及狀態,刀具的切削參數。以此來確定刀具修磨的幾何參數,只有這樣修磨後的刀具才是最好的狀態,才能達到最高的壽命。同時刀具的自主修磨也降低了發動機的製造成本。
聲明:本文所用視頻、圖片、文字如涉及作品版權問題,請第一時間告知,我們將根據您提供的證明材料確認版權並按國家標準支付稿酬或立即刪除內容!
機工刀具世界
致力於指導製造業一線技術員工
合理選用數控刀具
介紹刀具行業最新技術進展
推薦最新數控刀具產品
為製造業創造價值
《金屬加工》出品

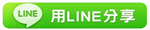
TAG:機工刀具世界 |