整體和細節看華為供應鏈到底怎麼樣?
有人在「知乎」上邀請我評價華為的供應鏈管理水平如何,我結合自己前後跟華為打交道幾年的經驗體會,於是成就此文供大家參考、批評指正。
2000年左右,我剛進入IBM做北京工廠高級物料經理的時候,華為就已經開始花大筆的諮詢費請IBM實施ISC(集成供應鏈)及IPD(集成產品研發管理)了,這在當時是非常有轟動效應的,在諮詢領域,尤其是導入國外供應鏈管理方面的諮詢,華為應該是最早吃螃蟹的這一批企業。應該說,在供應鏈管理方面,任總的眼光絕對是超前的,至少比一般人超前10年多。
2007年我在偉創力擔任手機事業部供應鏈管理總監,為他們代工手機(華為終端業務),儘管他們跟我們做的只是consignment(來料加工),但明顯感覺他們的供應鏈管理還是比較混亂,生產計劃朝令夕改、物料不齊套等情況一直比較嚴重,但那個時候聽說他們的operator(運營商業務)方面供應鏈管理還是可以的。
2011年,我在AC公司負責電子高科技行業供應鏈管理諮詢,又有幸接觸華為,跟他們合作供應鏈管理方面的諮詢項目,前後大約一年半左右的時間,接觸了很多華為供應鏈管理方面的人。總體感覺是,10多年過去了,他們還是在花大力氣放在供應鏈管理領域的諮詢上。
由於沒有直接在華為工作過,所以,我很難詳細地說明華為的供應鏈管理到底怎麼樣,但整體感覺是,華為的供應鏈管理在行業中肯定算是佼佼者了,否則其業務也不可能這麼快速地增長,相信供應鏈管理在這個過程里功不可沒,畢竟,供應鏈管理諮詢的巨大投入,至少在客觀上是起了一定的作用的;但從微觀層面,通過我親自接觸過的人和事,我感覺他們的供應鏈管理應該比現在更好一些才對,當然這僅僅是感覺。
由於華為不是上市公司,我只是百度到他們2011-2013年度的財務報告,單從庫存周轉率角度,他們這幾年是有很大的提高,2011年為4.8次,2012年為6次,2103年為5.7次,比十幾年前,華為在實施ISC之前的3.6次(見下面附錄信息),是有大幅度的提高,提高比例在60%以上,這在供應鏈管理上,已經是非常了不起的了。
同時,我又比較了華為的競爭對手,愛立信電信,他們的水平一直徘徊在4次左右(見新浪財經上市公司財務報告2013-2014),相比較而言,華為的庫存周轉率水平已經遠遠超過了其競爭對手愛立信。
當然,這裡面有個因素需要注意的,那就是華為終端(手機)業務比例的上升,客觀上提升了其整體庫存周轉率。這塊業務佔總銷售收入的24%左右,但其實扣除這個因素,華為的庫存周轉率應該也是比愛立信要高一些,至少是持平,但因為沒有分開的財務數據,我們無法確定。
只是,令人奇怪的是,按照附錄信息,當初IBM幫華為整合供應鏈之前,他們說(當時,十幾年前)國際上其他電信設備製造商的庫存周轉率是在9.4次左右,這個數據是怎麼來的,我們就不得而知了。如果這個數字是準確的(我個人表示懷疑),那麼,世界兩大電信巨頭在這方面還有很長的一段路要走。
至於附錄信息提到的訂單及時交貨率,這個就更無從查起了,至少財務的3張表是沒有這方面的數據的。
以上分析至少局限於我個人前前後後跟華為打交道的一些感覺、體會,即使數據,包括計算的庫存周轉率等,也是非華為官方數據,儘管原始數據應該是真實的。
總之,華為是一家令人尊重的公司,尤其是任總在管理方面,不僅僅是在供應鏈管理方面,其開放的心態、超前的戰略眼光及腳踏實地的管理作風,是絕對值得我們絕大多數業界人士認真學習的。
附錄信息:據IBM顧問介紹,華為在重整供應鏈之前,其管理水平與業內其他公司相比存在較大的差距。華為的訂單及時交貨率只有50%,而國際上其他電信設備製造商的平均水平為94%;華為的庫存周轉率只有3.6次/年,而國際平均水平為9.4次/年;華為的訂單履行周期長達20~25天,國際電信設備製造商平均水平為10天左右。重整供應鏈的目的就是為了設計和建立以客戶為中心、成本最低的集成供應鏈,為華為早日成為世界級企業打下良好的基礎。
華為這樣管理庫存
不合理的庫存導致公司破產的例子比比皆是,相比產品本身開發的失敗,庫存造成的損失往往更大。華為在很早的時候就意識到,庫存的大幅波動會給企業帶來資源浪費、成本增加、資金緊張等一系列的問題。因此,通過變革以及不斷地思考和改進,華為在庫存管理方面有了一些獨到之處,本文將用七張圖為您直觀展現。
庫存是把雙刃劍,一方面能提高供應柔性,但另一方面會佔用大量資金。不合理的庫存水平將有可能造成企業的資金鏈斷裂。相比產品本身開發的失敗,庫存造成的損失往往更大。
在華為,庫存管理的特點主要在於庫存規劃和日常管理方法。在規劃方面,華為有一套成熟的訂單履行流程,並且通過與業內標杆比對不斷進行改進,往往在年初時就需要定好全年的指標。而在庫存的日常管理方法方面,主要有以下幾點值得其他企業借鑒採納:
華為在建立自己的庫存結構時,採用了「棗形」結構。這對於大多數按訂單生產的企業來說,也是一個比較合理的庫存模型:成品及原材料相對比重較小,在制品比重較大。
在華為,主要採用ABC分類法對物料進行管理。ABC管理法是根據事物的經濟、技術等方面的主要特徵,運用數理統計的方法,進行統計、排列和分析,抓住主要矛盾,分清重點與一般,從而有區別地採取管理方式的一種定量管理方法。又稱巴雷托分析法、分類管理法等。
根據通用性強弱、價值高低等差異,華為對不同的物料採取了不同的採購、計劃與庫存控制策略。對戰略性物料需要做適當的長單或儲備,根據一定的方法(如根據其歷史用量和未來6個月需求量,ABC分類法等)對各種物料設定安全庫存。
齊套性是指完成某個半成品或成品的生產時,其構成的所有物料全部到位,能夠進行全部工序的生產。物料的齊套性很重要。物料不齊套將造成生產停線待工,浪費機台和人力及管理成本,影響生產進度。因此,華為通過提高計劃的準確性及計劃的執行力度,加強齊套性管理。
在華為,齊套性管理主要從兩個方法入手:(1)預缺料管理;(2) 風險預警及升級機制。
此外,華為還十分注意控制物料到貨的進度與節奏,維持進出平衡。控制物料的到貨主要是加大對例外信息的處理力度,控制不合理到料。具體方法可以採取如:把例外信息處理的比例列入採購的考核指標(按金額),每周公布統計排名;或者考慮把這個標準列入供應商考核的指標等。
華為對於低周轉物料的處理辦法是,第一,定期處理,分責任人,提交處理報告。第二,低周轉物料產生時,要把責任、原因分析清楚。第三,該報廢的報廢,該變賣的變賣,決不手軟。並且,低呆物料在不同情況下對它的周期有一些規定,像電容類、耐用品等的周期是不一樣的,不是一刀切的。
除了上述幾點,還有一些其他措施,比如:計劃提前介入研發IPD進度,嚴格把關物料的可計劃性、物料歸一化管理、物料的多家供應等評審;推行分級備料的方式,讓整個供應鏈條一起承擔庫存風險,也能提高供應柔性;建立計劃/採購/核心供應商的定期溝通機制,提高信息透明化...
總之,華為在庫存管理方面有不少方法,除了需要不斷改進和優化,也需要和供應鏈其他環節如計劃、採購相互配合,力爭消除庫存負面積壓、周轉率低等所造成消極影響。
文章選自庫存專家 程曉華老師,與華為專業研究社 華營私塾。
熱門推薦(點擊標題閱讀):
2、英國缺EE人,缺到你想像不到!
識別二維碼,一鍵關注
深度報道電子產業供應鏈
分享最及時前沿商情解讀

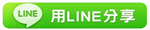
※美國車市寒冬:通用全球七家工廠將停產,福特將裁員7萬人……
※超詳細的液晶面板行業產業鏈!
TAG:國際電子商情 |