數字主線在T-X教練機和新中型客機研製過程中的應用
作為數字化研製的先驅以及數字樣機技術發展的重要推動者,近年來,波音公司積極推動數字主線技術的發展,實現了從2D圖紙文檔,逐步走向基於模型驅動的數字化企業(MBE)。波音公司利用先進建模和模擬技術,構建了從基礎材料、設計、工藝、製造到使用維護,覆蓋產品全生命周期的以統一的模型為核心的產品設計體系。目前,數字主線技術已經廣泛的應用於T-X教練機以及波音新中型客機(NMA)的設計與研製中。
一、數字主線在T-X教練機中的應用
波音公司通過建立DELMIA數字化平台對產品全生命周期進行數字化預測與反饋,該平台包括面向製造過程設計的DPE(DigitalProcessEngineer)、面向物流分析的QUEST(Queuing Event Simulation Tool)以及面向裝配過程分析的DPM(DigitalProcess Manufacturing)3大主要模塊。各模塊之間可以通過PPR(Process-Product-Resource)連接,形成了一套從設計到製造完整的數字主線解決方案。該平台可以圍繞T-X教練機的設計過程,定義各種約束條件、界面和需求,以及管理綁定數據、控制成本和進度。數字主線極大地改變了在研製過程中臨時改動的事項,包括研製時間、工程誤差、工廠停工、質量等。
圖1 T-X教練機研製全生命流程示意圖
為了便於產品的數據管理和構型控制,波音公司使用數字主線技術將T-X教練機分成了幾千個模塊,在構型控制時,不同的飛機產品由不同的模塊組成,並相應地對生產流程(設計、製造、裝備、檢測)劃分成排列在數字主線上的4個精簡作業流程TBS、TBS1、TBS2(A、B)和TBS3。根據模塊性質,不同模塊分屬到4個精簡作業流程中。通過數字主線的應用,產品數據能夠暢通地在飛機製造、裝配廠的生產下游、飛機的使用和維護等環節傳遞。
1.設計階段(TBS1)
在設計階段,波音公司通過DELIMA平台將CAD系統的設計數據與製造資源(2D/3D)進行結合,然後對整個製造和維護過程利用3D模擬引擎進行模擬和分析,最後得到可視性、可製造、可維護和最佳效能等方面的最優化數據。數字主線系統體系結構包括面向製造過程設計的DPE、面向物流分析的QUEST、面向裝配過程分析的DPM、面向人機分析的Human、面向機器人模擬的Robotics和面向虛擬數控加工模擬的VNC。
2.製造階段(TBS2(A))
數字主線將T-X教練機製造階段分為工藝規劃、資源建模和模擬、數字化製造基礎三個不同的階段,並基於DELMIA模型進行產品布局規劃、工藝與資源規劃、時間安排以及成本分析和產品評估。在此基礎上,利用數字化建模技術配置機器人工作單元、離線編程,然後進行工廠流程的模擬、數控加工和監控應用數字主線模擬平台,直觀地分析了產品的可裝配性,在裝配過程中再結合人因工程分析,進一步對裝配的工藝流程進行改進和優化。
通過數字主線的應用,能有效避免產品設計完成後通過使用樣機生產來驗證的資源浪費;產品設計在生產和裝配中的問題也能在DELMIA軟體虛擬的模擬環境中檢測出來,使得產品設計和工藝方案能及時進行修改,達到製造資源和生產工藝的虛擬協同設計的目的,使得製造和調試時間大量縮短;利用DELMIA中具有強大分析功能的人機工程模塊,在整體裝配過程中對工人進行定性的人因分析,促使工藝人員設計出操作更舒適和動作更經濟的作業標準。通過數字主線技術的應用,能夠在3D數字環境中完成一個整體的虛擬製造流程。
3.裝配階段(TBS2(B))
在裝配階段,波音公司利用數字主線對裝配過程進行預判,通過使用特徵識別模擬軟體DELMIA對裝配進行模擬,在模擬中分析了工業機器人的可達性、可焊性以及各產品對象之間干涉、間隙的分析,直觀地觀察到機器人的空間運動狀態以及機器人實現焊接的動作操作;結合應用DELMIA軟體中的各模塊對裝配、焊接進行工藝規劃、模擬,為工業機器人的合理布置和運動軌跡的最優化提供了可靠的依據,大幅度縮短工時和節約資源,提高了企業數字化製造水平。
4.檢測階段(TBS3)
綜合運用數字主線中DPM模塊和人機工程模塊對工人、維修設備、工具設備和環境兩兩之間進行空間干涉和碰撞的分析、人機工效的評定,及時對維修過程中的不合理維修操作做出調整,改善維修人員姿勢舒適度。從數字主線應用于飛機維修的案例中可知,數字主線優化了維修工程,縮短了維修時間,拋棄了用物理樣機為平台的維修方式,降低了維修的成本。
二、數字主線在波音中型客機中的應用
在2017年的巴黎航展上,波音公司首次公布了新中型客機(NMA)的研製計劃及部分細節,新項目將在2018年年底或2019年年初啟動,2020年開始設計,2021-2022年開始生產零部件,2023年開始總裝並下線,2024年開始飛行試驗和取證,2025年投入商業運營。
波音新中型客機(NMA)的研發將吸取787研製過程中的經驗教訓,數字孿生和數字主線將是NMA項目的關鍵。波音通過多學科優化設計,對設計、生產和試驗等各個環節進行了深入而全面的分析,力爭在數據協同與數據交換方面取得新進展
1.數據識別與反饋方面的應用
為了克服數字主線中存在的數據識別的問題,在NMA項目中,波音公司使用數字主線的內容(has—Content)屬性描述檢測反饋的數據,使用鏈接(has—URL)屬性描述檢測用到的外部鏈接,使用對象關聯(has—reliance)屬性用來描述特徵與構型反饋數據之間的關聯關係。由此,構建的基於本體的產品數字孿生模型可以與相應的構型數據關聯在一起,實際的物理產品研製過程中的相關技術狀態數據也可以與之建立關聯關係,從而可以基於產品數字主線+數字孿生模型實現構型數據的紀實,進而實現全三維研製模式下模型驅動的構型數據快速追溯和快速響應。
圖2 NMA客機數字孿生示意圖
通過構建基於數字主線的NMA機體數字孿生模型,開發分析框架,並綜合利用先進技術手段,實現了多尺度模擬和結構完整性診斷;配合先進建模模擬工具,實現了殘餘應力、結構幾何、載荷與邊界條件、有限元分析網路尺寸以及材料微結構不確定性的管理與預測。
2.數據交換與協同方面的應用
波音公司NMA項目為新中型客機研製項目專門構建了基於數字主線的全球協同設計環境GCE(Global Collaborative Environment),如圖1所示。通過GCE,波音公司構建了NMA飛機的邏輯相關的單一產品數據源(Logical Single Source of Product Data,LSSPD)。LSSPD使波音NMA飛機不僅具有完整的幾何數字樣機,而且具有性能樣機,製造樣機和維護樣機,較好地解決了產品數據的管理和交換問題,便于波音公司與分布在全球的合作者能跨地域、跨時區順利地進行產品各項功能的協同研製工作。
圖3 基於模型定義的全球協同網路環境GCE
結束語
現代飛機產品數字化製造過程的實質,是對一個產品進行並行協同的數字化建模、模擬模擬和產品定義,然後對產品的定義數據從設計的上游向零件製造、部件裝配、產品總裝和測量檢驗的下游進行傳遞、拓延和加工處理的過程。波音公司通過使用數字主線技術使飛機產品的加工/裝配狀態和運行狀態能夠實時、精確地反映在虛擬空間中,同時基於數字孿生形成的優化決策信息,通過數字主線傳遞到產品生產現場,實現了信息的雙向流動,使得利用信息的反饋機制對產品製造進行精確控制成為可能。
波音公司通過產品數字主線技術集成設計/模擬、生產製造及使用,能夠實現產品業務流程的全程可視化,規劃細節,規避問題,優化整個系統,使得工作人員可以適應全新的工作方式、獲得更高的靈活性,從而完成最艱巨的任務。數字主線的實現,為虛擬空間和實體空間深度融合、平行發展和平行控制提供了實施途徑。
(作者:北京航天情報與信息研究所 董皕喆博士)
此文為本微信公眾號原創,如轉載請註明出處
【關於我們】感謝您關注、閱讀與分享【航天縱橫】。【航天縱橫】依託於北京航天情報與信息研究所發展戰略與系統工程研究中心,圍繞航天軍事、軍民融合、國防科技、系統工程等領域,聚焦國內外最新政策解讀、戰略與管理諮詢研究成果、世界航天軍工信息等前沿動態,傾力打造為航天產業領域一流智庫。

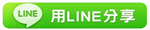
TAG:航天縱橫 |