汽車行業壓鑄一體化產業鏈專題報告:蓄勢待發
(報告出品方:長江證券)
新能源滲透帶動輕量化提升
提高續航里程,輕量化大有可為
汽車輕量化是在滿足汽車使用要求、安全性和成本控制的條件下,將結構輕量化設計技 術與多種輕量化材料、輕量化製造技術集成應用,實現產品減重。1)汽車輕量化並非 新興概念,國外優秀的整車廠很早就已開啟汽車輕量化進程。根據《中國汽車輕量化調 查》,在 1990-2010 年間,受歐美各國法規政策影響,歐美汽車企業製造的產品重量就 已減輕了 20%-26%。2)我國有清晰的汽車輕量化發展規劃,根據 2020 年由中國汽車 工程學會發布的節能與新能源汽車技術路線圖 2.0,預計我國 2025 年純電乘用車整車 輕量化係數降低 15%,2035 年純電乘用車整車輕量化係數降低 35%。
隨著新能源汽車行業的快速發展,汽車輕量化凸顯出以下三個優點。
1)輕量化可提升新能源汽車的續航里程。目前續航里程是新能源汽車進一步發展的主 要瓶頸,在電池能力提升逐漸達到極限的情況下,輕量化是解決該問題的另一手段。根 據 The Aluminum Association 的研究,電動汽車減重 10%和 15%可分別減少 6.3%和 9.5%的電能消耗。根據比亞迪的研究,約有 70%的能耗用在車身質量上,整車質量每 減輕 100 kg,每百公里電耗大約降低 0.5~1 k W·h。根據 DRIVEALUMINUM 的研究, 在電動汽車中使用鋁材可以將車輛的行駛里程增加與減輕重量大致相同的比例(如將重 量減少 20%可使車輛在同等電量下多行駛 20%的距離)。
2)輕量化可提高新能源汽車加速性、制動性、操穩性等諸多車輛性能,並進而提升汽 車使用壽命。一方面,減輕車重可以減少汽車輪胎和制動系統承受的壓力,進而延長這 些零部件的使用壽命,根據中國產業信息網統計,純電動汽車每減重 100kg,續航里程 可提高 6%-11%的同時,日常損耗成本可降低 20%。另一方面,減輕車重可以提高汽車 行駛性能,有效降低剎車距離,使得轉向和過彎的過程中更加靈活,同時在受衝擊時鋁 合金等輕量化材料能吸收分散更多的能量,因此輕量化可提升汽車的舒適性和安全性。
3)輕量化可在一定程度上降低整車製造成本。行駛同樣里程,車身越輕所需電池越少, 根據 DRIVEALUMINUM 的研究,電動車採用全鋁製車身結構後,每輛車可最多因此節 省 3000 美元。
材料、設計、工藝是輕量化三種途徑
汽車輕量化主要通過輕量化材料、輕量化設計和輕量化工藝三種途徑實現。 輕量化材料主要包括高強度鋼、鋁合金、鎂合金、碳纖維等,其中鋁合金材料由於可回 收、易成型、性價比高等等特點成為目前最有應用前景的輕量化材料。理論上鋁製汽車 可以比鋼製汽車減輕重量達 30%-40%,其中鋁質發動機可減重 30%,鋁散熱器比銅的 輕 20%-40%,全鋁車身比鋼材減重 40%以上,汽車鋁輪轂可減重 30%。鎂合金有更好 的減重和減震效果,但由於強度相對較低且耐腐蝕性差等缺點,目前未在汽車上廣泛使 用。
未來十年內汽車的各個主要部件用鋁滲透率都將明顯提高。根據 Ducker Worldwide 的 預測,鋁製引擎蓋的滲透率會從 2015 年的 48%提升到 2025 年的 85%,鋁製車門滲透 率會從 2015 年的 6%提升到 2025 年的 46%。具體反映在平均單車用鋁量上,1980 年 北美地區每輛車平均用鋁量為 54kg,到 2010 年增長到 154kg,預計到 2025 年每輛車 的平均用鋁量將會達到接近 325kg。根據工信部委託、中國汽車工程學會牽頭、500 位 專家歷時一年完成的大型聯合研究項目——節能與新能源汽車技術路線圖,單車用鋁的 具體的目標是:2020 年 190kg;2025 年達到 250kg;2030 年達到 350kg。
以特斯拉為例。車身方面,定位高端的 Model S/X 使用全鋁車身,相比傳統的鋼材質車 身,Model S/X 大幅地降低了重量,可以保證足夠的續航能力。全鋁車身減重效果明顯, 但是成本十分高昂,不單單是材料採購成本高,在汽車製造環節也更複雜,且全鋁車身 後期的維修成本也更高。 Model 3 作為定位中端的車型,為平衡成本和重量,放棄了全鋁車身,選擇鋁合金、低 碳鋼、高強度鋼和超高強度鋼的混合方案。Model 3 鋁合金材質更多集中在尾部,來平 衡前後重量分布,而在車身縱梁、A 柱、B 柱、車頂縱梁以及底板梁等位置使用超高強 度鋼,目的是保障車身主體框架的強度,提升車輛被動安全性。
從輕量化工藝角度,汽車上常用的鋁合金分為鑄造鋁合金和變形鋁合金。鑄造鋁合金在 汽車上應用最多,如動力系統中殼體類的發動機缸體、缸蓋等;底盤系統的轉向器殼體、 減速器差速器殼體、副車架、控制臂、車輪輪轂等。採用鍛造工藝生產的零件主要為力 學性能要求較高的零件,例如車輪、底盤懸架系統控制臂、轉向節、空調壓縮機渦旋盤 等。
隨著對強度和硬度的追求提升,其鑄造工藝也在持續改進,形成了多種工藝。按照難度 從易到難分類,分別為重力鑄造、高壓鑄造、低壓鑄造、差壓鑄造、真空壓鑄、半固態 壓鑄和擠壓壓鑄。其中重力鑄造是最原始的鑄造工藝,成本低廉,但產品強度差,高壓 鑄造是最常見的鑄造工藝,相對於重力鑄造其產品緻密性得到提高,但容易產生氣孔。 低壓和差壓屬於同一類,但差壓在低壓的基礎上結合了結晶成型,產品強度相比低壓更 高。為解決壓鑄件內部存在的氣孔和縮孔問題,能夠生產出高強度、高密性、可焊接可 熱處理、可扭曲等各種高要求的壓鑄件,真空壓鑄、半固態壓鑄和擠壓壓鑄是在普通壓 鑄的基礎上形成的新技術,對技術、設備提出了更高要求。
一體壓鑄改變行業生態,成為輕量化重大增量
降本增效,一體壓鑄有望成為製造主流
新能源車因車身結構差異,用鋁量有顯著提升。根據 DuckerFrontier 研究,新能源車單 車鋁合金使用量比傳統燃油車多 41.6%。其中由於減少了燃油車用發動機、傳動系統以 及其他看不見,使燃油車用鋁量分別減少了 24.0%、18.9%和 2.2%。而純電動車因動 力系統和車身結構件鋁合金用量更多,動力傳動系統、結構件及其他零部件分別使單車 用鋁量提高了 10.3%、48.7%、2.3%。
全鋁車身具有出色的的輕量化表現,但過去受限於成本與技術未能廣泛推廣應用。早在 1994 年奧迪 A8 就採用全鋁車身進行輕量化改進,全鋁車身可降低車身重量實現油耗和 排放大幅降低的同時,相較傳統車身具有更高安全性和可操作性。但受限於技術與成本, 全鋁車身尚未成為目前車身主流。
一體壓鑄是輕量化材料、工藝和設計的有機結合,可有效降低全鋁車身生產成本提升生 產效率。一體壓鑄是指將車身一體化鑄造,相較於傳統全鋁車身生產具有以下幾個好處:
1)產品性能更好,且生產材料回收率高。一體壓鑄基礎工藝是高壓鑄造,可實現生產 的少切削、無切削, 可避免衝壓生產的回彈情況,且廢料可以直接融化,材料的回收利 用率較高。同時,相比傳統的鑄造技術, 鑄件性能有所提高的同時,壓鑄生產的原輔料 消耗、能源消耗都有所降低。
2)模塊化生產減少零部件數量,顯著減少焊接工藝部件,解決鋁合金連接技術要求高 的問題並實現進一步減重。採用鋁合金壓鑄件設計方案可實現高度模塊化集成設計,有 效減少零部件數量,2011 款 Audi A6 的前減震器塔使用鋁合金高真空壓鑄件設計,實 現 10 個衝壓件集成為 1 個鑄件,且實現單車 10.9kg 的減重。根據 2020 年特斯拉電池 日公布數據,採用了一體壓鑄後車底的 Model Y 相較 Model 3 整塊後車底縮減 79 個零部件,焊點大約由 700-800 個減少到 50 個,下車底重量降低 30%。特斯拉的下一代車 身底盤設計方案計劃將電池盒整合進汽車底盤,用 2-3 個大型壓鑄件替換由 370 個零件 組成的整個下車體總成,並將 10%的重量,由此可增加 14%的續航里程。
3)精簡生產流程,提高生產效率。Model Y 相較 Model 3,減少了 300 台工業機器人, 簡化生產和質檢流程。
4)基於以上優點,一體壓鑄可以降低生產成本。特斯拉 Model Y 採用一體壓鑄後製造 成本下降了 40%。特斯拉下一代車身底盤設計方案可進一步降低 7%的製造成本。
技術持續進化,一體壓鑄產品有望持續延展
目前鋁合金鑄件在全鋁車身上使用較為廣泛且下車體上應用較多,未來上車體應用鑄件 的車型有望逐步增多。參考相關文獻及近十年 ECB 會議發布車型信息,統計了行業內 主流車型鋁合金鑄件的應用情況,1)整體而言,鋁合金鑄件已經成為複合材料車身、全 鋁車身、鋼鋁混合車身的必備部件,甚至已在部分高端的鋼製車身應用;2)鋁合金鑄件 主要應用在下車體上,最為典型的部件為前減震器塔、後減震器塔和後縱梁;上車體應 用鑄件的車型逐步增多,典型部件為 A 柱模塊以及 A/C/D 柱上接頭等件。
隨著壓鑄機噸位升級已經特斯拉帶來的示範效應,國外企業也積極探索車身一體壓鑄的 可能性。1)底盤:根據 2020 年特斯拉電池日信息,特斯拉將在 2024 年前實現下一代 車身底盤設計方案。斯拉將用 2-3 個大型壓鑄件替換由 370 個零件組成的整個下車體總 成,最終白車身的下車體僅由三個零件組成——前下車體、中下車體(也是電池包)、後 下車體。其中下車體設計採用結構化電池組(structural battery)的方案,即由底盤提供 保護功能,充當電池盒的角色,電池直接內置在底盤結構中。結構化電池組的設計可以更密集的包裝電芯並將電池移近汽車的質心,提高電池效率、整體結構的安全性以及汽 車靈活性。
2)副車架:2021 年 6 月,壓鑄企業漢特曼(Handtmann)研製出大型一體化壓鑄後副 車架集成了更多的性能並降低了生產成本。3)電池盒:除了特斯拉將電池盒整合到徹 底外,寶馬、大眾、本田等整車廠都有採用壓鑄的鋁合金下殼體,但多為混動車所用, 體積較小。2021 年 6 月,壓鑄企業喬治費舍爾(GF Casting Solutions)與雷諾公司一 起為雷諾兩款車開發了一體壓鑄的鋁合金電池外殼。該電池外殼尺寸為 1.00x0.55x0.15 米,重約 15 千克,並集成了冷卻電路等功能。在傳統生產工藝下,電池外殼需要組裝 100 多個單獨的部件,如框架、型材或連接點等,GF 的一體式壓鑄電池殼體將其整合 為一個整體,並減少了裝配步驟,避免了焊接和銑削等勞動密集型的連接和後工序。
3)電機電驅殼體:電驅動系統集成化發展已有時日,目前三合一電驅總成成為整車廠 選配的主流方案,且逐漸整合更多功能,如比亞迪八合一、華為 DriveOne 七合一、上 汽變速器&威邁斯七合一電驅動等。目前電機殼體主要使用壓鑄工藝,隨著電驅高度集 成化發展,一體集成式電機殼體體積也越來越大,因此預期未來電機殼體所使用壓鑄件 體積也將越來越大。
結合目前鋁鑄件使用情況,預期未來隨著壓鑄機噸位的提升以及鋁合金性能的提升,車 企可以通過一體壓鑄生產更大的鑄件。根據特斯拉「一體鑄造」技術專利推測,未來特 斯拉有可能會將車身底盤分為前車身、中間車身和左右側圍、後車身和底板幾個大型部 件一體壓鑄。1)一體壓鑄前車身可整合前縱梁、前隔板、前減震器塔、前保險杠等構 件;2)一體壓鑄中間車身和側圍可整合立柱、門檻板、地板、車頂等構件;3)一體壓 鑄後車身和底板可整合行李箱、後蓋板、後側板、後保險杠、後縱梁、後減震器塔等構 件。(報告來源:未來智庫)
一體壓鑄助力市場擴容,輕量化需求處於爆發期
電動車快速應用,一體壓鑄市場有望超百億
目前對於市場空間測算,主要有以下四個假設:
1)單車鋁合金一體壓鑄件使用量和鋁合金價格
參考目前研發進展,未來一體壓鑄工藝除應用於後車底外,還將應用於電池盒、副車架、 電機殼體等部件,根據前述部分重量計算,預計 2025 年新能源車一體壓鑄工藝部件重 量可達 100KG。 根據 DuckerFrontier 研究,純電動車因動力系統和車身結構件鋁合金用量更多,新能源 車單車鋁合金使用量比傳統燃油車多 41.6%,且無電機、電池盒等部件需要,假設 2025 年傳統燃油車一體壓鑄工藝部件重量約為 70kg。
2)使用一體壓鑄工藝的乘用車銷量
國內新能源乘用車和傳統燃油車銷量和輕量化部分預測保持一致。 根據目前有公布採用一體壓鑄工藝的國內整車廠(特斯拉、蔚來、小鵬、高合、小康汽 車(僅考慮賽力斯))2021 年銷量約佔國內新能源乘用車銷量的 22%,假設上述整車廠 2025 年所有車型標配一體壓鑄工藝,加之可能有其他整車廠後續也採用一體壓鑄工藝, 假設 2025 年使用一體壓鑄工藝的純電動車佔比達 30%。 因目前國內尚無傳統燃油車品牌宣布入局一體壓鑄,考慮到車型設計時間,假設 2025 年有 5%的傳統燃油車採用一體壓鑄工藝。
底盤、電池盒、電驅殼體放量,電動車輕量化整體空間有 望達到 1000 億以上
除一體壓鑄外,新能源尤其純電動汽車的結構升級推動輕量化單車價值提升,如底盤、 電驅殼體等均形成較大的單車價值量,疊加需求快速提升,純電動乘用車輕量化市場空 間快速擴容。 底盤:新能源汽車底盤與傳統底盤對比來看,取消原有的傳動軸、輸油管等部件,增加 了電池盒。純電動汽車省卻了發動機後,動力傳動系統大幅優化。傳統汽車一般採用發 動機前置、同時驅動後置的構架,不可避免需要傳動機構實現動力的傳輸。純電動汽車 採用電機驅動,電機的放置可以根據車型靈活調整,從而省去了傳動機構。另一方面, 純電動汽車電池包未來將主要放置在汽車底盤部分,所以需要電池盒進行加固和保護。
電驅殼體:純電動汽車採用電機驅動,電驅殼體是新能源輕量化中的重要增量部分。電 驅殼料主要有鐵質和鋁質兩種,也有少部分電機殼採用銅質的。鋁合金電驅殼體相比鐵 銅材料的優勢在於重量輕,導熱性能好,可塑性強,可壓鑄可擠壓,延伸率、穩定性、 隔音性更高。隨著電驅動系統集成化發展,電驅殼體由「分體式殼體」向「集成式殼體」 再向「一體集成式殼體」,殼體中連接件數量逐漸減少,單車價值預計在 1500 元左右。
基於以上分析,我們通過純電動乘用車銷量、單車用鋁量等假設,計算出純電動乘用車 國內輕量化市場空間: 核心假設:
1)2021 年中國新能源乘用車銷量為 332 萬輛,其中純電動乘用車銷量 271 萬輛,純電動車銷量佔比 82%。根據三部委印發的《汽車產業中長期發展規劃》,合理 假設 2025 年中國新能源乘用車滲透率達 53%,銷量達到 1353 萬輛,其中純電動乘用 車銷量 719 萬輛,純電動車銷量佔比 53%。
2)2025 年鋁合金使用量:全鋁車身可比全鋼車身減重 40%,由此測算可得鋁合金滲透 率每提升 2.5%,車身可減重 1%。根據 Dackfrontier 統計,2020 年北美汽車單車平均 用鋁量為 208kg,其中電動汽車單車用鋁量為 292kg,非電動汽車單車用鋁量為 206kg。 而根據智研諮詢數據測算,2017 年我國平均單車用鋁量為 156.2kg,根據《節能與新能 源汽車技術路線圖》設定我國 2020 年、2025 年、2030 年的單車用鋁量達到 190kg、250kg、350kg。結合兩方面信息表明,我國汽車鋁代鋼的進程落後北美約 5 年進度, 假設 2021 年中國純電單車鋁合金使用量 180kg,2025 年純電鋁合金使用量 205kg。
3)鋁合金價格:鋁合金價格假設同一體壓鑄市場空間測算保持一致。
4)2021 年鋁合金使用量:根據對目前國內主要新能源車型底盤和車身材質梳理測算, 2021 年電動車鋁合金轉向節、控制臂、副車架的滲透率分別約為 47%、41%、13%(考 慮到部分車型是部分採用鋁合金副車架,對應銷量除以一半),鋁合金電池盒滲透率 100%。由此測算出,2021 年單車鋁合金價值約為 9419 元。
新材料應運而生,免熱合金&模具鋼脫穎而出
免熱處理合金:為一體壓鑄而生,批產空間釋放
從上游材料環節來看,大型零部件壓鑄一體化工藝的橫空出世,帶動原料免熱處理鋁合 金和高端模具鋼等核心新材料亦進入產業鏈布局關注重點。
為何非免熱處理合金不可?
傳統鑄造鋁合金的生產工藝中,需要經過熱處理和機械矯直兩個必要的生產步驟。熱處 理能提升鑄件的機械性能、耐腐蝕性能、穩定尺寸,使鑄件在強度、韌性、耐腐蝕等屬 性達到車身結構件的要求。經過熱處理後,鑄件還需經過機械矯直恢復原始的幾何形狀, 進一步的穩定尺寸。值得說明的是,熱處理也會引發鑄件彎曲變形和表面缺陷的問題, 由此限制了傳統鑄造鋁合金在尺寸更大、形狀更複雜、彎曲程度更高的汽車結構件上的 應用。
壓鑄一體化工藝重點在於零部件大型化、尺寸表面精細化、一體化高效,而傳統鑄造鋁 合金的熱處理工藝受限於零部件小型化、尺寸表面不穩定化、分散化組裝,因此催生出 成分和工藝創新的免熱處理壓鑄鋁合金應運而生。 免熱合金通過對主成分元素的控制、對合金成分元素的控制、對恆量元素的控制、對有 害元素的控制,以及對整個生產流程精準的控制,實現了在不需要經過熱處理工藝下達 到和傳統鑄造鋁合金相當甚至更優的機械性能,具有優越的鑄造性能和充型能力,良好 的抗拉強度、屈服強度和韌性的同時還具有結構集成化、易加工成型和性能穩定性良好 的優點。
由於免熱處理合金無需經過熱處理流程,節省了傳統流程中消耗的大量的能量、精力和 時間,因此,下游壓鑄上,免熱處理合金能夠降本增效,使車身更輕、更安全。 1)傳統鑄造鋁合金壓鑄成零件後,需要經過焊接、鉚接組裝成車身件;免熱處理合金將 零件一次壓鑄成型,縮短了工藝流程,從焊接幾小時改善為壓鑄幾分鐘,精簡連接工序、 降本增效。 2)傳統鑄造鋁合金結構件連接點多,車身重量大;一體化壓鑄減少了連接材料的重量, 滿足汽車「輕量化」需求,提升新能源汽車節能減排和續航能力。 3)傳統鑄造鋁合金結構件在連接點處存在安全隱患,焊接、鉚接過程容易引發合金變 形,使結構件疲勞性能不穩定;一體化壓鑄從整體提升結構件的強度和韌性,比拼接的 結構件更安全。
哪些輕量化合金存在一體壓鑄潛力?
除鋁合金外,當前最有可能應用於一體化壓鑄的材料是鎂合金。從產品性能上看,鎂合 金密度比鋁合金更小,減震性能比鋁合金優異;鎂合金壓鑄件可以比鋁合金生產的更薄, 在壓鑄效率、加工性能上更有優勢;最重要的是,鎂合金具有高流動性、尺寸穩定性, 非常有利於一體化壓鑄上的應用。相比鋁合金,目前鎂合金在車身件上的應用更有限, 單車用鎂僅 10kg 左右。
鎂合金存在的上述問題正在逐步解決。1)針對易腐蝕的問題,主要採用電鍍塗層的方 法,在鎂合金表面增加一層保護層;2)針對六氟化硫的處置問題,主要通過開發六氟化 硫有效回收循環利用的技術;3)針對鎂合金材料機械性能不足的問題,主要通過在合 金成分中加入稀土元素以及採取創新的鑄造加工技術提高強度和韌性;4)針對標準體 系建設不完善的問題,鎂合金生產企業正廣泛和主機廠、壓鑄廠形成產業聯盟,推廣鎂 合金在我國車身結構件的應用。 目前鎂合金的成本相對鋁合金較高,但隨著材料技術工業的發展與突破,冶煉工藝的不 斷提高,成本會逐漸下降。未來倘若鎂合金缺陷和成本等痛點逐步解決,有望成為下一 代壓鑄一體化產業應用的重要材料。(報告來源:未來智庫)
模具鋼:壓鑄關鍵耗材,靜待國產替代
作為有「工業之母」之稱的模具鋼,其質量直接影響著製造業加工工藝的質量、產品的 精度以及生產成本。隨著下游整體升級以及裝備技術的提升,對模具材料的質量以及規 格的定製化需求更為突出。壓鑄模反覆與熾熱金屬接觸,要求壓鑄模具材料具有良好的 可鍛性、切削性、耐磨性和耐蝕性,在高溫下具有較高的紅硬性、高溫強度、抗回火穩 定性和衝擊韌度。具體來說,壓鑄模具對模具的性能要求主要為:
1) 壓鑄模具應具備良好的熱疲勞抗力。壓鑄模具表面反覆受到高溫加熱與冷卻,不斷 膨脹、收縮,產生交變熱應力,此應力超過模具材料的彈性極限時,就發生反覆的 塑性變形,引起熱疲勞。同時模具表面長時間受到熔融金屬的腐蝕與氧化,也會逐 漸產生微細裂紋出現早期龜裂,大多數情況下,熱疲勞是決定壓鑄模具壽命的最重 要因素。
2) 壓鑄模用鋼在高溫下應具有足夠的強度、硬度、韌性、塑性及耐熱性能。鋁合金壓 鑄模具受到熔融金屬注入時的高溫、高壓和熱應力作用,容易發生變形,甚至開裂, 因此,模具鋼在工作溫度下應具有足夠的高溫強度與韌度,以及較高的硬度和耐熱 性能。
3) 壓鑄模具應具備良好的抗熔融金屬的損傷性。隨著一體化壓鑄時代的到來,對壓鑄 機的要求也逐漸轉向大型化,壓鑄壓力也在增大,已從低壓的 20-30MPa,提高到 高壓 150-500MPa。高溫高壓澆鑄可產生明顯的熔融損傷,因此,模具材料必須具 有較大的高溫強度、較小的對熔融金屬的親和力,要求模具表面粗糙度小,並附有 適當的氧化膜、氮化層等保護層,且不存在脫碳層。
模具鋼優質的性能使其成為一體壓鑄產業中不可或缺的材料,目前較為主流模具鋼為 H13 型(熱作模具鋼)和 Cr12MoV 型(冷作模具鋼)。模具鋼下遊行業具體應用在國際 市場中首當其衝的是汽車製造,汽車行業是模具鋼原料消費的第一大行業,90%以上零 件都由模具成型,同時使用熱作、冷作及塑料模具鋼。此外,家電生產也需大量塑料模 具和冷沖模具,特別是大型塑料模具和冷沖模具。而電子通訊行業 60%-80%的零部件 都要依靠模具成型,這意味著電腦、手機、電子設備等都需要大量的模具,精密衝壓模 具和精密塑料模具約佔電子通訊市場的 20%左右。同時,房地產業中大量建築塑料型 材,塑料門窗、PVC 水管等都依賴大中型模具材料,以塑料和鋁合金擠壓模為主。
目前,我國高端產品對進口模具鋼的依賴仍然較大,我國模具鋼每年的凈進口總量約 10 萬噸,其中精品模具鋼佔據了國內模具鋼高端市場份額的 60%。進口來源主要有日本大 同、日立、德國 Schmiedewerke Gr?ditz GmbH(葛利茲鋼廠)、瑞典 ASSAB Group(一 勝百集團)、美國芬可樂等。進口模具鋼價格要比國內同類產品高出 3-6 倍,但高端產 品對進口模具鋼的依賴仍然較大,原因是國外模具鋼的品質主要體現在純凈、均勻、組 織細小、尺寸精確。
產業鏈存在哪些投資機會?
應用環節:市場大幅擴容,輕量化零部件迎來快速增長
相比於傳統產品,一體壓鑄產品具有高性能、生產效率高、生產成本低等優勢,因此未 來一體壓鑄市場有望快速擴容。預計 2025 年國內一體壓鑄件市場規模有望達到 128.6 億元,2021-2025 年 CAGR 約為 183.7%。鋁合金普通壓鑄、鍛造、擠壓等在車身、底 盤、電池盒等仍有廣泛應用,預計 2025 年純電動乘用車輕量化相關產品的市場空間將 達到 1078 億元,2021-2025 年 CAGR 約為 43.3%。
長期來看,一體壓鑄零部件仍將主要由 Tier 1 供應,且有以下三點優勢的企業具有一定 競爭優勢。1)快速的產能投放速度;2)具有一定壓鑄先發優勢;3)較強的營運能力, 包括較好的內部管理和供應鏈管理等。
拓普集團:布局壓鑄業務,蓄勢待發
拓普已具備了輕合金領域六大工藝能力,可完全覆蓋底盤部件及車身部件,提供一站式 輕量化解決方案。拓普已量產的產品類型涵蓋底盤系統、動力總成結構件、電池包結構 件、車身結構件以及熱管理閥板等。根據不同的工藝,產品壁厚設計範圍寬,成型後屈 服強度能實現從 100MPa 到 350MPa 全覆蓋,延伸率從 2%到 12%全覆蓋。基於以上 布局,拓普可為客戶提供定製化服務,針對客戶產品使用場景和性能要求,推薦最適合 的輕量化工藝。
拓普已根據 7200T 壓鑄機進行產品研發。2021 年 9 月,拓普與力勁集團就汽車輕量化、 大型汽車結構件一體化成型項目達成全新戰略合作協議,在已經購置了近 100 台力勁壓 鑄機的基礎上,拓普向力勁繼續訂購 21 套壓鑄單元,其中包括 6 台 7200 噸、10 台 4500 噸和 5 台 2000 噸的壓鑄設備。基於 7200T 真空鑄造設備,拓普將前沿的鑄造一 次成型技術迅速地應用在了一體式後艙輕量化量產零件上。對比傳統的衝壓焊接工藝, 一體鑄造將 70 多個部件整合為 1 個部件,同時也不再需要焊接工藝,2022 年 2 月,拓 普生產的國內首個基於 7200 噸巨型壓鑄機正向開發的一體化超大壓鑄車身後艙正式量 產下線,結構件長寬分別近 1700mm 和 1500mm,可實現 15%~20%的減重效果。
旭升股份:深度綁定特斯拉,新客戶持續拓展
旭升主要從事精密鋁合金零部件的研發、生產與銷售,聚焦新能源汽車領域,涵蓋多個 汽車核心系統,包括傳動系統、控制系統、懸掛系統、電池系統等。從工藝角度,旭升 同時掌握壓鑄、鍛造、擠壓三大鋁合金成型工藝並均具備量產能力,能夠針對不同客戶 需求提供一站式輕量化解決方案。
旭升客戶範圍持續拓寬,營業收入快速增長,公司前五大客戶佔比近年持續下降,其中 特斯拉營收佔比也持續下降。公司近年客戶持續開拓,與長城、蔚來、寧德時代等新客 戶展開合作。2021 年公司前五大客戶貢獻營收 20.02 億元,占公司營收比重為 66.20%, 其中特斯拉為公司貢獻營收 12.07 億元,占公司營收比重為 39.93%。
愛柯迪:中小鋁壓鑄件龍頭,發力布局中大件壓鑄業務
愛柯迪是中小鋁壓鑄件龍頭,定位「新能源汽車 智能駕駛」產品市場,近年汽車用通 用中小件市場佔有率持續提升,經營優勢明顯。受益於新業務及新客戶開拓,公司近年 營業收入穩步增長。2021 年,公司營收 32.1 億元,同比增長 24.8%,受原材料及海運 費價格持續上漲、人民幣升值等因素影響,公司歸母凈利潤 3.1 億元,同比下降 27.2%。
愛柯迪發力布局中大件壓鑄業務,擬購入 10 台 3200T 以上噸位壓鑄機。根據 2021 年 底愛柯迪智能製造科技產業園環評信息顯示,公司擬為該產業園購入 45 台壓鑄機,其 中包括 2 台 8400T、 2 台 6100T 和 4 台 4400T 和 2 台 3200T,以及 35 台 3200T 以 下噸位壓鑄機。
文燦股份:深耕鋁合金精密鑄件市場,全力布局一體壓鑄業務
文燦股份深耕鋁合金精密鑄件市場,受益於公司新能源汽車產品放量,近年營收快速增 長。2021 年公司營收 41.1 億元,同比增長 58.1%,歸母凈利潤 1.0 億元,同比增長 16.0%。
2021 年起,文燦股份持續重點布局一體壓鑄業務,目前進展順利。1)2021 年,與力 勁科技集團有限公司簽訂了《戰略合作協議》,向力勁採購了 9 台大型壓鑄機,包括 2 台 9000T、兩台 6000T、三台 4500T、一台 3500T、一台 2800T,用於研發及生產車身 結構件、一體化電池盒托盤、電機殼、變速箱殼體等。截至 2022 年 4 月,除一台 9000T 壓鑄機外,其餘 8 台壓鑄機已完成安裝調試,預計最後一台 9000T 將於今年 5 月份安 裝調試完畢並在 6 月份為客戶超大型一體化車身結構件產品試模。2)文燦股份在 6000T 壓鑄設備上已於 2021 年 11 月 18 日完成首次半片式後地板的試製,試製產品在某新勢 力客戶整車廠中完成白車身安裝下線;此外 9000T 壓鑄機系當下全球噸位最大的壓鑄 機,定點產品已經開始試製階段工作,用於另一知名頭部新勢力客戶的 SUV 車型。3) 2022 年,文燦股份將繼續向力勁採購 9 台大型壓鑄機,包括 2 台 2800T、3 台 3500T、 2 台 4500T 和 2 台 7000T,用於超大型一體化結構件及車身結構件的生產,進一步滿 足公司的產能需求。4)2022 年 5 月,與立中集團簽訂《戰略合作框架協議》,在新能 源汽車的大型一體化車身結構件、一體化鑄造電池盒箱體等產品的材料開發和工藝應用 領域建立戰略合作關係。
新材料:海外先發,國產替代加速崛起
美國鋁業、萊茵費爾德、特斯拉、立中集團、廣東鴻圖等企業紛紛布局免熱處理合金, 和目前廣泛在車身的傳統鑄造合金 AlSi9MgMn 經過熱處理後的性能接近。隨著國產研 發技術和工藝成本優化,未來免熱處理合金的國產替代大勢所趨。
萊茵費爾德、美國鋁業:深耕多年的老牌企業
作為傳統的鑄造鋁合金生產商,萊茵費爾德和美國鋁業深耕鋁合金行業多年,擁有多項 技術專利。萊茵費爾德研發生產的 Silafont-36(AlSi10MgMn)是目前車身應用最廣泛的傳 統鑄造鋁合金材料,現存許多產品都是基於該產品改進。美鋁研發的免熱合金 C611 系 列具有極佳的流動性,被歐美許多壓鑄廠家廣泛地應用於薄壁結構件(例如減震塔)的 生產。
立中集團:成本和技術領先,蓄勢待發
根據立中集團年報,公司通過材料成分配比、工藝路線設計、性能指標設定、工藝過程 保障等方面綜合調控,使得公司的免熱處理合金在抗拉強度、屈服強度和延伸率等方面 表現出了良好且均衡的機械性能,在保持高強度和良好鑄造性能的基礎上,延伸率較傳 統壓鑄材料提升了 5 倍以上,能夠更好的應用於高強、高韌、超大型一體化壓鑄零部件 的生產。
根據公司公告,受疫情對汽車產業鏈的影響,今年二季度對公司產品主要是鑄造合金、 鋁合金車輪的銷量有一定影響。但因中間合金業務應用行業比較分散,同時受高端晶粒 細化劑、航空航天用特種中間合金等高端產品逐步提升、鋁合金車輪板塊報價模式調整、 海運費聯動、公司出口業務穩定發展、內外鋁價正掛以及美元升值等諸多有利因素影響, 因此這些因素或有望對沖疫情擾動。
高端模具鋼:天工國際龍頭布局,靜待花開
天工國際作為全球工模具鋼優質龍頭,在全球經濟波動周期中,通過自身極強成本控制、 產品技術升級、精細化管理等綜合競爭力,成功穿越下行周期,實現穩健成長。 公司 3 月官網發布,7000 噸快鍛項目正式進入施工階段,通過完善公司產品結構體系, 以更好地滿足市場需求,如在一體成型壓鑄領域中對大規格模具鋼的廣泛需求。該項目 完成後,公司圓鋼產品最大規格將從目前的直徑 880mm 擴展到直徑 1200mm 以上,模 塊產品將從 800mm 厚增加到 1200mm 厚以上,產品規格進一步豐富。
(本文僅供參考,不代表我們的任何投資建議。如需使用相關信息,請參閱報告原文。)
精選報告來源:【未來智庫】。未來智庫 - 官方網站

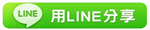