西飛精益工廠建設綜述:把精益做到職工心坎里
如果你想了解2018年航空工業西飛的熱詞是什麼?毫無疑問,那就是「精益」。
精益,並不是一個新鮮的辭彙, 但它也並不是靈丹妙藥,吃上一顆企業就會立即煥發青春,它必然伴隨著組織機構的重組、人員素質的提升和運營管理體系的優化,這些必然環環相扣,缺一不可。而從2014年開始的AOS試點,2016年生產單位扁平化改革、2017年職能部門一體化改革至2018年生產單元精益化改革,無論是從符合國家戰略和客戶需求,還是立足於企業未來的發展趨勢上,都為精益在西飛的落地生根鋪平了道路,奠定了基礎。
「生產單位扁平化」改革,原有的三級管理體系變革為「公司—專業廠」兩級管理體系,56個廠被整合成20個專業化工廠;通過實施「職能部門一體化」,部門組織實現由條塊職能型向流程功能型模式轉變;2018年啟動的「生產單元精益化」改革,標誌著西飛開始發力打通精益工廠建設的「最後一公里」,為準時化生產、均衡化交付奠定組織基礎。
2018年,按照「整體規劃、分步實施、陪伴式指導、達標式考評」的工作思路,採取先試點推行、後推廣應用、再全面實施的具體步驟,公司大力推進精益單元建設工作。先選取典型單位開展試點工作,探索精益單元運行機制及人力資源管控模式,在總結試點單位成功經驗的基礎上,向各專業廠複製推廣,將各類資源向生產一線傾斜、聚集,構建績效卓越的精益生產體系,提升企業價值創造能力,全面形成員工積极參与精益工廠建設的機制、氛圍,再通過強制性貫標、符合性評價、績效指標的嚴格考核, 實現精益工廠建設全面落地。
這是一場提升企業能力的自我修鍊,西飛在這場修鍊中不斷提升自己的硬實力和軟實力。生產效率提高了, 等待時間減少了,勞動強度降低了, 生產操作者更專註於生產執行以及作業過程的標準規範,隨著效率和質量的持續改善,職工收入穩步提高,這一年,西飛切實收穫了精益帶來的「紅利」。
精益之路越走越堅定
2018年3月13日召開的深化精益工廠建設暨生產單元精益化改革啟動會,正式開啟了西飛生產單元精益化改革。繼生產單位扁平化、職能部門一體化改革後,西飛的生產單元精益化改革隨之拉開帷幕。3月22日晚, 公司召開試點階段精益單元實施方案及工作計劃評審會。會上,機身裝配廠、機翼裝配廠、數控加工廠、結構件廠、蒙皮成形廠、鈑金構件廠等6家試點專業廠從產品家族劃分未來單元價值流圖、人員配置構成、單元管控制度和績效指標評價等方面介紹了各自精益單元建設的方案及具體實施計劃。同時,為了更好地推進精益單元建設試點工作,西飛成立業務指導組和組織保障組,全力做好「陪伴式」服務,各相關職能部門為精益單元建設一路「綠燈」,全力保障,「陪伴式」服務也讓精益單元建設有了組織保障和技術保障。
西飛領導班子提出,一定要學會用工具治理企業,沿著AOS方向路徑,以鋼鐵般的意志堅定不移地走下去,最終實現企業的卓越績效目標。
精益工廠建設之初,西飛就在發展規劃、運營管理體系架構、人力資源管理、員工培訓教育和發展、質量管理、工藝技術管理、生產計劃管理等方面在各專業廠全方位地開展精益化推進工作。公司系統策划了精益推進的路徑以及考評的辦法,由簡單的工具方法研究與應用向系統策劃與體系推進轉變;通過公司運營管理體系的正式運行,實施一體化的流程管理, 並依託精益單元建設逐步落地見效; 有針對性地編製了單元級、專業廠級、公司級的三級評價標準,以此推動和促進各職能部門的服務與支持。
通過試點,西飛總結出裝配類、零件類精益單元構建的技術路徑、運行模式、組織機構與崗位設置方案, 形成了一套單元管控及人員考核辦法。裝配類單元建設技術路徑是依據生產節拍,通過價值流分析,識別瓶頸站位,尋找關鍵路徑,優化工藝流程, 進行生產線平衡、工作站拆分,重新進行資源調整;細化三級生產作業計劃,明確單元物料需求、配送方式和物流路線,在關鍵路徑上設置預警管控機制。零件類單元建設技術路徑則是依據裝配需求拉動零件生產,結合分族分類結果,選取典型產品家族, 進行工藝精益化和工藝標準化設計, 定產品、定設備、定人員,有針對性地開展一人多機,培養多能工;建立各專業工藝技術知識庫,實現關鍵操作標準化。
試點單元充分發揮示範引領作用,形成一套精益單元建設的管理流程和方法,生產現場可視化管理效果明顯。2018下半年,公司精益工廠建設全面發力,在全公司各專業廠進行複製推廣試點單元的成功經驗。
2018年7月29日上午,一場別開生面的現場觀摩指導會在工具管理中心的生產現場舉行。與會人員驚訝地發現,現場管理基礎薄弱,起點並不高的工具管理中心在精益工廠建設上走在了前面。在這裡,幹部帶頭, 全員上陣,精益求精,完美地詮釋了精益的價值觀和無限可能性,工具管理中心的「精益魔法」讓它煥發了新活力。隨著生產現場精益改進力度逐步加大,生產現場改進早已從表面的概念性改進轉變為深入式改進。一個個精益櫃、工具車不斷升級,零散的庫房合併後變成了精益的工具「超市」……新點子、好方法在職工的腦中、手中變成了現實,實現效率最高、利益最大化。老廠房換了新容顏,老廠房裡的人也有了新的活力和期待。讓精益成為習慣,讓卓越成為可能;讓規則深入人心,讓體系得到敬畏;讓創新成為常態,讓智慧成為財富,這些理念已悄然植入員工的心中。
「領導幹部帶頭做、帶領員工一起做」「將技術、精益兩者有機融合」。在精益單元建設上,西飛領導幹部有擔當有作為,主動做、帶頭做,帶動職工一起做,讓精益理念深入人心, 全員參與。在做的過程中,西飛又始終把握成本績效導向,不斷降本增效, 牢記AOS22條準則要求,抓住技術的引領作用,缺乏技術支持,精益很快會碰到天花板,精益 技術的有機融合,才能開拓無限可能,才能在成本控制、智能製造等方面取得更大的突破。
數控加工廠就一直狠抓技術的引領作用,採取「標杆引領、整體推進」策略,以肋類零件精益單元為試點,「七個單元」齊步走,共同推進。針對數控瓶頸產能的提升,工藝精益化及標準化工作可算是肋零件單元建設初期關鍵的基礎工作之一。相似零件運用統一的程編軌跡、統一的定位裝夾方案、統一的刀具及參數、統一的防差錯方案、統一的製造指令,這些標準化有效控制了單元零件的加工質量。通過「黑燈設備」「成組化加工」等技術創新項目的開發應用,實現了程序調用、基準找正、刀具切換的全面自動化,甚至連鋁屑的清掃都可以由機器完成。數控設備一鍵啟動,無人值守自動運轉16小時以上,保證了單元內數控設備的連續運轉,部分肋零件的數控效率提升在30%以上。數控加工廠的肋精益單元80%的設備實現「一人多機」,大幅提高設備利用率, 每月增加設備產能千餘小時。
為助推精益單元建設再加力,讓精益單元建設責任人更加深刻理解精益工廠建設推進體系,從2017年開始,公司對各專業廠黨政一把手及精益主管領導、推進人員進行《精益工廠建設評價標準》的宣貫、單元推進路徑及方法培訓;對各專業廠、部門領導、推進人員進行精益理念、方法培訓,《精益單元評價標準》宣貫。組織各專業廠和相關職能部門的一把手進行「精益領導力」專項培訓,讓這些「領頭羊」成為精益單元建設的「最強大腦」,提升管理者引領精益工廠建設的能力。同時,組建公司專家隊伍、評估專家隊伍,進行精益工廠建設現場評估;每周二的晚上,開設在培訓中心的AOS夜校座無虛席,越來越多的精益骨幹從這裡走出去,成為各單位的精益力量。
整潔的生產現場
在總裝廠,數字化脈動生產線自實行「站位化管理」以來,生產效率和產品質量得到進一步提升。2018年, 總裝廠又以精益單元建設為依託,以生產線產能效率提升、人員減少為目標,對脈動生產線的管理模式重新進行大幅優化。在短短一年半時間內, 這條生產線從站位化管理到各站位的重新布局再到如今的精益單元建設, 通過優化生產線人力資源配置、增線不增人、一專多能,2018年這條生產線已實現了均衡交付。在總裝廠,雖然任務依然很重,但無效等待、被動加班少了,工作效率更高了。
一切都是有序而快速,精益改變了原先很多習以為常的生產模式和流程,這是一場翻天覆地的改革。
道,漸行漸明;路,越走越堅定。
玩轉精益「魔法」
「舉一綱而萬目張」,精益如漁網 上的總繩,提起網上的總繩一撒,一個個網眼就全部張開了。「原湯化原食」,生產現場的問題靠精益的辦法來解決。當職工嘗到了精益的甜頭,職工就會自主發力,同時,在制度上有了配套,有了細化,有了保障,職工「讀懂」的不只是要我做精益,更是對未來實現精益工廠的嚮往與憧憬。
無論什麼樣的創新,都必須以創造價值或解決問題為核心才有意義, 精益生產的核心是最大限度減少生產所佔用的資源。企業,只有實實在在地解決生產現場的浪費,才是基於價值創造的、有利於精益工廠建設的創新,才能符合主價值鏈需求。在精益工廠建設的進程中,各專業廠在生產現場改進中各出奇招,目的都是為了消除浪費、創造價值。通過改進現狀、進化自我的實踐,不斷改變和拓展人的思維方法和行為能力,讓員工真正成為企業運營價值鏈上的主人。
在創新管理室精益副主任張秋芬的微信里,有這樣一段話:「一切為了現場,一切來源於現場,一切回歸於現場!每走一次現場,心裡就踏實一次。喜歡和他們交流,他們直率、坦誠、可愛,他們最了解現場問題,我們需要用心傾聽一線人員內心的聲音,耐心啟發他們改變思路,尋求解決方案, 真正為他們解決問題。」在張秋芬的世界裡,精益就是她的工作重心所在, 而她與夥伴們通過努力讓更多的職工感受到精益的魅力,這也讓她更堅信了自己的工作價值。
熱表處理廠零件熱處理單元長李秋野興奮地說:「產量提升了數倍,加班卻少了,若不是精益,完成任務連門兒都沒有!」李秋野的興奮得益於一張「列車時刻表」。一年前,熱處理單元的生產現場,各專業廠送來需要熱處理的零件堆積如山,工人滿臉疲憊,加班已是常態,半夜三更被電話召回單位趕急件也是常有的事。於是,熱表處理廠精益改進團隊針對不同的工藝參數對零件分族分類,通過現場生產數據、排產影響因素、設備故障原因等分析,優化生產組織模式, 從人、機、料、法、環因素進行改善, 分別對每一環節中存在的問題拿出解決措施,合理利用峰谷值排產。通過科學排產,他們將每一種材料、每一台設備開工時間都寫得一清二楚,制定出零件熱處理的最優排產規則,就像一張精準的「列車時刻表」。有了這張表後,零件生產廠按時刻表送達零件,設備的裝爐量提升了,開爐次數減少了,零件準時交付率月平均值由83.40%提升至95%。2018年1~7月用電量同期下降20%,交付周期縮短30%,零件掛急量同期減少70%。今天,還是同樣的地方,零件擺放有序, 計劃排產節點清晰,管控有效。
當公司對機翼裝配廠進行單元成熟度評估驗收時,架外裝配單元長王東自信滿滿、侃侃而談,現場工人更是如數家珍,興奮地展示著自己的改進成果。王東講到工人克服困難自發改進的器具時,竟然感動到一時哽咽, 眼圈都紅了。因為只有親歷者才能知道,精益單元如今不斷提升的績效, 其中經過多少次失敗才有了現在的成果。成功,也許會遲到,但絕對不會缺席。一線員工的高度認可與積极參与,是精益的動力源泉。
2017年,同樣是在機翼裝配廠, 當創新管理室的精益團隊在現場為該廠的職工授課時,廠里有一位工人師傅用不屑的口吻說:「我工作了大半輩子了,我的後腰都不知被型架碰過多少回了,你能用精益解決嗎?」「能! 只要你給我一份信任,我就還你一個驚喜。」張秋芬堅定地回答她。
於是,精益團隊用了一個多月的時間,按工藝流程重新布局工位,對生產線進行調整,規划出物流通道、人員行走通道,改變了生產現場長期不合理的工裝布局。精益帶來的不僅是工作上的轉變,還有精神上的愉悅。如今,工人工作的現場是乾淨整潔的, 以前積壓如山的製品因為精益管理而變得井然有序,清晰的物流標識和管理看板使得各項工作有條不紊,精益單元建設讓在制品積壓顯著下降,產能、准交率持續提升,員工收入不斷增加。
有一次,張秋芬在生產現場又碰到當初質疑她的那位工人時,這位師傅高興地告訴她:「真沒想到,你們真的做到了,雖然我還有兩年就要退休了,但我的徒弟們會繼續得益於精益帶來的好處,真心感謝你們!」當初的不屑和懷疑變為發自內心的笑容, 沒有什麼硬性指令能比一線人員積極主動提出改進方案的推動力更強。對於精益,職工們曾經有過的猶豫和懷疑現在已轉變為堅定不移,發自內心的認可,並積極投入。
水不激不躍,人不激不奮
在西飛,精益的種子已經播散到各個角落。在精益加工中心,所有的精益改進都圍繞生產現場而進行。他們針對大型零件使用通用工裝降低更換工裝的頻率;對小型零件則採取快換工裝來減少機內裝夾,實現自動化加工減少程序間停機;針對鈦合金零件推廣配送人員裝夾;針對封閉式機床採取清潔風扇除屑……一系列的精益改進,大大減少了工人生產準備時間,提高了生產效率。精益加工中心鈦合金工段技術副工長裴高超深有感觸地說:「大量的精益改進都是為了提高產能,而這些改進反映在生產管理上就是改變了工人很多原有的工作習慣。最初我還要勸說、督促工人執行一些看起來『不好』的規定,現在卻少費了很多口舌。」裴高超所說的那些「不好的規定」是什麼呢?比如要求工人進行形跡化改進,比如在部分機床除屑時不再使用風槍、水槍,比如中心嚴格考核計劃完成率,中心測算出的標準操作時間和實做時間不符、互查互校機制的推行等。所有這些精益改進的方法最初都讓工人有點不適應,但最終設備OEE提升了、工人的勞動強度減輕了,精益的成效是最好的證明。
現在,每天當你走進精益加工中心658號廠房時,每台數控機床旁的狀態指示燈綠燈基本都已亮了,配送組的叉車已經在廠房開始了一天的配送工作,整個生產運行體系高效、快捷。而在每天機床預熱的時間內,各生產單元會組織召開一個僅有10分鐘的SQCDP例會。只需要10分鐘就足夠講明白所有問題,因為通過MES製造執行系統已將SQCDP各類信息電子化,安全、質量、成本、進度、人員等各因素的關鍵指標及現場異常問題得到隨時監控和處理,所有數據都是透明公開的。
在國際航空部件廠,精益改進團隊自主學習研究氣壓原理,設計製作氣動一鍵式壓緊裝置,縮短裝配周期, 降低操作者的勞動強度。
在工具管理中心,精益改進團隊通過現場觀察、試驗,並與操作人員交流,結合車床的結構,動手自製了防飛濺裝置,有效保護了操作人員的安全,同時便於集中清掃。
在模具鍛鑄廠,工人在現場堅持班前、班中、班後三個「五分鐘」,1把噴壺、1塊抹布、1個好習慣改變了現場的工作環境,也改變了員工的工作心情。
在蒙皮成形廠,各生產工段全面推進「班前五分鐘、班後十分鐘」的清理整頓「510」行動。「510」寓意為「我要動」,激發了員工自主管理的積極性, 將生產現場管理規範細化到職工的日常行為中。
「推行精益之前,工作是哪癢撓哪,哪疼治哪,踐行精益之後,員工會主動地、有針對性地發現問題解決問題,學會『偷懶』幹活了。」從一點一滴的小事做起,將精益的理念逐漸滲透於日常的生產中,精益為員工帶來的是意想不到的收穫。在採訪中, 從一線員工或微笑或羞澀,或嚴肅或動情的描述中,你能看到他們的眼睛會發光。從抱怨、不理解、不認同到如今的贊同和自主自發地要做精益, 西飛的員工正用最樸素的行動表達出對精益發自內心的堅守。
兄弟齊心,其利斷金
在精益工廠建設中,西飛各專業廠打破界限,廠際間單元協同,互相合作。
跨專業廠精益生產單元合作模式讓蒙皮成形廠和熱表處理廠嘗到了甜頭。蒙皮類產品一直存在加工周期長、外圍工序多、周轉過程複雜等不利因素,為縮短交付周期及產品周轉距離、減少蒙皮運轉中可能產生的質量問題,蒙皮成形廠提出「蒙皮產品表處後直交」方案,即將產品表處後直接在熱表處理廠現場交檢,然後直接運送交付到裝配現場。方案得到了熱表處理廠、國際航空部件廠、製造工程部、質量管理部等單位的大力支持,在規劃經營部的指導下,蒙皮成形廠和熱表處理廠開展了跨單位間的精益生產單元合作模式。他們在流程梳理、資源配備、問題快速響應、模擬運行等方面開展了一系列細緻的計劃後,蒙皮成形廠選取波音項目作為「蒙皮產品表處後直交」試運行產品, 在熱表處理廠304廠房現場進行產品直交模擬運行,在各部門積極配合和努力協同下,2項7件大蒙皮在304廠房順利完成交檢、制標識等工序, 以100%的合格率將蒙皮產品從熱表處理廠現場直接交付到國際航空部件廠,將交付周期從1~2天壓縮到1~2個小時。縮短產品周轉距離,既減少了現場佔用面積,也大大減少了蒙皮搬抬及運輸過程中可能產生的表面質量問題,降低生產成本,提高生產效率, 實現了精益生產理念在生產單元的精準落地。
在某型機生產線,機身裝配廠和工具管理中心開展了工具站位式可視化配送管理。機身裝配廠精益單元建設團隊在前期工具形跡化定置管理的基礎上,在工具櫃側面設置工具配送管理可視板,按工具現狀分為「可 用」「故障」「不可用」三種狀態,分別對應綠色、黃色、紅色三種顏色標識,操作人員根據工具使用狀態,標註相應的標識,提出配送需求。工具管理中心配送人員每天早上8點半之前,檢查各站位所有的工具櫃配送管理可視板標識,若有「故障」或「不可用」標識情況,針對需定檢、保養、返修的工具,及時補充工具完成更換, 並使用工具臨時借用帳與站位負責人辦理交接手續,保證工具櫃始終處於可用狀態,問題狀態不跨日,並根據工具安全庫存情況及時補充工具。這種工具站位式可視化配送管理受到操作人員的歡迎,因為它消除了工人自行借用、送修、保養、定檢工具的時間, 在提高工具使用效率的同時,增加了有效工作時間,提升了生產效率。
精益,再一次用它的魔力散發出它獨有的魅力。
當前,我國各項改革發展事業進入新時代,航空工業未來發展藍圖也已繪就,正是所有航空人施展作為的大好時機。肩負著今日和未來,西飛的各個角落都迸發出精益的力量,精益的步伐必將越走越快,越走越穩。在未來精益工廠建設的道路上,西飛有能力書寫更精彩的故事,建設更美的精益工廠。

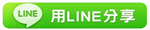
※美國C-5M「超級銀河」為B-1B維護提供零件
※霍尼韋爾、賽峰推進混合電推進系統研製
TAG:看航空 |