乾貨!金屬3D列印材料性能以及典型應用
什麼時候選擇金屬3D列印較為適合呢?
數量——傳統製造更適合大規模生產,而3D列印對於小型複雜或特殊的液壓元件可能更經濟或更實用。
節省時間——削減工序,如CNC加工,可能需要30到60天的生產時間,從金屬棒料中生產一個部件,或者需要6到12個月。對於3D列印,液壓元件可以在幾天內按需列印。如果列印的零件需要加工,交貨時間可能會增加到一到兩周。
原型——3D列印的原型設計可以同時產生不同的原型變體,從而使設計方案的評估成為可能。
材料選擇——液壓元件必須具有足夠的強度和耐腐蝕性,以安全地處理液壓系統中通常存在的高壓。3D列印技術可以提供更廣泛的選擇的材料,包括不鏽鋼(AISI316L),鋁,鈦,鉻鎳鐵合金(Ti6Al4V)(625或718),和馬氏體鋼。
材料性能如何?
由於金屬3D列印在液壓系統領域的應用是相對較新的,它提出了一個問題,即3D列印件的材料特性如何與傳統工藝相比。雖然典型的機械性能,如抗拉強度,屈服強度和彈性模量似乎是可比的,根據材料的選擇,液壓系統中經常遇到的高壓值得額外考慮。
通過適當的材料選擇和設計,部件可以承受這些壓力,但也可能遇到很難適應的衝擊和壓力脈衝。例如,歧管通常由球墨鑄鐵或其他韌性材料製成,以處理這些脈衝,但這些材料不利於3D列印的製造過程。鐵和碳鋼材料也屬於這一類,因為原料材料必須以粉末形式存在。
複雜的液壓元件,通過金屬3D列印可以納入細節,重量和尺寸減少,而不影響性能。這對於傳統加工工業來說是極其困難,甚至是不可能實現的。
典型應用
許多類型的液壓元件已經用金屬進行3D列印生產。例如,Aidro使用不鏽鋼列印液壓閥塊以控制單作用氣缸(圖1)。該公司能夠做到節省空間和優化其內部通道,與傳統組件比較,擁有更高的流量與較低的壓力損失。由於不需要輔助鑽孔,也消除了外部泄漏的可能性。
此外,使用3D列印設計與改進生產了一個可堆疊的液壓閥(圖2)。直接操作減壓閥是由鋼和鍍鋅製成的,以防腐蝕。當Aidro的客戶有小數額的閥門需求時,數控加工對於交貨時間和成本來說是不可控的。相反,閥門使用3D不鏽鋼重新設計生產,重量減輕了60%。其結構牆和原來相比一樣結實,在250bar壓力測試下新的設計結果具有可比性。
Domin的總經理MarcusPont說,新的伺服閥在尺寸上、效率以及質量上相比目前設計有了很大的提高,同時保持了從簡化製造中獲得的有競爭力的價格。這些性能改進是基於與當前最先進的伺服閥的比較。
相比具有顯著的競爭產品,Pont表示Domin伺服閥提供了25%的額定流量改進,並減少20%的泄漏量。它也減少了25%的體積、15%的重量,並且減少了40%的零件,簡化了製造。
Aidro提供的另一個例子是一個應用於農業機械的液壓集成件(圖4)。這個歧管控制雙作用氣缸,有兩個電磁閥和兩個先導式止回閥。3D列印歧管的功能與它所取代的單元完全相同,但尺寸比以前的歧管少一半,輕75%。該部分包括AlSi10Mg6000系列的鋁合金,將良好的強度和熱性能以及輕量化和潛在的靈活後期處理有效的融合在一起。它通常用於薄壁和複雜幾何形狀的零件生產中。
Aidro的tacconelli的報道,壓力測試顯示的力學性能——如拉伸強度、伸長率、衝擊韌性等,相比傳統材料製成的歧管甚至要更好。由於內部通道在十字角中彎曲形狀沒有90轉角,操作性能相當於甚至超過傳統的部分。
賓州州立大學的CIMP-3D,用3D列印將液壓歧管列印成一塊(圖5)。它的重量比它更換的17個組件少了70%,但經受住了同樣的壓力和疲勞測試。
Aidro重新設計的閥芯是3D列印新的孔的形式,與方孔代替圓形孔(圖6)。這增加了閥芯內部油路的面積,降低了壓降。
這些只是一些金屬3D列印擴展了在液壓領域改進組件設計和生產的潛力的方法。據Infinium全球研究報告稱,2017-2023年,全球金屬3D列印市場將以33%的年複合增長率高速發展,液壓應用有望成為這一擴展領域的重要組成部分。

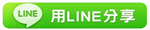
※3D微納米列印技術介紹
※SLM解決方案為奧迪W12發動機3D列印罕見零件
TAG:魔猴網3D列印 |