江蘇:江蘇省智能製造示範工廠建設三年行動計劃
各設區市經信委,崑山市、泰興市、沭陽縣經信委(局):
為進一步做好江蘇省智能製造示範工廠建設工作,現將《江蘇省智能製造示範工廠建設三年行動計劃(2018-2020年)》印發給你們,請認真貫徹執行。
江蘇省經濟和信息化委員會
蘇經信裝備〔2018〕464號
關於印發江蘇省智能製造示範工廠建設三年行動計劃(2018-2020年)的通知
各設區市經信委,崑山市、泰興市、沭陽縣經信委(局):
為進一步做好江蘇省智能製造示範工廠建設工作,現將《江蘇省智能製造示範工廠建設三年行動計劃(2018-2020年)》印發給你們,請認真貫徹執行。
江蘇省經濟和信息化委員會
江蘇省智能製造示範工廠建設三年行動計劃(2018-2020年)
智能工廠是指基於全面互聯、智能控制、安全可靠的工業互聯網,廣泛採用新一代信息技術和先進位造技術,綜合運用設計生產、檢驗檢測、倉儲物流等智能裝備、軟體和控制系統,覆蓋研發設計、生產製造、經營管理、運維服務等生產全流程、管理全方位和產品全生命周期,泛在連接、彈性供給、動態優化和高效配置製造資源,實現響應時間縮短、資源消耗減少、質量效益提升、運營成本降低、環境生態友好的現代工廠。2015年以來我省大力推進智能製造,已累計創建示範智能製造車間536個,為創建智能製造示範工廠奠定了良好基礎。為深入貫徹落實省委、省政府關於加快推進智能製造,創建一批示範智能工廠,培育一批智能製造領軍企業的要求,結合《江蘇省「十三五」智能製造發展規劃》和智能製造工程實施方案的推進工作部署,現制定江蘇省智能製造示範工廠建設三年行動計劃如下:
一、總體思路與目標
堅持以企業為主體,以市場為導向,注重工廠建設與互聯網平台建設、產業生態建設相結合,充分依託和發揮國家智能製造試點示範和省智能製造示範車間的創建優勢,聚焦「設施互聯、
系統互通、數據互享、產業互融」建設內容,培育創建一批示範引領作用強、綜合效益顯著,覆蓋生產全流程、管理全方位、產品全生命周期的智能製造示範工廠,引導和帶動全省智能製造水平穩步提升。
到2020年,以機械、汽車、電子、醫藥、紡織、輕工等領域為重點,創建50家左右省級智能製造示範工廠,培育100家左右智能製造領軍企業,形成一批智能製造標準。
二、工廠建設總體原則與要求
江蘇省智能製造示範工廠總體上分為離散型智能工廠和流程型智能工廠兩類,每類智能工廠創建遵循相應示範體系要求(具體內容附後),總體上各類智能工廠遵循以下共同原則與要求:
1、設施高度互聯。建立各級標識解析節點和公共遞歸解析節點,促進信息資源集成共享;建立工業互聯網工廠內網,採用工業乙太網、工業無源光網路PON、工業無線、IPv6等技術,實現生產裝備、感測器、控制系統與管理系統的互聯;利用IPv6、工業物聯網等技術實現工廠內、外網以及設計、生產、管理、服務各環節的互聯,支持內、外網業務協同。
2、系統高度互通。工廠的總體設計、工藝流程及布局均已建立數字化模型可進行模擬模擬,應用數字化三維設計與工藝技術進行工藝設計、工藝模擬;建立製造執行系統(MES),實現計劃、
調度、質量、設備、生產、能效等管理功能;建立企業資源計劃系統(ERP),實現供應鏈、物流、成本等企業經營管理功能;建立產品數據管理系統(PDM),實現產品設計、工藝數據的管理;建立試驗數據管理系統(TDM),實現產品試驗、測試、在線檢測數據的管理;建立質量信息管理系統(QMS),實現供方質量檢驗、關鍵工序SPC分析、過程質量數據採集、管理與分析等;在此基礎上,製造執行系統(MES)、企業資源計劃(ERP)與數字化三維設計模擬軟體、產品數據管理(PDM)、試驗數據管理(TDM)、質量信息管理(QMS)、供應鏈管理(SCM)、客戶關係管理(CRM)等系統實現互通集成。
3、數據高度互享。建立生產過程數據採集和分析系統(SCADA),實現生產進度、現場操作、質量檢驗、設備狀態、物料傳送等生產現場數據自動上傳,並實現可視化管理。製造執行系統(MES)、企業資源計劃(ERP)與數字化三維設計模擬軟體、產品數據管理(PDM)、供應鏈管理(SCM)、客戶關係管理(CRM)、質量管理系統(QMS)、試驗數據管理系統(TDM)等系統之間的多元異構數據實現互享。建有工業信息安全管理制度和技術防護體系,具備網路防護、應急響應等信息安全保障能力。建有功能安全保護系統,採用全生命周期方法有效避免系統失效。
4、業態高度互融。構建基於雲計算的集成共享服務平台,實現從單純提供產品向同時提供產品和服務轉變,從大規模生產向
個性化定製生產轉變,促進位造業與服務業相融合。
三、創建重點任務
(一)科學篩選項目。分業分類制定智能工廠示範體系,調研建立智能製造示範工廠創建項目庫,同時對省內智能製造領軍服務企業進行調研摸底,建立領軍服務企業基礎資料庫。按年度動態明確智能製造示範工廠項目申報條件和要求,在申報基礎上組織委內相關處室和行業專家遴選優質項目。
(二)加強過程管理。組織專家對入庫項目進行診斷,形成目標明確、操作可行的診斷報告,企業根據診斷報告意見完善項目實施方案,形成智能製造示範工廠創建任務書。建立創建目標考核責任制,加強實施過程監管,確保時間進度和創建成效。
(三)加強工作協同。建立統籌協同的工作機制,強化信息基礎設施建設,推進工業互聯網發展,加快發展智能裝備和工業軟體,培育壯大系統解決方案供應商。
(四)優化服務保障。組織開展專題現場對接推進活動,促進智能裝備製造商、系統集成商與創建企業對接。加強產融合作,促進金融機構為智能製造示範工廠建設提供資金支持。加強協調服務,確保財政專項資金對智能製造示範工廠建設的有效支持。加強經驗總結,及時宣傳推廣智能工廠創建經驗,引導帶動相關行業企業加快發展智能製造。
附件1:
江蘇省離散型智能工廠示範要點(試行)
一、研發設計環節
應用數字化三維設計與工藝設計軟體進行產品、工藝設計與模擬,並通過虛擬樣機、數字化虛擬工廠以及物理檢測、試驗等方式進行驗證與優化;建立產品數據管理系統(PDM),實現產品多配置管理、研發項目管理,產品設計、工藝數據的集成管理。對產品生產過程建立虛擬模型,模擬並優化生產流程。對各環節製造數據、績效數據集成分析,優化生產工藝,提高產品質量,降低生產成本。
二、生產製造環節
建立製造執行系統(MES),實現生產計劃管理、生產過程式控制制、產品質量管理、車間庫存管理、項目看板管理智能化,提高企業製造執行能力。
(一)生產排程柔性化。建立高級計劃與排產系統(APS),通過集中排程、可視化調度及時準確掌握原料、設備、人員、模具等生產信息,應用多種演算法提高生產排程效率,實現柔性生產,全面適應多品種、小批量的訂單需求。
(二)生產作業數字化。生產任務基於生產計劃自動生產,
並傳送至製造執行系統(MES)生產採集終端,系統自動接收生產工單;通過製造執行系統(MES)生產採集終端可查詢圖紙、工藝標準等技術文件及物料清單(BOM)信息。
(三)過程質量可追溯。建立數據採集與監視控制系統(SCADA),通過條形碼、二維碼或無線射頻識別(RFID)卡等識別技術,可查看每個產品生產過程的訂單信息、報工信息、批次號、工作中心、設備信息、人員信息,實現生產工序數據跟蹤,產品檔案可按批次進行生產過程和使用物料的追溯;自動採集質量檢測設備參數,產品質量實現在線自動檢測、報警和診斷分析,提升質量檢驗效率與準確率;生產過程的質量數據實時更新,統計過程式控制制(SPC)自動生成,實現質量全程追溯。
(四)生產設備自管理。設備台賬、點檢、保養、維修等管理實現數字化;通過感測器採集設備的相關工藝參數,自動在線監測設備工作狀態,實現在線數據處理和分析判斷,及時進行設備故障自動報警和預診斷,部分設備可自動調試修復;設備綜合效率(OEE)自動生成。
(五)生產管理透明化。可視化系統實時呈現包含生產狀況(生產數、生產效率、訂單總數、完成率)、品質狀況(生產數中的不良數、不良率)、設備狀況等生產數據;生產加工進度通過各種報表、圖表形式展示,直觀有效地反映生產狀況及品質狀況。
(六)物流配送智能化。基於條形碼、二維碼、無線射頻識
別(RFID)等識別技術實現自動出入庫管理,實現倉儲配送與生產計劃、製造執行以及企業資源管理等業務的集成;能夠基於生產線實際生產情況拉動物料配送,根據客戶和產品需求調整目標庫存水平。
(七)能源資源利用集約化。建立能源綜合管理監測系統,主要耗能設備實現實時監測與控制;建立產耗預測模型,水、電、氣(汽)、煤、油以及物料等消耗實現實時監控、自動分析,實現能源資源的優化調度、平衡預測和有效管理。
三、經營管理環節
建立企業資源計劃(ERP),以系統化思維和供應鏈管理為核心,科學配置資源,優化運行模式,改善業務流程,提高決策效率。利用跨供應鏈的產品全生命周期管理系統(PLM),改善產品研發速度和敏捷性,增強交付客戶化、為客戶量身定做的能力。高級計劃與排產系統(APS)應用拓展到企業上下游供應鏈,圍繞核心企業的網鏈關係,在正向需求流及逆向供應流之間增加供需平衡管控機制,實現供應鏈各環節共同規劃需求、訂單和預測分析評估調整、產能和關鍵物料規劃與控制、多工廠多車間協同、短中長期物料供需平衡管控等。
四、運維服務環節(針對部分企業)
採用遠程運維服務模式的智能裝備/產品應配置開放的數據介面,具備數據採集、通信和遠程控制等功能,利用工業互聯網
採集並上傳設備狀態、作業操作、環境情況等數據,並根據遠程指令靈活調整設備運行參數。建立智能裝備/產品遠程運維服務平台,能夠對裝備/產品上傳數據進行有效篩選、梳理、存儲與管理,並通過數據挖掘、分析,向用戶提供日常運行維護、在線檢測、預測性維護、故障預警、診斷與修復、運行優化、遠程升級等服務。智能裝備/產品遠程運維服務平台應與設備製造商的產品全生命周期管理系統(PLM)、客戶關係管理系統(CRM)、產品研發管理系統實現信息共享。智能裝備/產品遠程運維服務平台應建立相應的專家庫和專家諮詢系統,能夠為智能裝備/產品的遠程診斷提供智能決策支持,並向用戶提出運行維護解決方案。
五、其他關鍵要素
(一)工業互聯網。採用工業乙太網、工業無線等技術,實現生產裝備、感測器、控制系統與管理系統等的互聯,實現數據的採集、流轉和處理;利用工業物聯網等技術,實現與工廠內、外網的互聯互通,支持內、外網業務協同。採用各類標識技術自動識別零部件、在制品、工序、產品等對象,在倉儲、生產過程中實現自動信息採集與處理,通過與國家工業互聯網標識解析系統對接,實現對產品全生命周期管理。實現工廠管理軟體之間的橫向互聯,實現數據流動、轉換和互認。在工廠內部建設工業互聯網平台,或利用公眾網路上的工業互聯網平台,實現數據的集成、分析和挖掘,支撐智能化生產、個性化定製、網路化協同、
服務化延伸等應用。
(二)工業雲平台。通過協同雲平台,實現製造資源和需求的有效對接;實現面向需求的創新資源、設計能力的共享、互補和對接;實現面向訂單的生產資源合理調配,以及製造過程各環節和供應鏈的並行組織生產。建有圍繞全生產鏈協同共享的產品溯源體系,實現企業間涵蓋產品生產製造與運維服務等環節的信息溯源服務。
(三)工業大數據平台。建立數據倉庫或數據中台基礎系統,應用微服務組件架構,建立演算法和模型。通過數據治理及數據集成,實現決策分析平台,輸出數據指標,指導設計研發、工藝和製造過程。
(四)人工智慧(針對部分企業)。關鍵製造裝備採用人工智慧技術,通過嵌入計算機視聽覺、生物特徵識別、複雜環境識別、智能語音處理、自然語言理解、智能決策控制以及新型人機交互等技術,實現製造裝備的自感知、自學習、自適應、自控制。應用機器學習、專家系統、深度學習等人工智慧新技術對企業生產數據、財務數據、管理數據、採購數據、銷售數據和消費者行為數據等數據資源進行分析和挖掘,實現對研發設計、生產製造、經營管理、物流銷售、運維服務等環節的智能決策支持。
附件2: 江蘇省流程型智能工廠示範要點(試行)
一、工藝優化環節
應用數字化工藝設計技術進行設計與模擬,並通過數字化虛擬工廠、檢測與實驗等方式進行驗證與優化。建立產品數據管理系統(PDM),實現產品多配置管理、研發項目管理,產品設計、工藝數據的集成管理。對產品生產過程建立虛擬模型,模擬並優化生產流程。對各環節製造數據、績效數據集成分析,優化生產工藝,提高產品質量,降低生產成本。
二、生產製造環節
建立製造執行系統(MES),實現生產計劃管理、生產過程式控制制、產品質量管理、車間庫存管理、項目看板管理智能化,提高企業製造執行能力。
(一)生產排程柔性化。建立高級計劃與排產系統(APS),通過集中排程、可視化調度、工業大數據等及時準確掌握原料、設備、人員等生產信息,應用多種演算法提高生產排程效率,實現柔性生產,全面適應多品種、小批量的訂單需求。
(二)生產作業數字化。生產管理系統和分散式控制系統(DCS)全面集成,自動生成企業所需要的日報表、盤點表、月
質量報表等相關報表。生產流水線上重要工藝參數、設備狀態、料位、喂料量等實行實時監控;圖形站上的生產流程圖所有顯示值均為動態數據,可定時刷新。
(三)過程質量可追溯。生產線安裝大量感測器探測溫度、壓力、熱能、振動和雜訊等,用大數據分析整個生產流程,一旦某個流程偏離標準工藝,及時報警預判。質量管理系統和化驗設備無縫集成,實現在線檢測。企業基於同一個平台系統進行操作,與檢測設備集成,自動形成使用數據,系統自動匯總質量數據信息。統計過程式控制制(SPC)自動生產,實現質量全程追溯。
(四)生產設備自管理。設備台賬、點檢、保養、維修等管理實現數字化;通過感測器採集設備的相關工藝參數,自動在線監測設備工作狀態,實現在線數據處理和分析判斷,及時進行設備故障自動報警和預診斷,部分設備可自動調試修復;設備綜合效率(OEE)自動生成。
(五)生產管理透明化。可視化系統實時呈現包含生產狀況(生產數、生產效率、訂單總數、完成率)、品質狀況(生產數中的不良數、不良率)、設備狀況等生產數據;生產加工進度通過各種報表、圖表形式展示,直觀有效地反映生產狀況及品質狀況。
(六)能源系統和水電儀錶無縫整合。準確掌握各類能源介質分系統運行狀況;完善能源計量體系,提供數據支撐、統一數據來源。
(七)物流配送智能化。基於條形碼、二維碼、無線射頻識別(RFID)等識別技術實現自動出入庫管理;實現倉儲配送與生產計劃、製造執行以及企業資源管理等業務的集成。能夠基於生產線實際生產情況拉動物料配送,基於客戶和產品需求調整目標庫存水平。
三、經營管理環節
建立企業資源計劃(ERP),以系統化思維和供應鏈管理為核心,科學配置資源,優化運行模式,改善業務流程,提供決策效率。利用跨供應鏈的產品全生命周期管理系統(PLM),改善產品研發速度和敏捷性,增強交付客戶化、為客戶量身定做的能力。高級計劃與排產系統(APS)應用拓展到企業上下游供應鏈,圍繞核心企業的網鏈關係,在正向需求流及逆向供應流之間增加供需平衡管控機制,實現供應鏈各環節共同規劃需求、訂單和預測分析評估調整、產能和關鍵物料規劃與控制、多工廠多車間協同、短中長期物料供需平衡管控等。
四、其他關鍵要素
(一)工業互聯網。採用工業乙太網、工業無線等技術,實現生產裝備、感測器、控制系統與管理系統等的互聯,實現數據的採集、流轉和處理;利用工業物聯網等技術,實現與工廠內、外網的互聯互通,支持內、外網業務協同。採用各類標識技術自動識別原材料、在制品、工序、產品等對象,在倉儲、生產過程
中實現自動信息採集與處理,通過與國家工業互聯網標識解析系統對接,實現對產品全生命周期管理。實現工廠管理軟體之間的橫向互聯,實現數據流動、轉換和互認。在工廠內部建設工業互聯網平台,或利用公眾網路上的工業互聯網平台,實現數據的集成、分析和挖掘,支撐智能化生產、個性化定製、網路化協同、服務化延伸等應用。
(二)工業雲平台。通過協同雲平台,實現製造資源和需求的有效對接;實現面向需求的創新資源、設計能力的共享、互補和對接;實現面向訂單的生產資源合理調配,以及製造過程各環節和供應鏈的並行組織生產。建有圍繞全生產鏈協同共享的產品溯源體系,實現企業間涵蓋產品生產製造與運維服務等環節的信息溯源服務。
(三)工業大數據平台。建立數據倉庫或數據中台基礎系統,應用微服務組件架構,建立演算法和模型。通過數據治理及數據集成,實現決策分析平台,輸出數據指標,指導設計研發、工藝和製造過程。
(四)人工智慧(針對部分企業)。關鍵製造裝備採用人工智慧技術,通過嵌入計算機視聽覺、生物特徵識別、複雜環境識別、智能語音處理、自然語言理解、智能決策控制以及新型人機交互等技術,實現製造裝備的自感知、自學習、自適應、自控制。應用機器學習、專家系統、深度學習等人工智慧新技術對企業生產
數據、財務數據、管理數據、採購數據、銷售數據和消費者行為數據等數據資源進行分析和挖掘,實現對研發設計、生產製造、經營管理、物流銷售、運維服務等環節的智能決策支持。

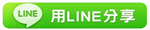
TAG:財政資金申請 |