120°或90°的螺紋孔倒角和沉頭孔如何避免毛刺的形成!
對內螺紋孔進行倒角或沉頭孔的目的通常是為了避免產生凸起的毛刺,毛刺會妨礙適配件與平整的工件表面之間固定。另外,當裝配件壓在毛刺上時,毛刺將被壓下,從而導致內螺紋變形並增加螺紋錯扣的可能性。
在零件圖上繪製倒角或沉頭孔也可以幫助螺栓正確對齊或插入。在待鑽孔所在的位置加一個倒角或埋頭孔可以幫助入鑽。由於這些原因,絕大多數螺紋孔需要某種類型的倒角或埋頭孔。因此,這是最常見的加工工藝之一,也是通常需要改進的地方。
螺紋孔倒角的角度通常為120°或90°,其中最常見的是90°。有時會在工程圖上指定倒角的外徑和深度。然而,機械師或程序員經常會自行決定倒角孔的深度或外徑。
頭孔和倒角可以選用多種形式,或者直接由工程師決定
在一些經典的機械師經驗法則中,最常見的做法是加工比螺紋大徑大0.010英寸-0.015英寸(0.254mm-0.381mm)的倒角直徑,這將消除毛刺並提供足夠的深度引導即將裝配的螺栓。
加 工 方 法
加工倒角或沉頭孔有多種方式,這些方法的加工效率不同。過去常用的方法是在初鑽之後,在待鑽孔處加工一個120°或90°的倒角。
許多機床廠採用90°角的數控點鑽來完成點鑽、沉頭孔及倒角,不僅節省了換刀時間,也降低了刀具成本。數控點鑽頭作為引導工具,在鑽孔之前被用來加工一個90°的夾角。雖然這種方法方便,但若使用較新的高滲透率硬質合金鑽頭來鑽孔時,則不建議採用上述方法。因為這類硬質合金鑽頭的頂角是140°。在使用了90°的點鑽之後,再利用140°硬質合金鑽頭進行鑽孔加工會導致在該硬質合金鑽頭上造成切角並使刀具更快失效。若採用硬質合金鑽頭鑽孔,必須改變使用刀具的序列。
此時,正確的刀具序列應為:鑽孔、倒角(或鑽沉頭孔)、點鑽。在這種情況下,使用120°或90°角度的沉頭鑽或倒角銑刀是最佳選擇。通過選擇適當的刀具序列,硬質合金鑽頭的刀具壽命將顯著增加。
在進行沉頭孔或孔的倒角加工時,應特別注意對刀。錯誤的對刀將對零件的質量和功能產生很大的負影響。使用倒角銑刀時,可以通過圓弧插補進行圓形倒角的加工,但這可能不是直接倒角的最佳工藝。相反,傳統的高速鋼沉頭孔是專門為倒角而設計的,但它們並不適用螺旋圓弧插補刀具路徑。
合 並 操 作
對孔加工倒角的最有效、最快捷的方法是使用同時具備了鑽削和沉頭的功能的階梯鑽。由於該鑽頭具有90°的沉頭階梯角度,利用這種階梯鑽進行加工可一次性完成鑽孔和沉頭加工工序。將兩個加工操作合併為一個,不僅可減少換刀時間、循環時間和刀具庫存,而且保證倒角的與底孔同心。
如果將階梯鑽作為鑽孔的首選方法,必須使用改良後的標準鑽頭,階梯鑽的螺紋小徑磨削成一個標準的單直徑鑽頭的直徑大小。螺紋小徑的鑽芯厚度可能會出現過大的情況,並影響切屑排出。出於易於清理的目的,螺紋小徑一般沒有刃帶,同時這也會引起外徑上出現過大的摩擦,從而降低刀具的性能。
階梯鑽,尤其是硬質合金階梯鑽,應該是由硬質合金材料棒加工而成,而不是對現有刀具進行修磨而成,以保證鑽芯和刃帶符合要求。標準的階梯鑽是存在的,一些刀具製造商能夠迅速的提供這些產品給最終的用戶,並可用於加工具有不同螺紋孔深度的盲孔。
工藝改進是先進位造商永恆的目標。儘管攻螺紋前製備倒角和沉頭孔是常見的結構,但是加工順序並不是一個標準化的工藝,同其他大多數工藝一樣,仍需要精益求精。

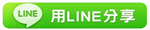
TAG:UG編程學習 |