革新型的輕量化開發——輕量化整體解決方案之道
革新型的輕量化開發
輕量化整體解決方案之道
前言
純電動汽車每減少1Kg,整車就可以少裝0.021KWh容量(續航250Km的電池),整備減100Kg,可以增加續航里程10%,節約電池成本約15%-20%。可以說相對於傳統燃油車,新能源汽車更迫切地需求輕量化。
2016年12月29日四部委聯合出台的《關於調整新能源汽車推廣應用財政補貼政策的通知》正式將補貼標準與電池包 「重量比能量」掛鉤:
而2018年客車補貼標準為:
不難看出,補貼迅速退坡,而對於系統比能量的要求則顯著提升。要在短時間內提升系統比能量,提升電芯單體能量密度難度較大,所以PACK輕量化成為了最佳選項。
不少開發人員認為PACK輕量化核心就在於電池箱體減重,而電池箱體減重無非就是更換材料,減薄壁厚。於是全鋁箱體、SMC複合材料箱體等各種新型箱體方案應接不暇。最終不是比誰更安全,而是比誰更輕……那我們就要思考一個問題:如果是後補貼時代,不再參考系統比能量給予補貼,還會犧牲安全性想盡一切辦法做更輕的箱體嗎?
合理的PACK輕量化應該從整個系統層面出發,做一體式輕量化設計,目標是配合整車的輕量化,如下圖所示:
1
電芯層面:
單體電芯「儘可能」做大。我們看到Tesla電芯由18650切換為21700;方形電芯尺寸也在不斷增加,鋁殼變薄(鎂鋁);軟包電芯單體也有做大的趨勢。
2
模組層面:
標準模組實現一體化設計,集成更多的部件功能。如將熱管理、信號採集等高度集成式設計;模組本身結構作為PACK結構的一個構成部分等設計方案。
3
箱體層面:
箱體的拓撲優化和模擬驗證先行。在正向開發的初期,利用模擬技術,及早進行結構優化(如拓撲)和設計驗證;在開發後期,模擬結合實際測試來確定最終的方案。
4
系統層面:
電池包與底盤一體化設計。在此,主要是避免過度防護,整車應協同實現輕量化,盡量避免傳統車底盤改電動車的方向。
由此可見,單純減重電池箱體對整車的輕量化實際上作用非常有限,電池箱只是整個輕量化方案中的很小的一部分。
以上是從整個輕量化PACK系統性、頂層地來考慮其輕量化方案,除了一體式輕量化設計以外,也必須要突破常見的成型工藝。對於此,利用最新的攪拌摩擦焊技術將給PACK輕量化開發帶來了全新的解決思路。
相比於其他的成型工藝技術,攪拌摩擦焊擁有諸多優勢,這裡不一一累述,重點對以下問題進行探討:
1
一體式底盤
因為寶馬、比亞迪等主流電動車使用,乘用車鋁擠攪拌摩擦焊電池箱(托盤)風靡一時,但經過比對,單純鋁擠攪拌摩擦焊電池箱減重優勢並不十分明顯。其實綜合考量是因為這些車企設計了底盤一體式承重電池箱,並不是單純考慮電池箱體減重,箱體本身作為底盤結構的一部分,所以綜合來說整備減重明顯,但電池箱可能反而不減重。
2
全鋁車身
在全鋁車身連接領域,使用攪拌摩擦焊點焊技術可以替代專用鉚釘鉚接,使得整備質量及製造成本明顯下降。
3
一體式電池箱
傳統電池包液冷方案需要使用大量獨立的水冷板,這無疑增加了系統重量,而鋁擠攪拌摩擦焊的應用使得集成水冷板的一體式電池箱成為可能,這將大大減少系統重量,使得系統輕量化水平得到顯著提升。
4
輕量化電連接
在PACK及整車電連接領域,因為銅鋁攪拌摩擦焊擁有內阻極低、連接強度高等諸多優於傳統激光焊接、超聲焊接的性能,使得低成本、輕量化的鋁排替代銅排成為大趨勢。
從以上可以看出,一體式的輕量化設計結合攪拌摩擦焊的應用,能夠為電動汽車的輕量化提供一個全新的、切實可行的解決方案。從目前已應用的實際產品案例來看,在實現「輕量」的基礎上,也可以達到降本提質的效果。本月4月21日,在蘇州科尼普的公司戰略轉型發布會上,其總經理苗東方將會攜數位行業技術專家,對一體式輕量化設計的具體關鍵技術、以及實施案例經驗進行深入探討和分享。
結語
輕量化是一個系統工程和系統的過程,需要從整車一體式輕量化角度設計和布局,引入虛擬模擬無樣件研發過程,使用先進位造工藝和特種裝備,結合實際試驗驗證,協同實現輕量化,最終達到節能降本的目的。單純從PACK或電池箱體減重來思考輕量化,顯得過於片面,難免陷入「難以再降」的困境,也並不是新能源汽車輕量化的初衷。

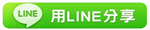
TAG:連線新能源 |