當汽車製造成為一道門檻,什麼才是最重要的部分?
攝像頭、顯示屏、內存晶元、電池……每部 iPhone 有超過來自 200 多個供應商的零部件,蘋果向全球供應商訂購這些零部件。當這些零件都匯聚到總裝工廠,iPhone 大約需要經過 400 個工序,包括拋光、粘接、切割等等以及一系統測試才可完成組裝。
蘋果的代工廠富士康在鄭州僱傭多達 35 萬名工人,共有 94 條生產線,這大約每分鐘可以組裝 350 部蘋果手機,每天的產量達到 50 萬部。
在如此巨大的產量下,保證 iPhone 體驗基礎的甚至是展現硬體產品高質量的不是富士康,而是這些工序當中伴隨著的蘋果及其嚴苛的質量控制規則,同時,通過強有力的產業鏈控制能力,對生產的各個環節都進行嚴密的監控和檢查,保證消費者最終享受到最好的硬體體驗和質量。
一款好的產品會伴隨著嚴苛的質量把控,而擁有上萬個零部件的汽車對此要求更高。甚至在這個經歷了百年變動的汽車行業已經將質量控制量化到每一秒、每一微米甚至是每一階段例行的破壞性檢測。
19 世紀之前,汽車生產工人是採用手工的方式,將各個零部件組裝成汽車。在那個年代,汽車的品質把控是由檢查人員依靠「看」和「手動」來檢查製品的好壞。但是這個方法除了會受到檢驗工具的影響,還會受到檢查人員的情緒的主觀影響,批量產品質量波動很大。
科技不斷發展和市場競爭趨於激烈之後,質量波動大的產品逐漸變得不能適應競爭。因此,現在的汽車除了採用新的生產技術外,正是採用了不斷更新的全新的品質控制方式。
直到今天,汽車品質控制方式也已經順應浪潮開始朝著智能化方向演進。當新造車、新思維、新革命不斷的涌動汽車行業發生變化的時候,汽車製造成為了這之間的一道門檻,而這道門檻的背後對於量產質量的不懈追求正是傳統車企付出了無數心血的地方。
知乎上有這麼一個問題「現階段中國哪家汽車製造企業的「生產工藝」與「質量控制」最好?」其中一個回答的總結是,「總體而言,國內工藝「最好的」企業,基本就是最晚投產的「豪華品牌」。因為只有豪華品牌才能承擔好工藝帶來的高成本,而越晚投產的廠房,通常技術越先進、自動化信息化程度越高、工藝流程越成熟。」
而奇瑞捷豹路虎常熟工廠正是這樣一個「成熟」的相對「晚」投產的「豪華品牌」生產基地。2014 年投產的奇瑞捷豹路虎常熟工廠,不僅是捷豹路虎首個英國本土以外的整車製造工廠,是全球樣板工廠,它還投產了國內首家專制全鋁車身車間。
在這一個自動化信息化程度相對高、技術先進的奇瑞捷豹路虎常熟工廠,在它的身上我們才能看到「質量控制」對於他們的意義是什麼,以及「質量控制」如何成為汽車製造環節中的最重要的必修課,甚至它未來該如何「進化」。
「濃度高」的質量檢測
340 個全鋁車身車間機器人,短短几分鐘之內打造了捷豹 XFL 全車共 2754 個鉚點。在自動化、速度與效率之外,質量檢測成為了奇瑞捷豹路虎整間工廠中最「冷靜」的一個環節。
不驚嘆於效率,而是將 2754 個鉚點一一進行檢查,同時,質量檢測也不只是「事後諸葛亮」。在鉚接過程中,運用「自沖鉚接實時監測系統」進行在線監控;可視化塗膠監測系統確保黏合劑的位置精準;同時,運用激光定位設備和攝像技術,工藝精確到 0.2 毫米,確保工藝質量等等,這是也許就是他們不斷積累出的「心血」經驗。
這樣的質量檢測幾乎遍布生產的每一個環節,而更重要的是他們彼此組成一個個可反饋的循環。在總裝車間的車輛下線點,在進行 Calipri 間隙段差檢測時,它是與焊裝車間共享後台數據,保證了第一時間將產品缺陷信息反饋給焊裝車間,可以幾乎同時進行與車身相關的焊裝改進。而這也被奇瑞捷豹路虎稱為過程質量控制系統(Premium Process Control System)的一部分。
質量體系看似是一個簡單的流程檢查,但其實卻因為汽車行業的百年沉澱演化成了一個與製造體系密不可分的重要流程。
現在很多工廠都已經做到了過程中儘可能的「生產可追溯」,也就是質量信息採集和質量追溯。簡單說就是當車有質量問題了,檢查發現是螺栓沒有緊固好,以前查不到任何信息,現在,當廠商的生產線信息化做得足夠「精緻」,螺栓緊固信息全部記錄在案,一查就知道。
為此,奇瑞捷豹路虎也擁有一款質量大數據平台系統 IQIS。
奇瑞捷豹路虎將這套系統連接所有和質量相關的系統,比如售後 IQM(解決售後質量問題的捷豹路虎全球系統)、MES、SAP、車聯網平台等系統,在此基礎上管理公司的質量表現、質量分析、質量檔案管理等,並通過大數據模型中與質量相關的數據產生聯動,從而及時發現問題,甚至是提前質量預警等等。
於是與這些質量系統配合的精度高達 0.5μm,不足頭髮絲直徑的百分之一的三坐標系統、振動台、環境倉,以及業界領先的氣密性測試標準設備等等就成為了奇瑞捷豹路虎常熟工廠的一部分優勢所在。
全鋁車身的秘密
製造體系其實是企業硬實力和軟實力的最佳體現。
而這個 2016 年 4 月竣工投產的國內首家專制全鋁車身車間,則讓奇瑞捷豹路虎常熟工廠變得與眾不同。佔地面積 48420 平方米的奇瑞捷豹路虎全鋁車身車間,擁有全球先進的鉚接膠合技術和設備,鉚接自動化率已經達到了 100%。
質量不僅是檢查出來的,源頭的設計對質量的影響也同樣重要。全鋁技術則凸顯了捷豹的設計優勢,鋁材料輕巧,堅固……等優勢讓捷豹開發的車型具有輕量化,快速響應的特點甚至是讓車身設計達到接近 50:50 的前後車身比重分布,讓整車具有更強的操控性和性能表現。同時,這些節省下來的重量,更可以為未來越來越多的複雜科技的布置安裝做準備。
你在工廠內還能看到更多的新鮮科技,例如虛擬工廠模式,通過工藝流程及布局模型、生產過程模型和組織模型等系統建模,以及模擬分析,實現工藝優化,並基於供應鏈大數據平台建設物聯網系統。不斷的讓全鋁製造變成一個不斷進化的工藝。
所以在全鋁車身等一系列標準和設計要求上,奇瑞捷豹路虎採用了和總部全球統一的設計要求、規範與工程驗證來確保產品質量一致。整車量產前,從設計優化、零件匹配,到系統調校,都要經過非常嚴苛的驗證。
你很難想像製造一輛全新的捷豹 XFL,從單個零件到整車系統,它歷經了 89516 工作日的完整驗證和試驗。還有模擬極端使用情況下 30 萬公里多通道台架測試,並在英國米拉試車場進行了 7x24 小時不間斷的 70000 公里耐久測試。
「質量控制」這方面主要是看整體的質量管理體系,汽車底蘊深厚的企業在這方面擁有很強的優勢。
這也是為什麼許多自主品牌選用和合資豪華品牌相同的供應商,但在細節的質量上仍然要略遜一籌。因為缺乏完整的質量管理體系,無法對供應商提出精準的要求,所以也就在相同材質的情況下,質量會出現差異。
影響質量的因素很多、涉及面也很廣。那麼作為企業「細胞」的班組如何做好基礎質量管理工作就顯得尤為關鍵,每一道工藝、每一個材質都在考驗著傳統車企以及這些新入局的新造車勢力們的「耐心」。我們已經看到門檻的背後對於質量的不懈追求正是傳統車企付出了無數心血的地方,因為要能夠有過關的硬體基礎和體驗這才能為下一步打造一個完美的前提。

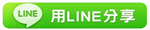
※從智能手環、智能手錶再到 AI 晶元,華米看到的究竟是什麼機會?
※馬蜂窩被爆出數據造假;因恆大違約:FF 全員降薪 20%;Oculus 聯合創始人宣布從 Facebook 辭職 | 極客早知道
TAG:極客公園 |