精密折彎模具製造工藝分析
高精度的折彎模具在鈑金加工體系中佔據著非常重要的地位和作用,但是在製造折彎模具的過程中,由於各廠家在設備、材料及工藝上的差異,很大程度上造成了折彎模具的壽命及精度差距,因此,本文對摺彎模具生產工藝中的一些相關內容進行了簡要的分析和闡述,希望能在鈑金用戶選擇折彎模具時給予一定程度上的參考。
鈑金加工行業是我國機械製造行業的重要支撐力量,其中折彎加工是鈑金加工中不可缺少的一道工序,每天的模具使用頻率相對較高。但是,在安排折彎工序的過程中,要想有效地提升零件產品的質量和生產效率,非常關鍵的一項內容就是選擇品質優良的折彎模具。本文闡述的主要內容就是如何從生產上實現折彎模具的優良品質。
折彎模具的現狀
我公司專業從事鈑金模具製造及服務20餘年,在企業的發展過程中,充分與數千家終端用戶進行互動。在與客戶的信息交流過程中,了解到目前鈑金用戶對摺彎模具的需求存在幾個難題:國產模具品牌參差不齊,模具質量不夠穩定,精度不夠精密,相比較進口模具有一定的差距;使用進口模具,則價格高昂,且交貨期偏長;若是需求非標模具時,與模具製造商的溝通途徑較少,且時效性較差;行業並沒有執行一個既定的模具標準。導致各廠家之間做的模具不能互換,造成鈑金用戶在使用模具時,會被綁架銷售,選擇空間小。
模具質量的核心要素
材料
折彎模具材料應選擇正規鋼鐵企業生產的42CrMo,相對於其他材料,42CrMo材質有著明顯優異的機械性能。具有強度、淬透性高、韌性好,淬火時變形小,高溫時有高的蠕變強度和持久強度等特點。
市場上的材料還有T7A、T8A,儘管這幾款材料均可以通過熱處理達到一定的表面硬度。但是由於淬火層深度過淺,刀具心部組織過軟,容易變形。由於受價格限制,很多折彎模具材料多採用相對便宜的材料。國外折彎模具採用的材料,耐磨、耐腐蝕及拋光亮度等綜合性能均優於國產材料。這也從根本上影響了國產折彎模具的外觀質量和使用壽命。
熱處理
折彎模具為了得到合格且均勻的硬度,熱處理的工序至關重要。折彎模具要求的硬度為47±2HRC,其含義為模具的表面任何位置硬度應該在45~49HRC之間。並且硬度層的深度單邊控制在10mm以上。
熱處理的大概過程為:首先將粗銑好的毛坯,在端面焊上吊裝環,進加熱爐升溫至880℃,等產品已經整體到溫出爐淬油冷卻檢驗變形量冷校正回火硬度檢測,其中回火保溫時間根據批量而有所不同。完成以上步驟,基本上完成粗銑毛坯的熱處理。
以上步驟有幾個關鍵點:
端面焊上吊裝環進行懸空加熱及懸空淬油冷卻。由於折彎模具的形狀是不規則的幾何形狀,在冷卻時,冷卻不均勻、不等速,會產生較大的變形量,且不可控。因此只有懸空的燃燒方式及懸空冷卻才能有效的使模具變形量達到最小值。由於是懸空狀態下加熱及冷卻,在這個過程中,吊裝環是和模具焊接成一體進爐加熱。如果模具過重,在880℃的溫度下,很容易造成吊裝環與模具之間斷裂。正是由於這個熱處理加熱上的限制,國外廠家及我公司堅持做835mm標準長度模具。模具若是存在熱處理上的缺陷,就會大幅降低模具的使用壽命。
冷校正。在產品出油爐之後,由於模具本身幾何形狀的不規則,造成變形量的不可控。所以,在模具出油爐之後,每一件產品都需要檢測變形量,如果變形量過大,那麼需要冷校正。很多廠家為了省事,會選擇採用火焰槍燒紅的老式辦法進行校正。在重燒的地方,會造成局部組織軟化。在日常的使用上,存在安全隱患。
經嚴格把控熱處理工藝的折彎模具,應該達到以下壽命:在加工2.0mm厚度以下(含2.0mm)的不鏽鋼板、3.0mm以下的冷板(含3.0mm)時,採用6~8倍V槽的折彎下模,刃口的R角可以承受2000000次的頻繁折彎(換算成年數,以一款模具一年使用20萬刀次算,可使用10年),而刃口的磨損在0.03mm之內。低廉的價格是否真的就是性價比高?用最終的使用刀次來體現就會發現,其實並不是那麼一回事。只有專業的熱處理工藝及合格的材質,才能保證模具經久耐用。
精密的數控成形磨削
前兩點提到的模具材料及材料熱處理,主要關乎的就是折彎模具的壽命。那麼對模具的刃口及V槽面的處理方式就是保證模具精度的最關鍵的一道工序。
傳統的磨削工藝對於刃口的磨削辦法為:將砂輪角度人工對半分,磨削完一面,再磨削另外一面,最後R角靠鉗工手動打磨。下模的V槽處理方式也是大同小異,將砂輪修成單V形,越往下磨,V槽就越寬,最後V槽面的R角處手動打磨。這種傳統的加工方式精度差,做不到同型號的一致性,為後續增訂模具增加了互換性的困難。
我公司引進了5台歐洲進口全自動化數控成形磨床,全系配備進口數控系統。使得整個磨削的過程和國外廠家一致。
第一,修整成形砂輪。這個工序完全顛覆了傳統的砂輪修整方式,根據每一個型號的模具對應形狀,修整出對應的成形砂輪。然後進行成形磨削,將複雜的曲面磨削,簡化成簡單的平面磨削原理,從而更好的控制模具的R角、角度、V槽寬度等關鍵尺寸。
第二,粗磨刃口及V槽面。
第三,精磨刃口及V槽面。在粗磨刃口或V槽面的過程中,砂輪會有損耗,所以在精磨前,砂輪會在系統的作用下,自動補償損耗量及自動補償。
第四,光刀。將光刀的次數及砂輪粒度統一。從而可以做到每一條模具的尺寸都是一致的,精確到0.01mm的尺寸公差。
以上四個步驟是一次裝夾同時完成的,可以顯著的提高模具的一致性及穩定性。
傳統的磨削辦法,在整個製造過程中,大部分是人為干預;而數控化的磨削,在整個製造過程中,全程都是設備本身及配套的數控系統在控制產品的尺寸成形及尺寸精度。因此,生產出來模具的一致性及穩定性有著本質上的區別。
由於傳統工藝的缺陷,模具一致性無法穩定。所以國內很長一段時間都是在使用整支的模具。然而AMADA等進口品牌一直在生產標準長度為835mm及500mm的模具。究其原因,就是因為先進的磨削設備及工藝,能夠製造出一致性的模具。從而達到互換拼接使用的效果。也正是國內外廠家在工藝上的區別,造成折彎模具一直以來沒有一個標準的行業規範。各廠家生產的均是本廠的模具尺寸。如果有了一個統一的尺寸標準,鈑金用戶在選擇廠家時,就可以更加自主一點,而不需要遷就某一款模具或某一家製造商。
通快的模具長度標準為500mm,AMADA的標準長度為835mm和500mm,江蘇亞威的配機模具長度為835mm及515mm。在精度能夠保證的前提下,輕便的模具更能提高生產效率,降低生產人員的工作強度。
圖1 常用上模型號
圖2 下模不同的V槽配比
模具型號的歸納
我公司歸納出以下數款常用模具,這些模具是目前市場上最為常用的折彎模具型號。這幾款常用的模具,因為使用折彎機的品牌及參數不同,在基準高度上有部分差異。上模型號對應為A190、A200、A470、A130、L210、#109、#202、#453、#210、#10870(圖1),下模型號根據板厚不同的需求,整理出不同的V槽配比(圖2),但應該以同芯下模為客戶的使用趨勢。
根據終端客戶的反饋,以上歸納的上模型號能夠應付90%以上的標準鈑金件折彎工作。A開頭的上模型號,為基準高度120mm的等高模具。能夠有效降低模具對刀的時間,提高生產效率。同芯下模也是高效的下模系列。在使用不同V槽時,可以直接使用,而不需要調整導軌。
結束語
隨著現在市場的競爭愈加的激烈,人工、材料等硬性成本逐年增加。越來越多的鈑金企業選擇自動化的生產模式,引進更加柔性的自動化生產解決方案。在此過程中,如果折彎出來的產品,展開係數、尺寸等發生改變,會很大程度上影響到後續的自動化生產,造成不必要的損失。本文對摺彎模具的精度及標準做了簡單的介紹,希望能夠幫助到廣大的鈑金客戶。
——節選自《鈑金與製作》2018年第4期

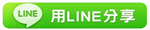
TAG:鈑金與製作 |