片狀弧形結構件成形回彈控制
本文摘選自《模具工業》2014年第11期
作者:鮮光斌,羅琳
(奇瑞汽車股份有限公司)
製件成形存在的問題
1
圖1為片狀弧形結構件,材料為B340/590DP,料厚1.2mm,該製件拉深深度淺、角度大,在成形中容易產生回彈,部分區域(見圖2所示橢圓區域)回彈量達到14mm以上,導致製件在焊接匹配過程中存在干涉和間隙問題,如圖3所示。
圖1弧形結構件二維圖
圖2 製件成形回彈區域
圖3 製件在焊接匹配中出現的問題
製件成形時回彈產生原因
2
經分析,引起製件成形時回彈主要因素如下:
01
製件結構特徵
製件呈片狀弧形結構,且弧形角度大,成形深度淺,整個片狀體上沒有設置一個加強筋,不利於保證製件強度,因此容易產生回彈。圖4所示為無加強筋的製件三維模型。
圖4 無加強筋的製件三維模型
02
製件材料及厚度
由製件材料B340/590DP、料厚1.2mm可知,製件的成形屬於高強度、高厚度鋼板成形,成形性較差,容易產生回彈。
03
CAE分析水平欠缺
由於CAE分析人員的設計水平不夠,現場實際經驗不足,對回彈問題缺乏深刻認識和處理經驗,未能及時改善衝壓工藝和模具設計以防止製件成形時回彈;或者CAE軟體分析精度不夠,未能精確分析出製件實際的反彈量,從而不能對回彈問題進行預防處理。
04
衝壓工序不合理
製件的衝壓工序為:①落料;②彎曲;③整形、沖孔、分切。該衝壓工序有如下缺點:①採用彎曲成形工藝,成形力相對較小,導致製件成形不充分,從而產生回彈;②由於製件先整形後分切,分切後製件會恢復自由狀態,不受任何約束力,從而容易產生回彈。
圖5 整形模結構
05
整形工藝不合理
圖5所示為製件整形模結構,由圖5可見,製件在模具上的擺放角度並不合理,這樣會導致製件弧形段受力不均,甚至部分區域受不到整形力,影響整形效果。此外,製件部分型面未布置斜楔機構進行側整形,是導致整形效果不明顯的主要原因。
製件成形時回彈控制措施
3
針對製件的成形特點,採用如下措施減少製件成形時回彈:
01
增設加強筋,提高製件強度
在考慮布置焊點的前提下,在製件避開焊點的位置儘可能多地增設加強筋,以提高製件強度,減少製件成形時回彈。圖6所示為帶有加強筋的製件三維模型。
圖6 帶有加強筋的製件三維模型
02
採用熱壓成形工藝
隨著車身輕量化的要求,在車身設計中採用高強度、高厚度鋼板已成趨勢,但高強度、高厚度鋼板的成形性較差,容易產生回彈,因此可在條件允許的情況下採用熱壓成形工藝,以提高製件成形性能。
03
提高CAE分析水平
一方面要讓CAE分析人員多去現場了解模具的實際結構、衝壓工藝和機床設備等情況,提高CAE分析人員的水平;另一方面使用模擬過程更真實、精確度更高的CAE分析軟體,不斷提高製件成形分析的精確度,以便提前預防製件成形時回彈,對相應的模具結構和衝壓工藝進行優化。
04
優化衝壓工序
優化後的製件衝壓工序為:①拉深;②修邊+側修邊;③修邊+側修邊;④分切;⑤整形+側整形+沖孔。該衝壓工序的優點為:①拉深工藝能保證製件充分成形,把原彎曲成形工藝改為拉深工藝,是因為拉深模採用壓邊圈壓住板料,在拉深過程中對製件施加的力比彎曲工藝更大,製件的塑性成形更好,能確保製件的拉深成形更充分、成形到位;②將原工序中的先整形後分切改為先分切後整形,即在製件恢復到自由狀態後再進行整形,這樣能很好地控制製件的回彈。
圖7 製件旋轉一定角度後在整形模上的擺放狀態
05
優化整形工藝
為保證製件整形到位,控制製件回彈,提高製件精度,要求整形工序衝壓方向上沒有負角。因此,要想讓整形效果達到理想狀態,需要將製件在模具上旋轉一定角度,以確保製件在整形過程中受力均勻。製件旋轉一定角度後在整形模具上的擺放狀態如圖7所示,此時製件在整形過程中所受整形力更大,能有效控制製件回彈,提高製件精度。此外,在整形模上增加側整形工藝,採用斜楔機構對製件弧形段進行側整形,能有效提高製件整形效果。
微信編輯:野牛
《模具工業》創刊於1975年,是我國最早出版的模具專業期刊,系中國模具工業協會會刊,在我國模具行業具有較高的知名度和影響力,主要報道各類模具先進技術及行業動態等,是交流模具技術、傳播模具信息、宣傳行業廣告的理想平台。
《模具工業》雜誌唯一官網為中國模聚網(www.moulds.com.cn),雜誌投稿系統的鏈接為http://www.moulds.com.cn/magazine/

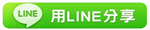
TAG:模具工業 |