蜂巢能源張放南:動力電池系統安全設計構想
新能源汽車補貼政策從2016年開始退坡,同時提出動力電池高能量密度路線。近期接二連三的電動車自燃事件,引發了大眾對於電動車安全的進一步關注。7月5日,由蓋世汽車主辦的2019新能源動力電池安全技術論壇在上海舉行,蜂巢能源科技有限公司Pack開發中心總監張放南就動力電池系統安全設計進行了主題演講,內容如下:
張放南:我給大家分享的主題是《蜂巢能源動力電池系統安全的構想》。
總共分為5部分的內容,第一項是安全問題的簡介,王總也講了,現在的消費者從「里程焦慮」逐漸轉到「安全焦慮」,我們也把安全事故做了一個初步劃分,業內對安全的劃分有很多種,分法不太一樣,整體是差不多的,包括失效的原因也做了一個初步分析,包括起火爆炸、高壓觸電、化學安全。失效原因也做了三個劃分,一個是控制策略的原因,一個是外部短路的原因,還有內部的原因。控制策略失效包括過充、過放、過溫,以及絕緣失效,外部短路原因包括過放或者線路老化引起的外部短路的機械的損傷,內部短路主要是在製造過程中的缺陷以及後期使用過程中的絕緣膜的溶穿。
針對系統安全我們做了一個初步的劃分,從電池的整個生命歷程分了三個階段。第一階段是電池生產和設計過程中注意安全,然後是電池應用中的安全,以及梯次回收安全,做了三個大的領域劃分。
針對產品設計過程中也分了四個層級。第一級主要是針對原材料,電芯,整車,整個系統過程中實現多重的主被動設計,通過控制策略的優化來實現安全的控制,就是依託自動化的生產防錯,以先進的製造工藝來保證產品的一致性,實現零缺陷的製造過程。
第二級是早期預警及干預,通過高精度的感測器結合的控制策略,通過遠程的雲端分析,前端的BMS相結合,能夠在事故發生的早期提前識別這種異常數據來提前預警。
第三級是安全風險發生之前,基本上事故馬上發生,通過感測器及BMS提醒駕駛員停車保證人身安全。
第四級是事故發生之後,通過被動安全及滅火措施來控制和延緩熱失控蔓延的時間。
針對整個系統安全的設計,從材料、系統、整車、電芯和整車,其實涉及的過程中我們認為最關注的應該是需求,目前的系統開發的需求,基本上來源於整車廠的SOR,可能需求並不一定完善全面,整個層級的分解過程可能也不是很專業。第二整車分解到系統,從系統分解到電芯,然後分解到材料,分解的這種需求的完整程度需要進一步的加強,我們認為,未來的設計應該首先關注的是完善需求的提出,完善需求分解的過程。
現在所有的安全測試項目國標基本上已經比較全面,但是國標畢竟是一個基礎、入門級的標準,真實的路況,還有比較嚴苛的路況,可能在標準裡面沒有體現,這樣就需要系統開發過程中識別除了標準以外的需求和測試項目,比如說蜂巢一共識別了104項測試標準,包括安全性、可靠性和性能耐久等項目。比如說國標上現在要求的一些溫度衝擊、振動等等,都是單個的產品在做相關的測試。單個產品做完了之後,可以用同一個產品再做其它驗證項目,比如說做完溫度衝擊,再做振動,再做浸水實驗,以驗證在實際使用過程中的老化引起的密封失效,後邊也會有詳細的介紹。
針對結構的設計理念,電池包都是在底盤下面,電池包有很大的作用,是承接了來源於整車側面的傳力或者是加強整車結構強度的作用。這樣的話,需要在電池包設計的過程中,模組之間或者是在電池包內部增加橫樑來提升整車的側撞。當然增加電池包和車邊緣的空間尺寸同樣有利於碰撞安全。
這個是我們識別的除去國標以外的一些特殊的測試項目,比如說整車在洗車的時候,高壓水槍的沖洗對電池包的密封會有一定的影響,整車在高速通過積水路面或者是冬天通過冰水路面的話,對電池包密封的要求不一樣。包括長時間的浸水,國標是有一個短時間的浸水要求。這樣的話對密封設計的要求是會比較嚴苛的,測試項目測試方法也會明顯的不一樣。
比如整車發生碰撞之後做這種翻轉測試,做模擬整車碰撞實驗之後,增加一些特定的實驗方法,來滿足實際使用過程中的差異。
這個是我們識別的整車級別的一些特殊的狀況,比如說行車過程中掉落,或者是整車通過障礙物時的一些測試,包括過溝,模擬側滑撞擊路邊,各種顛簸路的測試,包括掃描路況等等,其實在整車需求里,對電池包的設計、系統開發的要求並不是很明確,需要電池廠或者是系統開發單位,能夠對整車的需求有一個很深入的了解。
現在,可能大家關心的大部分都是在事故發生之後,由於設計的原因,主要是設計缺陷引起的事故大家比較關注,但是真正耐久、老化之後的壽命業內關注的程度不是很高,可靠和耐久的設計,需要進行深入的研究。比如說Pack級的壽命測試,針對結構方面的測試大部分是通過振動實驗,但是實際載荷情況並不是很吻合,所以在整包振動實驗的時候,需要結合整車的實際使用工況去採集數據做相應的模擬及測試,來保證產品的耐久。
同時緊固件開發,以及密封性能的優劣,都是通過緊固來實現的,所以選型規範及相應的驗證需要去研究。電池包內的感測器連接的可靠性,受衝擊的可能性也是需要重點去解決的。
針對電氣安全,內部的高壓部件的選型,以及高壓絕緣的耐壓等等都比國標要好。比如說現在保險和接觸器的選型我們同時需要結合電芯,尤其是方形電芯本身內部的保險(OSD),以及Pack的主保險和接觸器三者之間的匹配關係來進行系統的開發和實驗的設計。關於電器件的可靠性的設計需要考慮整車某些極端情況下的使用,如玩兒鑰匙等導致電池包反覆的上下電,可能對繼電器、預充電阻的壽命會有一定的影響,同時結合上電的控制策略,來優化我們選型的相關要求。
對於電池包熱管理的安全,尤其是熱失控前期的感測器的選型,現在主要是通過BMS的策略,以及策略的優化,再加上壓力,煙霧,或者是氣體檢測來共同判斷、識別在熱失控前期能夠及時的反饋給乘客,提醒注意安全。
Pack級的設計,從電芯到模組到整包,針對熱失控需要採取多重的防護設計,比如說電芯間增加隔熱、絕緣的材料,同時這種材料有一定的可壓縮性,這種材料目前很難找,也需要業界同仁共同去努力開發這種新的材料。通過隔熱絕緣材料來防止或者說延長電芯間的熱失控蔓延時間,通過模組間增加防撞梁等隔離措施,以及這種絕緣防火的材料,來延長增加模組之間的熱失控蔓延的時間。同時在Pack的設計過程中增加相應的排氣通道,讓它定向排氣以避免對相關人員尤其是駕駛員的傷害。
這個是我們做的一個的模擬,根據電芯熱失控之後的熱蔓延,因為這種情況比較激烈,所以在電芯和模組間增加相應隔離設計,來延長熱失控的時間。同時熱失控之後,對上蓋的衝擊或者損傷是比較明顯的,這樣的損害會直接對駕駛員對乘客造成人身傷害,所以對電池包的上蓋設計以及上蓋的選材或者是防火材料的設計也是需要重點研究和分析的。
針對熱失控之後的滅火,現在基本上主要採用的水基和乾粉滅火,起到的滅火效果並不是很理想。未來需要研究專用的吸熱的包覆材料或者是滅火的覆蓋材料可能對電動車的滅火會有一定的幫助,當然我們也希望能夠和消防單位消防機構一起去探討未來電動汽車滅火的一些方式和方案。
針對BMS的安全,整個電池包系統能夠實現正常工作,除了電芯的安全生產、結構、熱管理以外,最重要的就是控制策略。我們也有一些研究,比如說BMS最主要的功能,是監控和控制讓電池包能夠在合理的區間之內工作,超出正常區間之後BMS具有相應的報警和診斷,通過前面講述的一些措施來實現預警。
下面是關於BMS開發過程的一些要求,剛才有提到,針對電池包設計的時候,需要對整車的橫向加固以及加強,同時你要留有一定的碰撞空間,我們對電芯和模組以及Pack未來的發展趨勢也做了一個初步的構想。通過整車碰撞分析,整車可分為三個區域,一個是碰撞危險區域。第二層是高風險區域。第三層是控制電池包最安全的區域。要保證安全,電池包應安裝在第三層,這樣的話,電池包的尺寸或者是模組電芯的尺寸會受到相應的限制,比如說現在的整包寬度尺寸可能是1米3左右,隨著電芯,Pack的能量密度要求不斷提升,這個尺寸可能會縮小,假如說未來達到700mm到800mm的電芯的尺寸,未來可能會需要設計長的模組或者是長的電芯。
針對長電芯,目前業內普遍做的是EV的尺寸長度148,MEB的尺寸的是220,如果未來做到800到1米的長度的話電芯的長度可能在400到500,或者是700到800的長度,如果這麼長的電芯用傳統的卷繞工藝無法實現,需要採用全新的疊片工藝,因為電芯做長之後,卷繞可能在工藝實現上,設備上以及生產過程中的產品的一致性控制等都會有很大的挑戰,所以必須選用全新的疊片工藝來實現未來的長電芯大容量。疊片對電芯內阻有一個明顯的優勢,這樣會帶來電芯的功率提升,同時消除了卷繞的圓角空間浪費,以及做成疊片之後可提升電芯極片的壓實等,會對電芯的容量有一個明顯的提升。
同時針對安全和循環壽命我們也做過分析,用卷繞工藝在循環後期,電芯極卷會發生明顯的褶皺,尤其是圓角的位置會有斷裂或者析鋰的風險,造成安全隱患,因為疊片工藝比較整齊,後期使用過程中的膨脹會比較均勻,不存在類似的問題。
關於售後安全,國家也在強調開展電動汽車的售後服務維修,針對對電動汽車做定期的檢測和維修,作為整車廠肯定是要求推廣這些工作,電池廠我認為更主要的是要識別出作為電池,在售後維修、保養過程中,需要檢測項目、內容、方法,這個是需要後期業界同仁共同探討的,國家已經出台相應的標準做定期的維修和檢測。
針對售後保養的體系,整車廠現在針對電池汽車的安全問題,或者是特殊的事故,肯定會建立響應機制和團隊。電池廠在這個階段,長期來說都應該具有這種要求和能力,比如說我們建立由總經理挂帥的響應機制,同時建立專業的售後團隊,去針對未來市場可能發生的一些事故、特殊情況做及時的響應。
下面介紹一下蜂巢能源有限公司。蜂巢前身是長城汽車下面的一個動力電池事業部,是在2016年底、2017年初從長城汽車剝離出來,現在是隸屬於長城控股集團。
我們是2016年12月份正式成立,是一家專業從事電動汽車電池材料、電芯、模組、Pack、BMS、儲能、太陽能等專業研發和製造的單位,目前員工的人數1700人,其中研發是1000人,外部聘請專家超過380人,到2020年我們的研發投資將達到30億。這是目前我們公司的產業鏈的局部,從礦產到原材料,到電芯、模組都有研發和生產能力,未來針對儲能、太陽能、回收利用也會開展相應的業務。
我們的電芯工藝剛才也提到,我們選用的是國內首創的疊片工藝,我們認為未來疊片無論是電芯容量做大之後帶來的尺寸的增加或者是做固態電池,疊片更加合適,所以我們選擇的是方型疊片工藝。
這個是我們目前的產品情況,目前市場上應用比較多的是VDA尺寸的電芯,我們和捷威成立了合資公司在生產軟包,在今年年底我們就會有產品量產。目前不同的產品,除了型號尺寸上的差異以外,在不同應用場合和性能上,同樣有一定的布局,如快充體系的電芯,針對運營市場、計程車市場開發的運營版電芯,可以支撐五年50萬,六年60萬的質保要求,其他的個人版電芯是針對傳統的個人使用。
在電芯材料體系由目前的622 811的,純811的,然後811石墨加硅的,未來都有規劃。這個是模組產品,跟上一頁的電芯對應,我們有355的標準模組,590的模組以及非標的長模組,VDA的電芯可用於355的標準模組或者是非標準的長模組,MEB的電芯對應的是MEB的這種模組。
目前已經投入使用了4個研發中心:保定、韓國、上海、印度,印度是主要針對BMS的,韓國、日本是針對材料的,保定是比較全面的研發中心,從材料、Pack、模組、電芯研發都具備。未來會在無錫建立全新的研發總部。生產基地目前是在金壇,未來會在中國的其他地區、北美和歐洲建立新的工廠,未來總產能規劃是76GWh。
這是保定研發中心的情況,從性能、安全試驗室、電芯模組的試製線、材料的實驗室、正極材料試製線、理化分析中心等等都是具備的。
這是金壇工廠情況,金壇工廠今年底投產,明年的產能大概是5 GWh,金壇初步規劃是兩期,二期是2021年完成,2021年投產之後總產能達到12 GWh,全球的產能規劃是76GWh。

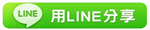
※結束「爭端」 日產批准雷諾代表獲其董事會關鍵委員會席位
※特斯拉研發新型柔軟耐用面料 可延長汽車座椅使用壽命
TAG:蓋世汽車資訊 |