汽車行業一體壓鑄研究報告:一體鑄造大勢所趨,自主品牌大有可為
(報告出品方:中信證券)
特斯拉引領行業趨勢,一體鑄造蔚然成風
特斯拉開創一體鑄造技術先河
特斯拉 2019 年提出「一體鑄造」技術,計劃在 Model Y 上應用。2019 年 7 月,特 斯拉發布新專利「汽車車架的多向車身一體成型鑄造機和相關鑄造方法」,提出了一種車 架一體鑄造技術和相關的鑄造機器設計。該技術將通過多向壓鑄機、車輛覆蓋件模具和幾 個可以相對於覆蓋件模具平移的凸壓模具,實現對汽車白車身的鑄造成型。此類凸壓模具 會分別移動至鑄造機中央的鑄造區,負責不同部件的鑄造,在一台機器上完成絕大部分車 架的鑄造工作。同年,特斯拉 CEO 埃隆馬斯克在特斯拉電池日上表示,特斯拉的 Model Y 車型白車身將轉向鋁鑄件設計。「當我們引入大型鑄造機之後,就可將 70 個部件變成 1 個, 機器人無需將這麼多部件組裝在一起,從而大大減少成本。」
2020 年,一體鑄造技術在 Model Y 上開始應用。2020 年,特斯拉開始與壓鑄設備商 義大利意德拉合作,使用 6000 噸級壓鑄單元 Giga Press,採用一體成型壓鑄的方式生產 Model Y 白車身後地板總成。根據 2020 年特斯拉電池日發布的信息,Model Y 的後地板通過應用一體壓鑄技術,將原先通過衝壓等工藝生產的 80 個零件集成為 1 個鑄造零件, 製造成本能夠降低 40%。同時,特斯拉公布了下一代白車身設計方案,整車地板總成將由 2~3 個大型壓鑄件組裝而成,電池包採用了 structural pack 的設計理念,使得整個白車身 具有更高的強度和剛度。
Model Y 一體壓鑄前艙落地柏林工廠,Cybertruck 後地板亦將應用。2021 年 5 月 17 日,德國壓鑄專家阿克塞爾·圖爾克(Axel Turck)在推特分享了一體壓鑄前機艙試製 零件,提到特斯拉 Model Y 車型未來將應用一體鑄造技術生產更多的零件。10 月,特斯 拉於柏林工廠開放日上對公眾展示了一體壓鑄機模具、一體壓鑄 Model Y 前機艙,結構電 池包(structural pack)等核心技術方案,表明未來柏林工廠生產車型將全面使用「一體 壓鑄」工藝。在 2020 年四季度業績電話會議上,馬斯克表示新一代皮卡 Cybertruck 的後地板將也會應用一體化壓鑄技術,且將使用更大噸位的 8000T 壓鑄機進行生產。在 2022 年一季度財報中,特斯拉汽車業務毛利率 32.9%,整體毛利率 19.2%,均創下歷史新高, 其中就有一體鑄造技術帶來的貢獻。
自主新勢力奮起直追,積極擁抱行業變革
國內新勢力中,蔚來 ET5 率先應用一體鑄造技術,輕量化、安全性領先。2021 年 10 月,蔚來汽車宣布成功驗證開發了可用於製造大型壓鑄件的免熱處理材料,將會應用在蔚 來第二代平台車型上。新材料避免了傳統壓鑄件在熱處理過程中引起的尺寸變形及表面缺 陷。2021 年 12 月,蔚來在 ET5 發布會上正式宣布將開始採用一體鑄造工藝,ET5 將使 用超高強度鋼鋁混合車身,使車身後地板重量降低 30%,後備箱空間增加 7L,整車抗扭 剛度高達 34000N·m/deg。
小鵬汽車一體壓鑄技術已在規劃當中,計劃自建產能。在小鵬 2021 年業績發布會上, 董事長何小鵬宣布將於 2023 年發布兩個新平台及其首款車型,並將使用超大一體化壓鑄 新工藝。根據武漢當地媒體沌口之聲,2021 年 7 月小鵬正式啟動武漢項目,將建設一系 列工藝車間,年總產能約 10 萬輛。根據武漢經濟技術開發區(漢南區)自然資源和規劃 局,2021 年 10 月,小鵬已正式申報「小鵬汽車武漢產業基地項目」規劃建築方案,預計 今年 10 月投產,其中包括一體化壓鑄工藝車間。小鵬汽車武漢工廠還將引進一套以上超 大型壓鑄島及自動化生產線。
高合汽車在一體鑄造材料、製造端推進領先。2021 年 12 月,高合汽車與上海交通大 學輕合金國家工程中心展開戰略合作,共同研發 TechCast?超大鑄件用低碳鋁合金材料, 該材料流動性高於同級別材料 15%以上、強塑積高出 30%以上,保證了整車碰撞等性能 達到更高維度。2 月 25 日,高合汽車與拓普集團合作開發的 7200T 一體化超大壓鑄後艙 成功下線。該部件應用了上海交大的合金材料,實現了 15%~20%的減重與工藝複雜度的 大幅降低,整個開發周期也縮短了 1/3。截至成功下線時,該壓鑄機是汽車零部件領域已 知最大的一體化鋁合金壓鑄件,未來也將應用於高合各類車型中。
傳統車企不甘示弱,加速跟進一體鑄造
大眾計劃於 SSP 平台開始應用一體壓鑄,樣件已於卡塞爾工廠下線。大眾現有的大部分電動車型均是基於MEB平台打造, 而新一代電動汽車平台 SSP 無論從軟體還是硬體架構上都將提供更好的可拓展性,Trinity 車型則是基於 SSP 平台打造的首批車型之一。
賓士發布一體化壓鑄成果,性能提升顯著。2022 年 1 月,賓士發布全新概念車 VISION EQXX。車身的後部及前部減震塔頂應用了和特斯拉同樣的仿生工程結構部件,整個車身 由 3 塊組成:前後分別有一塊一體壓鑄鋁合金鑄件,中間有一套結構電池組。這樣的設計 有望減輕車身 15-20%的重量。在這一設計的助力下,VISION EQXX 能耗達到 10kw·h/ 百公里以下,實際用電里程超過 1000km。
變革推動行業擴容,自主有望實現領先
高壓鑄造是鋁合金材料最高效的成型方法
高壓鑄造(壓鑄)是將熔化狀態金屬在模具內加壓冷卻成型的精密鑄造方法。金屬制 品主要採用機床銑削、鈑金成型焊接、鑄造三種工藝生產。其中鑄造主要生產內部結構復 雜,難以用鈑金成型或機床銑削不具有經濟性的零件。鑄造主要分為砂型鑄造和特種鑄造 兩類,壓鑄屬於特種鑄造範疇。壓鑄全稱高壓鑄造,是一種將金屬熔液壓入鋼製模具內施 以高壓並冷卻成型的一種精密鑄造法。壓鑄適合鑄造結構複雜、薄壁、精度要求較高、熔 點比鋼低的金屬零件(鋁、鋅、銅等)。作為一種幾乎無切削的近凈成形金屬熱加工成型 技術,其產品具有精密、質輕、美觀等諸多優點,廣泛應用於汽車、家電、航空、機械等 諸多行業。
高壓鑄造是批量生產鋁合金鑄件的最高效生產方式。與採用石英砂做鑄造模具的重力 鑄造相比,高壓鑄造具有以下優勢:1、模具可以反覆利用;2、通過模具內的冷卻系統可 以實現快速成型並實現連續生產;3、冷卻中對熔融金屬施加壓力保證零件具備更好的應 力強度;4、金屬模具內部尺寸精確,可做到精密鑄造。壓鑄雖然高效,但因模具材料均 為鋼製,因此只能製造熔點比鋼低的金屬。目前高壓鑄造行業所使用的基材主要是鋁/鎂/ 鋅/銅等合金材料,其中鋁合金的應用最為廣泛。鋼材因熔點加高,因此只能採用每次需要 破拆石英砂模具的重力鑄造,效率較低。與高壓鑄造相近的是低壓鑄造,低腰鑄造同樣采 用 可循 環的 鋼製模 具,但 低壓 鑄造 壓射壓 力僅在 1~5MPa, 遠 低 於高壓 鑄造 的 300~600MPa 水平。低壓鑄造適合生產壁厚較厚的鑄造鋁/鎂/鋅/銅合金等材料的零件,例 如汽車輪轂、皮帶輪等。雖然低壓鑄造設備結構簡單投資相對較低,但其生產效率和零件 強度低於高壓鑄造,所以在產品適合採用高壓鑄造且需要大規模批量生產情況下,高壓鑄 造是鋁/鎂合金等鑄件的最高效生產方式。
壓鑄機和壓鑄模具是壓鑄生產的核心設備,結合周邊配套設備即為壓鑄島單元。壓鑄 機就是用於壓鑄零件生產的機器。壓鑄機相對標準化,通過安裝不同的壓鑄模具可實現多 種形狀壓鑄零件的生產。當壓鑄生產時,現將熔融的液態鋁合金倒入壓鑄機的壓射機構內, 壓射機構將鋁液推入模具內並加壓成型,通過模具內的冷卻系統將鋁合金零件快速冷卻至 固態,最後模具打開由機器人取出零件、清理噴塗脫模劑再進行下一個循環生產。壓鑄生 產溫度高、煙氣多、雜訊大,業內通常採用自動化生產。壓鑄機周邊需要配套熔煉爐、機 邊爐、取件和清理噴霧機器人、切邊設備、機加工機床、檢測設備、冷卻系統、排氣系統 等,上述周邊設備與壓鑄機、壓鑄模具組合在一起的壓鑄生產單元即為壓鑄島。
減重需求促使車身採用鋁合金替代鋼材,壓鑄鋁件逐漸應用於車身結構件。受制於壓 鑄機規格,傳統壓鑄生產零部件尺寸通常在 600mm 以內,以汽車零部件、電機外殼、手 機機殼、消費品金屬件為主。過去十年間,壓鑄機最大規格在鎖模力 5000 噸以內,需求 主要用於生產商用車變速箱外殼和乘用車發動機缸體。新能源車普及和燃油車減排趨勢使 車身結構件鋁代鋼減重需求日益增加。大眾、寶馬等德系廠商已逐步在白車身複雜結構處 採用壓鑄鋁合金件替代傳統鈑金焊接件,壓鑄車身結構件尺寸逐漸增大。
一體鑄造技術有望顛覆汽車的製造方式
一體壓鑄工藝是汽車製程中的顛覆性技術,壓鑄機有望成為汽車製造領域的核心裝備。 從上世紀初焊接技術逐步成熟以來,汽車車體製造工藝均以鈑金衝壓 焊接為主。上世紀 70 年代以前,汽車車體焊接主要由人工作業完成。1970 年代數控技術逐步成熟,工業機 器人誕生,最早應用於汽車焊接工藝。過去 50 年間,汽車車身製造工藝始終以鈑金衝壓 機器人焊接為主。本次特斯拉一體壓鑄技術有望使汽車車體製造工藝發生重大變革,壓鑄 機有望取代焊接機器人成為造車核心裝備。
「一體壓鑄」簡化車身製造工藝流程,整合供應鏈環節。一體壓鑄工藝將取代傳統車 身結構件的組件衝壓和焊接環節,特斯拉稱其新一代全壓鑄底盤可減少 370 個零件,車門 和前後兩蓋結構件也同樣可用壓鑄工藝,零件數量銳減,車體製造流程大幅簡化。同時, 整車廠內原先複雜的機器人白車身焊接線也被大幅簡化,僅需要將若干車身壓鑄組件和外 覆蓋件組裝焊接即可。車體製造管理流程和所需人力也相應降低。
車身重量減輕,減少電池裝機量,電池降本是鋼換鋁式車身材料增加成本的 6.6 倍。 特斯拉新一代一體壓鑄底盤有望降低 10%車重,對應續航里程增加 14%。以普通電動車 電池容量 80kwh 為例,若採用一體壓鑄車身減重並保持續航里程不變,則電池容量可減少 約 10kwh。按照磷酸鐵鋰電池 pack 成本 800 元/kwh 計算,則可降低成本 8000 元。
一體壓鑄工藝可大幅減少塗膠工藝環節。塗膠是傳統焊接白車身重要工藝部分,通常 由機器人完成塗膠工藝。因點焊使鋼板間存在縫隙,傳統白車身塗膠主要起到密封防水、 增加車體強度、降低鈑金件間的摩擦和震動的作用。改為一體壓鑄車體後,零件面積大幅 增加,不再需要繁瑣的塗膠環節彌補焊接鈑金件間的縫隙,生產流程再次簡化。
壓鑄廢品、流道等可再次熔煉,材料利用率超 90%,遠高於衝壓。傳統衝壓-焊接工 藝,通常板材利用率僅為 60%~70%,衝壓剩餘邊料只得按廢舊金屬出售。而改為一體壓 鑄後,因壓鑄時可反覆熔煉,因此廢品、壓鑄流道、邊料等廢料可返回熔煉爐再次利用。 壓鑄工藝對材料利用率在 90%以上,遠高於衝壓工藝,再次降低生產商成本。
車身生產車間佔地面積減少 30%以上。相較於 300 多台機器人組成的白車身焊接線, 一體壓鑄工藝採用的壓鑄島佔地面積更小。特斯拉採用壓鑄工藝的新工廠佔地面積節省 35%。同時因生產流程簡化,原先由零部件廠供應的組件衝壓、組件焊接環節取消,相關 場地同時不再需要,更進一步降低全產業鏈的用地面積。
部件端:壓鑄結構件滲透加速,潛在百倍成長空間
一體壓鑄技術帶來行業百倍以上成長空間
鋁高壓鑄造工藝已較多應用於車身結構件。鋁合金鑄造性能好,被廣泛用於結構複雜 的零件和殼體,如發動機機體、副車架、白車身和轉向節等。鋁壓鑄件相比鑄鋼和鑄鐵件 具有密度低、比強度高等諸多優點。在同等排量的發動機中,全鋁發動機相比普通發動機 能夠減輕 20 公斤。在汽車白車身系統上,一個整體鑄造的車身結構件,如鋁製減震塔 (shock tower)或後縱梁(rear rail)等零部件,能夠替代 5-10 個衝壓零部件,重量更輕, 且節省了焊接成本。
鋁壓鑄結構件成本較高,主要應用於豪華品牌車型。鋁壓鑄結構件雖然比強度高、生 產效率高、集成優勢強,但是由於鋁合金成本遠高於鋼,且高壓壓鑄設備價格昂貴,因此 小尺寸的鋁壓鑄結構件成本顯著高於鋼衝壓焊接結構件。當前應用鋁壓鑄結構件的多為 35 萬元以上的豪華品牌車型,平均單車價值不到 3000 元。以凱迪拉克 CT6 為例,車身上前 減震他、前翼子板支架、扭轉盒等零件均採用鋁合金高壓鑄造工藝生產,單車價值約為 2750 元。
壓鑄車身結構件行業多由喬治費歇爾、麥格納等外資主導,國內文燦、鴻圖等也有配 套。海外高壓鑄造供應商起步早,因此產品、技術和客戶覆蓋上普遍領先於國內企業。從 全球來看,高壓鑄造行業規模較大的供應商有瑞士喬治費歇爾(Georg Fischer)、加拿大 卡斯馬(Cosma,麥格納旗下車身事業部)、德國德志(DGS)、日本利優比等。在壓鑄車 身結構件上,喬治費歇爾、卡斯馬和德志等企業具有先發優勢,如喬治費歇爾在鋁車身結 構件真空高壓壓鑄工藝上有超過二十年歷史。麥格納深耕鋁壓鑄多年,鋁壓鑄相關技術持 續領先,2022 年 4 月憑藉 Aural 5R 鋁合金(即鋁壓鑄金)入圍素有汽車界奧斯卡獎之稱 的 PACE Pilot 創新前瞻獎決賽。國內壓鑄車身結構件參與者主要有文燦股份、廣東鴻圖和 拓普集團等。
「一體壓鑄」技術有望快速滲透,車身結構件一體壓鑄具備百倍成長潛力。考慮「一 體壓鑄」技術對白車身生產降本帶來的顯著效應,我們預計全球主機廠有望快速跟進這一 技術路線。據產業調研,我們測算 2022 年一體化壓鑄件全球市場空間約為 22 億元;到 2030 年,我們預計全球主機廠將都跟進這一技術趨勢,乘用車一體壓鑄全球滲透率為 30%, 在保守情形下,預計一體壓鑄技術將應用於前後底板、電池盒體、前副車架、電機/電驅外 殼等部位,合計單車價值量約 1 萬元,對應行業市場空間 2460 億元,8 年 CAGR 達 80%; 中性情況下,預計電池盒蓋板、中控台骨架、副車架等部件也將應用一體壓鑄技術,合計 單車價值量約 1.8 萬元,對應市場空間 3739 億元,8 年 CAGR 達 90%;樂觀情況下,預 計 A/B/C 柱側圍、車頂及座椅骨架也將採用一體壓鑄技術,合計單車價值量約 2.5 萬元, 對應市場空間為 4477 億元,8 年 CAGR 達 94%。(報告來源:未來智庫)
行業新機遇下國內廠商紛紛布局
多家供應商相繼採購大型設備,進軍一體化壓鑄行業。國內多家汽車鋁合金精密壓鑄 件公司布局一體化壓鑄項目,加快引入大型壓鑄設備和免熱處理材料研製的步伐。上市公 司中,文燦股份 2021 年 5 月向力勁集團採購包括 2 台 6000T 在內的 7 台中大型壓鑄單元, 2021 年 8 月再簽署戰略協議購買 2 台 9000T 壓鑄機(全球最大智能化壓鑄設備),2022 年計劃再採購包括 2 台 7000T 在內的 9 台大型壓鑄機。廣東鴻圖 2022 年 1 月向力勁集團 簽訂包括 2 套 12000T 在內的 8 套大型及超大型智能壓鑄單元。泉峰汽車以馬鞍山生產基地作為公司最主要的大型壓鑄產能部署地,首批將新增包括 1 台 8000T 和 1 台 6000T 在 內的 7 台大型壓鑄設備,2022 年底前預計將完成安裝和調試。拓普集團 加快推進輕量化 戰略,於 2021 年 9 月向力勁集團採購 21 套壓鑄單元,其中包括 6 台合模力 7200T、10 台 4500T 的大型壓鑄機。愛柯迪建設寧波江北高新技術產業園區,擬購包括 2 台 6100T 和 2 台 8400T 在內的 35 台 1000T 以上壓鑄機,目前已擁有 4400T 等規格型號壓鑄機。 旭升股份將在未來三年內向海天金屬引進型號 1300T-4500T、6600T 和 8800T 的多套冷 室壓鑄島。
非上市公司中,寧波海威公司 6600T 壓鑄單元生產的超大型結構件一體化電池包產品 已於 12 月下線,規劃在紹興工廠安裝 6 台 6600T 和 9000T 的大型壓鑄設備,用於生產新 能源汽車超大型結構件——前機艙、後車體及電池包箱體等產品。瑞立集團於 2021 年 4 月向力勁集團訂購 6800T、8000T 和 9000T 超大型智能壓鑄單元,並與力勁集團、輕合 金精密成型國家工程技術中心簽署戰略合作協議。美利信科技 2021 年 12 月美利信科技 HDC8800T 壓鑄機入場,已於 2022 年 4 月中旬正式投入使用。並與重慶大學國家鎂合金 材料工程技術研究中心簽署戰略合作協議。
布局進度領先,文燦股份走在行業前列。文燦股份在大型一體壓鑄設備落地進度、項 目定點、產品開發試製等方面均走在行業前列。設備落地進度方面,7 台中大型壓鑄單元 已全部到位並完成安裝調試;1 台 9000T 壓鑄機已在天津工廠完成安裝,處於產品試製階 段;今年 5 月已有 1 台 9000T 壓鑄機在南通工廠完成安裝調試,6 月試模。模具設計方 面,子公司文燦模具積累了大量車身結構件的項目經驗,掌握真空高壓壓鑄模具,能夠滿 足鋁合金車身結構件對於壁厚的要求。工藝管理方面,子公司雄邦壓鑄(南通)擁有配套 賓士、特斯拉、蔚來、小鵬、廣汽 AION 等客戶的豐富經驗,在車身結構件生產技術上領 先國內同行。產品開發試製方面,2021 年 11 月 18 日,南通雄邦工廠 6000T 超大型壓鑄 島成功試模,採用一體化壓鑄成型的汽車零部件成功下線;2022 年 4 月,天津雄邦壓鑄 工廠 9000T 超大型一體化鋁合金後地板產品試製成功。項目定點方面,文燦股份與蔚來建 立了密切的合作關係,已為蔚來三款量產車型供應車身鋁合金結構件。截至目前,公司還 與 5-6 家國內外客戶進行大型一體化車身結構件產品的研發,預計在 2023 年-2025 年開 始量產。
廣東鴻圖完成產品試製,免熱處理材料研發領先。公司於 2022 年 1 月成功試製 6800T 新能源汽車超大型一體化鋁合金後地板壓鑄結構件產品,標誌該大型壓鑄單元正式投產。 同時,廣東鴻圖與力勁集團、廣州市型腔模具製造有限公司及廣東鴻勁金屬鋁業有限公司 共同就 12000T(噸)超級智能壓鑄單元開發項目開展合作,目前 12000T 設備正處於設 計開發階段,預計將於今年 8 月投入使用並進行動力電池托盤產品試製。此外,公司在免 熱處理材料研發方面也已取得一定的成效,目前免熱處理鋁合金材料已獲得國家授權發明 專利,性能和使用成本處於領先水平,並已應用於一體化產品開發試製。
拓普集團超大結構件率先下線,免熱處理材料實現突破。2022 年 2 月 25 日,拓普集 團與高合汽車合作的 7200T 一體化超大壓鑄後艙量產下線,實現了 15%-20%的減重效果 標誌著拓普集團成為了國內首個量產超大型一體化鋁合金結構件製造技術的汽車零部件 供應商。此外,在材料方面,拓普集團與華人運通及上海交通大學合作,全球首家成功應 用了其聯合發布的 TechCast?高強韌性免熱處理鋁合金材料,該免熱處理的合金材料可以 避免因熱處理帶來的零件尺寸變形及表面缺陷等問題,是汽車產業製造端低碳合金技術的重大突破,該材料流動性高於同級別材料 15%以上、強塑積高出 30%以上,保證了整車碰 撞等性能達到更高維度。
設備端:2030 年行業具有 30 倍空間,力勁科技行業領先
一體壓鑄趨勢下,壓鑄機成為造車核心裝備
一體壓鑄工藝將主要取代白車身、四門、後蓋結構件的衝壓和焊接環節。根據特斯拉 電池日(2020 年 9 月 3 日)公布的車身一體鑄造技術和力勁科技調研可知,未來汽車的 覆蓋件衝壓生產的方式不會改變之外,其餘車身、電池盒、車門骨架、後蓋、前後副車架等結構件的衝壓和焊接環節均可以採用壓鑄工藝生產,這將使得整車白車身生產工藝大幅 簡化。A/B 柱、車頂和座椅骨架是否能夠採用鋁壓鑄工藝代替鋼材衝壓焊接,目前還在探 討當中。
前地板、後地板和電池托盤有望在 2022 年實現一體壓鑄技術的應用。根據特斯拉電 池日公布的信息,其製造技術創新主要集中在前、後地板和電池包:前、後地板均應用一 體鑄造技術,將數十個衝壓零件焊接在一起的總成替換成一個整體的大型鑄件;電池包中 的電芯採用了大圓柱無極耳設計,能夠與電池殼緊密貼合,和結構件一樣實現承重功能。 特斯拉於 2021 年在 Model Y 車型的後地板上量產一體壓鑄技術,完成前地板一體壓鑄件 試製,兩者均採用 7000 噸級壓鑄機生產;若後期考慮採用一體壓鑄工藝生產電池托盤, 則需要用到 1.2 萬噸級別的壓鑄機。2022 年 1 月,力勁科技已與廣東鴻圖簽署 1.2 萬噸級 壓鑄機購買合同,預計 2022 年三季度可交付,屆時行業有望實現採用一體壓鑄技術生產 一體壓鑄電池托盤。
根據我們測算,若全車身廣泛採用一體壓鑄技術,單車型壓鑄島投資約 10 億元。在 特斯拉推出一體壓鑄技術前,因新能源車用鋁量增加,鋁壓鑄件已開始在車身零件上逐 步滲透。目前前副車架(Model 3)、車門(Model X)、電機和電驅外殼已有車企採用鋁 壓鑄件。特斯拉一體壓鑄技術帶動 5000 噸以上超大型壓鑄機逐漸問世,為車身其他部位 結構件導入壓鑄提供可行性。除底盤外的 A/B/C 柱側圍、車頂、尾門、電池盒上蓋以及 CATL 推出換電方案而產生的電池倉,上述車身結構件也具備採用壓鑄工藝替代衝壓焊接 件的可能,並且目前已有車企和零部件廠在研發相關工藝和技術。中控台骨架和座椅內 部結構件國外已有採用壓鑄鎂合金替代鋼製沖焊件來減重的案例。上述結構件若全部采 用壓鑄工藝生產,則單車零件配套壓鑄相關設備投資約 10 億元左右。
按照一體壓鑄在車身結構件滲透的三個階段分析,較可能實現的第一、二階段對應年 產能 10 萬/1000 萬/5000 萬輛的壓鑄設備投資額合計為 4.4 億/436 億/2181 億元,若三個 階段中的車身結構件均採用壓鑄工藝,對應年產能 10 萬/1000 萬/5000 萬輛的壓鑄設備投 資額合計為 7.5 億/750 億/3752 億元。根據一體壓鑄在車身結構件的滲透進展,我們大致 將壓鑄在車身結構件應用的滲透分為三個階段。第一階段:以特斯拉 2020 年電池日公布 的技術路線為主,包括前後橋、電池盒體以及目前已實現壓鑄工藝量產的前副車架、電機 電驅外殼等。第一階段相關壓鑄設備按照產能/產量餘量 30%計算,對應年產能 10 萬輛車 相關的壓鑄機 周邊設備組成的壓鑄島投資額約 2 億元,對應產能在 1000 萬/年和 5000 萬 /年的設備投資額約 198 億元/989 億元。第二階段:主要包括電池盒蓋板、中控台骨架、 後副車架、車門、尾門等技術上可實現採用壓鑄工藝,且有車企和零部件廠商已有研發的 相關部件。第二階段對應年產能 10 萬輛車的壓鑄島投資額約 2.4 億元,對應產能在 1000 萬/年和 5000 萬/年的設備投資額約 238 億元/1192 億元。第三階段:主要包括 A/B/C 柱側 圍、車頂、換電電池倉、座椅結構件等。上述結構件雖可採用壓鑄工藝製造,但尚未有車 企和零部件廠商明確導入。第三階段對應年產能 10 萬輛車的壓鑄島投資額約 3.1 億元, 對應產能在 1000 萬/年和 5000 萬/年的設備投資額約 314 億元/1571 億元。壓鑄工藝在上 述三個階段的滲透,我們認為第一、二階段的部件最終採用壓鑄工藝的可能性較大,第三 階段是否最終採用壓鑄工藝存在不確定性。
2020 年我國壓鑄機市場規模僅 30 億元,力勁科技佔據行業主導地位
壓鑄機分為冷室機、熱室機兩大類,尺寸超過 10cm 以上零件需要採用冷室機。熱室 壓鑄機存在巨大的保溫鋁液坩堝,其壓室在保溫坩堝內的熔化金屬液體中,壓射機構設計 在坩堝的上方,壓鑄時壓射機構將壓室內浸滿的液態金屬壓射入模具中並成型。熱室機通 常生產尺寸較小的零件,如箱包金屬件、拉鏈頭、玩具等,材料以鋅合金、銅合金為多。 冷室壓鑄機採用卧式結構,壓室與保存熔化金屬液的坩堝爐是分開的。壓鑄工作時,由機 械臂從坩堝爐中取出液體金屬澆入壓室內,隨後壓射機構將壓室內液態金屬壓入模具內保 壓成型。尺寸超過 10cm 以上的產品,如 3C 產品結構件、5G 基站外殼、電機外殼、汽車 零部件、結構件等均採用冷室壓鑄機生產,材料通常為鋁合金、鎂合金。
2020 年我國傳統壓鑄機市場規模在 30 億元左右,受益於鋁替代鋼而總體呈持續增長 趨勢。我國製造業規模全球第一也是世界上最大的壓鑄機市場。全國壓鑄機市場規模沒有 明確的統計數據,我們根據中鑄科技公布的 2019 年國內壓鑄機市場份額以及行業龍頭力 勁科技壓鑄機業務歷年收入和內銷佔比大致推算行業空間。我國壓鑄機市場總體呈增長趨 勢,市場規模從 2012 年的 17 億增長至 2020 年的 30.5 億,CAGR6.7%。這說明壓鑄機 需求受益汽車行業規模擴大以及鋁代鋼帶來壓鑄件佔比提升在緩慢擴大中。全球壓鑄機市 場規模沒有明確的公開數據,根據力勁科技調研相關信息,我們預計中國大概佔全球壓鑄 機市場規模的 40%,則 2020 年全球壓鑄機市場規模約 75 億元左右。
預計一體壓鑄在車身結構件的滲透周期約 10~15 年
蘋果帶動手機機殼從塑料變為金屬,金屬機殼滲透率提升至 90%大致用時 7 年。2010 年蘋果從 iphone4 開始採用金屬機殼,並成功引領行業趨勢。2013 年 HTC 率先也採用鋁 合金外殼,2014 年國產智能手機品牌如小米、華為開始逐步在高端機種中採用金屬機殼。 至 2017 年,以金屬為主要結構材質的手機佔比已達 90%,手機行業機殼金屬化大致用時 7 年時間。
金屬機殼加工設備投資高峰出現在金屬機殼滲透率提升周期的中後段時間。金屬機殼 替代塑料機殼促使零部件企業大量採購 CNC。金屬機殼主要生產企業比亞迪電子、可成、 長盈精密在金屬機殼滲透率快速提升過程中均大量採購 CNC,固定資產支出同步上行。 2015 年設備採購高峰期三家公司合計資本開支近 80 億元,是 2010 年的 4.3 倍。比較金 屬機殼滲透周期和零部件企業設備投資周期,設備投資高峰出現在金屬機殼滲透率提升周 期的中後段時間。
我們預計一體壓鑄在汽車行業滲透率提升至 90%需要 10~15 年左右。我們將汽車一 體壓鑄變革與手機外殼金屬化做類比,2020 年特斯拉開始導入一體壓鑄車體類似於 2010 年蘋果發布 iphone4,業內其他企業開始探索和跟進。手機行業用 7 年左右時間將金屬機 殼滲透率提升至 90%左右。考慮到汽車行業產品迭代速度比手機行業慢 1 倍左右,我們預 計一體壓鑄車身在汽車行業滲透率提升至 90%需要 10~15 年左右時間,當行業總體形成 共識後,滲透率提升速度有可能加快。
我們預計到 2030 年全球車身結構件壓鑄機系統總累計投資額約 1614 億元。根據中 信證券研究部新能源車組的相關預測,到 2030 年全球乘用車總銷量預計在 1 億輛左右, 其中新能源車佔比預計在 40%。我們認為一體壓鑄工藝在行業滲透周期 10~15 年。至 2030 年預計第一、二階段的車身結構件可實現壓鑄替代沖焊零件,第三階段中預計一體壓鑄可 滲透約 30%的車身結構件。按照上文計算的年產能 10 萬輛車的結構件相對應壓鑄機 附屬 設備(壓鑄島)投資額約 4 億元,對壓鑄機系統到 2030 年市場空間進行敏感性分析。通 過分析,我們認為到 2030 年一體壓鑄技術在全球新能源車滲透率 70%左右,燃油車領域 滲透率 20%的假設比較合理,此種情形下對應壓鑄機系統總投資額在 1614 億元左右。
材料:免熱處理合金需求爆發,先發企業迎來新機
免熱合金是一體鑄造的剛需,性能要求更上一層樓
汽車輕量化潮流促進「以鋁代鋼」,鋁合金材料應用比例持續增加。普通 B 級車鋼製 白車身重量通常在 300-400kg,「以鋁代鋼」可使白車身種類降低 30%-40%。世界鋁業協 會報告指出,NEDC 工況下汽車自重每減少 10%,能減少 6%-8%的能耗。由於「以鋁代 鋼」減重及節能效益明顯,汽車傳統非承載件(例如殼體、支架類)已廣泛使用鋁合金材 料;近年來,隨著高緻密度壓鑄成型技術發展,部分大型、複雜、薄壁汽車關鍵承載件(如 汽車減震塔、副車架、座椅骨架、壓鑄底盤等)開始採用壓鑄鋁合金進行生產。2021 年 6 月,特斯拉宣布下一步計劃採用 2-3 個大型壓鑄結構件組裝車體總成。
傳統壓鑄結構件需熱處理、矯形,一體壓鑄下尺寸精度和成本難以兼顧。目前傳統壓 鑄結構件因其使用材料的限制,在壓鑄工藝後需要通過熱處理(高溫固溶 過時效)來提 升其強度、堅固性、延展性等指標,以達到汽車碰撞安全的要求;但是熱處理加熱和冷卻 的過程會導致零件變形,需要通過專業設備或人工進行矯形,以保證尺寸精度。這樣的工 藝設計不利於一體壓鑄技術的應用,因為零部件尺寸成倍變大後,其熱處理、矯形的製造 費用以及產生廢品的風險大幅提升,極大影響零件的生產效率和成本。因此,傳統的鋁合 金壓鑄材料難堪一體鑄造的大任,免熱處理材料應運而生。
免熱合金優勢顯著兼顧優異性能與降本增效。傳統熱處理鋁合金材料,僅適用於壓鑄 中小型結構件,總成組裝仍需經過數十至上百次的鉚接/焊接過程。免熱處理鋁合金具備非 常好的熱穩定性能與力學性能,適合大型壓鑄件生產,可實現一次簡單壓鑄加工,由焊接 幾小時改善為壓鑄幾分鐘,精簡連接工序、節約生產時間,使得車身結構件的成本和性能 具有較大優勢,亦提高產品的良品率,並可以減少碳排放(省去零件壓鑄後的熱處理工藝), 順應碳中和節能減排趨勢要求,所以其為一體壓鑄最佳材料選擇。(報告來源:未來智庫)
抽絲剝繭,一體壓鑄對合金材料要求有哪些?
(1)力學性能要求更高。一體化大鑄件通常具有尺寸大、壁薄、結構複雜等特徵, 且大型關鍵結構件在服役過程中往往承受持續、交變的載荷,因此一體化壓鑄件需要滿足 車身不同部位對受力、強度以及韌性的不同要求。在力學性能方面,免熱處理合金需具備 強的塑性和強度,該指標越高對應材料減重效果越明顯亦兼顧提升零件碰撞,疲勞性能; 此外,一體化大鑄件難以做到鑄件整體各區域的性能統一,需採取不同的連接方式對材料 性能要求不同,因此,材料需具備高的連接包容性;大鑄件流程較長對材料的充型距離挑 戰較大,需具備較好的鑄造性能避免材料欠鑄與變形等問題。
(2)更高的微量元素和雜質元素包容度。免熱合金出品率為 60%,40%的回爐料需 要重新使用,此外還可能結合再生料使用,兩種材料會帶來微量與雜質元素可能引起材料 粗化,需在材料設計時給予更高的微量、雜質元素容忍度,確保經濟性及鑄件的性能要求。
(3)長效的、高效的變質劑。免熱處理合金沒有熱處理流程在凝固過程中直接形成 組織,只能依靠單一的組織調控,主要是依靠變質劑進行組織調控,來實現材料的強度和塑性。實際生產過程中,大鑄件由於機台或模具需要熔體長時間保溫,在該過程中如果變 質劑不具備長效與高效特性,會打斷生產的連續性。
(4)完善的材料資料庫(包括材料物性參數與不同材料卡片)
材料物性參數資料庫。大鑄件無法做到所有位置性能一致,不用位置由於結構或 充型的差異帶來不同力學性能,在零件設計時需要把完整的材料物性參數,帶入 到高精度的鑄造模擬過程中,以識別出生產過程中哪些流程或位置較大概率存在 缺陷,並採取措施應對。
不同材料卡片(服役性能資料庫)。大鑄件無法做到所有位置性能一致,零件設 計時在進澆口、遠澆口、合流或者填充流向改變的位置,在這些本體性能較差時, 不同區域賦予對應材料卡片,旨在模擬中得到真實零件受力,為零件設計在模擬 方面提供安全的保證。
免熱合金需求快速釋放,預計國內 2022-2025 年市場規模 CAGR 為 161%
一體壓鑄加速滲透,其中材料端免熱合金需求快速釋放空間廣闊。我們對 2022-2025 年國內與國外新能源車與 2030 年國內與國外乘用車整體免熱處理合金市場空間進行測算。 預計 2022-2025 年國內新能源車整體免熱合金市場規模分別為 8.15 億元、22.97 億元、 46.35 億元、145.15 億元,對應 2022-2025 年 CAGR 為 161%;保守/中性/樂觀情形下估 計 2030 年國內乘用車整體免熱合金市場規模為 377/562/665 億元。伴隨主機廠一體壓鑄 強需求牽引,大型壓鑄設備與配套模具持續落地提供強底層支撐,材料端免熱處理合金成 功革新,產業鏈各環節配合漸入佳境,工藝愈發成熟,模式逐步跑通,一體壓鑄有望加速 滲透帶動免熱合金需求快速釋放。測算過程及相關假設如下:
免熱合金用量測算倒推過程: 根據前文一體壓鑄結構件空間測算結果,我們去除掉不使用熱合金的一體壓鑄結構件 空間,主要包括 2030 年時保守假設下的前副車架、電機/電驅外殼,中性假設下後副車架、 車門,樂觀假設下車頂、汽車座椅等部位,得出使用免熱合金一體壓鑄結構件市場空間, 再除以一體壓鑄結構件平均單位價值量(假設為 35 元/kg),最後得出免熱合金總體用量。 免熱合金價格假設: 假設鋁價保持在 20000 元/噸左右,材料商加工費假設為 5000 元/噸,對應單噸鋁價 為 25000 元左右。
免熱合金技術與專利壁壘高,強者恆強的可能性大
免熱處理合金材料成分、工藝複雜,具備較高的技術壁壘,其中合金材料成分設計是 免熱處理合金開發的核心技術壁壘。
(1) 合金主要成分配比是合金性能基礎:常用壓鑄鋁合金可以分為 Al-Si 系、Al-Mg 系、 Al-Si-Cu 系、Al-Si-Mg 系,主要成分配比影響合金強度、硬度等力學性能指標, 同時影響流動性、凝固性等鑄造性能指標;
(2) 微量特殊元素引入可調節合金品質但元素選取與引入比例較難把握:以上海交大 輕合金中心專利《一種非熱處理強化高強高韌壓鑄鋁鎂銅合金及其製備方法》為 例,Al-Si-Cu 系合金,可通過引入稀土元素 Y、Er 以及 Ce 作為活性元素,形成 細小彌散相以提高合金的強度;德國德國萊茵金屬公司的 Castasil-37 合金是一種 高韌性 Al-Si 合金,主要通過添加微量 Mo、Zr 等元素提高壓鑄過程的合金強度。 但是微量元素的選取種類較難確定及引入區間較窄或特定,不同元素有其各自性 能優缺點,且不同元素之間可能存在相互作用,只有當元素種類選取合理且各元 素添加比例適宜時,才能生產出符合要求的免熱合金,技術難度較大,這需要生 產企業長時間的生產實踐經驗積累,擁有多年材料配方設計經驗。
同時需在材料選用、凈化處理、工藝過程保障等方面綜合調控保證合金性質 (1)材料選用:需要依據成分設計結構,選用純度較高的電解鋁、工業硅和其他添 加材料,保證雜質 Fe、Ca、Na、P 等元素儘可能少的帶入,才能保證鋁合金材料具有良 好的鑄造能力和充型能力、較好的延展性、良好的抗拉強度和良好的屈服強度。 (2)凈化處理:通過對鋁液中非金屬夾雜物、氧化物及含氣的高效去除,方能保證 鋁液具有較高的純凈度,從而避免因鋁液中含氣量影響,提高產品良率。 (3)澆鑄工藝:適宜的澆鑄溫度和澆鑄參數,可保證合金材料具有均勻、緻密的晶 粒組織及較好的力學性能。
專利壁壘:對合金材料配方成分進行鎖定,其他企業需「繞道而行」
專利壁壘鎖定合金成分,後發超車難度加大。基於上文分析我們知道合金材料成分料 配方設計為技術壁壘的核心,而專利壁壘主要是通過專利中對於合金中其他元素添加的比 例進行限制,後發者需要繞過原有專利的配方成分設計研發出符合主機廠要求的免熱合金材料,技術難度愈發加大,行業門檻進一步拔高。即使後發企業繞過專利壁壘成功突破免 熱合金技術研發,後續還將面臨量產階段的產品性能與成本平衡問題,後發超車難度加大。
免熱合金後續格局演繹有望呈現強者恆強趨勢。我們認為具備先發優勢的免熱合金廠 家有望強者恆強,主要原因將從以下三個維度闡述:
維度一:後發者面臨多重困難。後發廠家需要長周期經驗積累與高研發投入才可能繞 過現有專利配方實現免熱合金技術突破,新材料技術突破非一蹴而就,以行業基本規律來 看,一項新材料技術的開發至少需要 5-10 年,甚至更長的時間,即使研發成功後續還 將面臨量產之後產品性能與成本的平衡問題,難度進一步加大。
維度二:合作商應用材料一旦定型轉換成本較高。前期一體化產品設計流程中主機廠 需求、材料性能與對應壓鑄模具、壓鑄工藝參數等需相互針對性優化,各個節點緊密配合 才能促成最終壓鑄件穩定生產。一旦先發者材料在車企廣泛推廣應用,較大可能成為這套 體系里的早期標準制定者,定型之後如果出現新的材料想要進行應用替換,這需要重新更 改後續流程的模具、改衝壓工藝等等,過程複雜,代價較大。即使後發者材料性能更優, 大多數車企也不願意做出調整和改變。所以早期搶佔市場者後續有望獲得最為陡峭成長曲 線。
維度三:先發者產品持續迭代升級與降本強者恆強。在此期間先發廠家基於產品應用 經驗積累與持續研發投入進行產品迭代升級,同時可通過推進應用再生料於免熱材料的研 發和生產過程中的技改提效等方式,助力未來成本進一步下探,強化產品量產性價比優勢, 構築強大客戶粘性壁壘,引領技術先進性與市場份額。
不受自供、外攜等商業影響,享受行業增量確定性高
主機廠自供和第三方供應的方案將長期共存。目前一體壓鑄模式主要有車企自供、第 三方壓鑄廠合作兩種模式,目前除特斯拉採取自供外,其他主機廠大多採取與壓鑄廠合作 供應方案,兩種模式共存的狀態將長期存在。
成本之差:規模效應是關鍵。一體壓鑄前期需一次性投入高價值大型壓鑄設備、配套 設施廠房等固定成本,所以產能利用率高低通過固定成本攤薄直接影響產品單位成本,第 三方壓鑄廠基於單台大型壓鑄設備,可以通過更換不同模具配套多家主機廠不同車型產品, 提升單台設備產值,實現單位固定成本快速下降,同時產能飽滿帶來生產連續性提升與能 源利用率提升,單位能耗降低。疊加學習效應助力生產效率與製造成熟度提升,實現單位 可變成本的下行。而主機廠自行壓鑄結構件主要是配套自家有限車型,目前,大多數主機 廠銷量規模難以匹敵特斯拉,規模效應不足直接推高一體壓鑄結構件單位成本,短期主機 廠難以看見正向利率將會積極尋求與第三方供應商合作。
關注享受一體壓鑄趨勢高確定性的材料廠商
一體壓鑄商業模式持續演繹,材料廠商影響較小高確定性凸顯。基於前文分析兩種模 式競爭格局將長期存在,短期看第三方供應方案或為主流模式,長期看主機廠自供比例有 望提升。無論商業模式演變趨勢如何,對於材料廠商影響較小,主要系無論是主機廠自供 亦或與第三方壓鑄供應商合作,如若實現一體壓鑄結構件最終落地應用免熱合金材料是剛 性需求,材料廠商格局較好可以選擇與主機廠或供應商合作免疫商業模式變化,充分享受 一體壓鑄加速滲透的高確定性高景氣紅利。(報告來源:未來智庫)
國內外免熱處理鋁合金材料開發進展
國外:主流高品質免熱處理鋁合金材料開發者仍以外企為主。如美國鋁業公司,其產 品為 EZCAST?系列 C611 免熱處理 AI-Si 系壓鑄鋁合金等,該系列合金由美國鋁業公司 在上世紀 90 年代開發成功,並應用於奧迪 A8 的全鋁車身的結構件上。此外,德國萊茵金屬公司也開發出 Al-Si 系和 Al-Mg 系免熱處理高強韌合金,如 Castasil-37 壓鑄鋁合金;加 拿大鋁業公司則開發有 Aural-2 和 Aural-3 等壓鑄鋁合金材料。
國內:免熱合金可量產廠家稀缺,目前競爭格局良好。目前國內免熱處理鋁合金材料 實現自主研發突破,性能指標滿足汽車結構件要求。競爭格局方面,目前國內僅立中集團 具備自主知識產權技術成熟並具備可量產能力,其他廠家或為海外合金廠商授權應用或為 高校研發階段暫不具備量產能力。行業具體情況如下:立中集團歷經十年的技術創新,打 破國外技術壟斷,研發出 LDHM-02 免熱處理合金材料具備自主知識產權,並形成批量供 貨,稀缺性顯著。帥翼馳集團與美國鋁業簽訂獨家代理協議,代理美鋁高強韌免熱處理鑄 造鋁合金;上海交大輕合金中心研發免熱處理高強高韌壓鑄 JDA2b 合金,2021 年 12 月, 上海交大輕合金中心與華人運通高合汽車達成戰略合作。雙方全球首發 TechCastTM 超大 鑄件用低碳鋁合金,將在高合汽車後續車型上大批量採用。
重點公司分析
文燦股份
公司高壓鑄鋁結構件技術國內領先,受益行業變革確定性高。根據公司招股說明書, 公司於 2014 年研發成功並實現量產,為國內最早。公司現已穩定配套賓士、特斯拉和蔚 來等豪華品牌客戶。2017 年,公司結構件產品銷售收入僅為 0.7 億元,而 2020 年已達 3.5 億元,規模快速提升。2020 年,公司成功開發了理想汽車、加拿大龐巴迪和恆大汽車等 新客戶,並獲得了蔚來新款車型和北京賓士的車身結構件新項目,對新老客戶的滲透不斷 加深。高壓鑄鋁結構件對材料、設備和模具等核心環節技術的要求較高,「一體壓鑄」難 度將進一步提升;公司已訂購 9000T 等大型壓鑄機,加速一體化壓鑄技術產品研發,構築 行業護城河。
收購法國百鍊,開啟全球化進程。2020 年 12 月,公司完成對法國百鍊集團 100%股 權收購。法國百鍊集團是全球領先的汽車制動系統精密鋁合金鑄件生產企業,主要產品工 藝為低壓和重力鑄造,主要客戶為標誌雪鐵龍、寶馬等整車廠和大陸、采埃孚等一級供應 商。收購百鍊集團後,公司實現高壓鑄造、低壓鑄造和重力鑄造的工藝全覆蓋,並有望借 助百鍊的客戶群體實現全球擴張。
「一體壓鑄」引領汽車生產潮流,公司在新勢力定點進展順利。特斯拉採用「一體壓 鑄」工藝,相比鋼鋁混合車身實現 40%的降本效果。在降本效應驅動下,我們預計全球整 車廠生產模式將發生重塑,高壓鑄鋁結構件單車價值有望從 3000 元提升至 6000 元以上, 滲透率有望從 8%(約 35 萬以上車型) 提升至 30%(20 萬以上車型),行業 2030 年空 間有望達到 1000 億以上,10 年 CAGR 為 30%。公司鋁壓鑄車身結構件產品技術國內領 先,已實現為戴姆勒、特斯拉和蔚來等頭部品牌的配套。此外,公司與力勁科技簽訂了戰 略合作協議,公司採購包括 6000T、9000T 在內的 9 台大型、超大型壓鑄機。目前 6000T 壓鑄設備上的試製產品已在某知名頭部新勢力客戶整車廠中完成白車身安裝下線;9000T 壓鑄機定點產品已經開始試製階段工作,用於另一知名頭部新勢力客戶的 SUV 車型。我 們預計隨著壓鑄機調試不斷成熟,公司有望未來充分享受新勢力客戶帶來的增量,行業領 先地位進一步鞏固。
拓普集團
公司是國內優質、稀缺的 Tier 0.5 級平台型零部件供應商。公司是國內特斯拉產業鏈 核心供應商,單車配套價值量大,業績彈性高。公司客戶拓展順利,除核心客戶外,公司 積極拓展 Rivian、Lucid、華為、金康、高合、小米、理想等國內外創新車企客戶,單車配 套價值有望隨合作進一步提升。公司基於底盤底層能力積累,在空氣懸掛、線控轉向、電 子膨脹閥等核心總成及零部件方面積極投入研發。我們認為,隨著國內新能源汽車滲透率 不斷提升,公司在智能電動汽車客戶拓展方面穩步推進,業務成長增加新動能。
加碼輕量化底盤,定增發力拓展客戶。2021 年 12 月 30 日,公司公開發行可轉債申 請被證監會受理,擬募集不超過 25 億元全部投資於寧波杭州灣新區四期土地的輕量化底 盤系統建設項目(年產 150 萬套)及寧波杭州灣新區五期土地的輕量化底盤系統建設項目 (年產 330 萬套)。此外,公司擬在重慶設立全資子公司,投資 15 億元分期建設新能源汽 車各產品線生產基地,積極布局新能源汽車輕量化底盤系統暨內飾隔音件系統生產基地。 公司在輕量化底盤業務方面頻頻擴產,訂單層面能夠滿足更多的新能源客戶,在輕量化底 盤的技術上也能夠鞏固其行業地位,以便提前搶佔更多的市場份額。
平台型零部件公司典範,產品品類不斷拓展。公司作為平台型零部件公司,在原有汽 車內飾、隔音及減震產品基礎上,持續前瞻布局輕量化、電動化和智能化賽道,不斷拓展 公司的行業競爭優勢,其中公司為電動皮卡品牌 RIVIAN 配套的單車價值達 11000 元。此 外,公司依託研發 IBS 智能剎車系統所積累的電控及精密製造的能力,成功研發集成式熱 泵總成、電子膨脹閥和電子水閥等產品,熱管理總成開始深度配套新能源核心客戶,單車 價值量接近 3000 元。依託在線控制動研發過程中形成的機械、電控、軟體能力以及底盤 調校能力,結合公司在橡膠方面和真空泵方面的多年經驗積累,公司迅速開發空氣懸架系 統項目,單車配套 5000-10000 元,在汽車消費升級的時代,具備很大的市場空間。在智 能化領域,公司已具備為客戶提供 IBS EPS 一體化解決方案的能力,大幅減少主機廠的 研發匹配工作量,預計將於今年量產,為客戶提供更多增量價值。
愛柯迪
鋁高壓鑄造龍頭,市場空間持續增長。公司是國內領先的汽車鋁合金精密壓鑄件專業 供應商,當前積極推進產品結構轉型,加快推進產能釋放,把握電動化、智能化發展趨勢, 聚焦汽車輕量化、節能環保,重點發展新能源汽車相關業務。長期來看,公司是國內領先 的鋁高壓鑄造龍頭,逐步提升的全球汽車產銷量及汽車用鋁量將促進汽車鋁合金精密壓鑄 件的市場空間持續增長。
公開發行 16 億可轉債,把握一體壓鑄大趨勢。公司 2022 年 1 月 12 日發布公告,擬 公開發行總額不超過人民幣 16 億元(含 16 億元)可轉換公司債券,期限為自發行之日起 6 年,優先配售公司原股東。募集金額在扣除發行費用後將全部用於愛柯迪智能製造科技 產業園項目的建設發展。該項目投資總額為 18.9 億元,將新建車間廠房、全自動立體倉庫 等約 137,255 平方米,建成後新增新能源汽車電池系統單元、新能源汽車電機殼體、新能 源汽車車身部件和新能源汽車電控及其他類殼體等 710 萬件產能。此外,通過實施本次募 集資金投資項目,公司將引進 800 噸到 8400 噸不等的國內外先進中大型精益壓鑄單元, 增強公司在一體化壓鑄領域競爭力,在這一由電動化催生的新賽道中佔據先機。
新能源、智能化項目不斷突破,高固相半固態成型技術持續向前。2020 年,公司收 購銀寶壓鑄 51%股權,設立半固態成型專業化產品生產工廠,開拓公司在高緻密性、高力 學性能鑄件方面的供應能力。報告期內,公司固態產品在新能源汽車電池包系統、電驅系 統、熱管理系統等方面取得零的突破,我們判斷 2021 年至今半固態項目壽命期內新增銷 售收入佔比約為 10%。公司獲取新項目生命周期內預計新增銷售收入再創新高,新增法雷 奧、大陸、匯川技術、海康威視、舜宇集團、速騰聚創、蔚來等新能源汽車或汽車智能化 項目,未來增長動力十足。(報告來源:未來智庫)
旭升股份
深耕鋁合金成型領域,深度應用壓鑄、鍛造、擠壓三大工藝。公司是全球汽車輕量化 零部件產業鏈中的重要一員。2021 年實現營收 30.23 億元,同比 85.8%;實現歸母凈利 潤 4.13 億元,同比 24.2%。2021 年公司鋁壓鑄板塊在手訂單持續放量,新增長城 DHT 雙電機、賓士電機殼體、LUCID 動力系統、車身系統、電池系統等部件項目順利量產。此 外,公司鍛造、擠出業務拓展順利:鍛造業務新增新能源汽車轉向節、熱管理系統閥板等 多個項目定點或量產;擠壓業務新增多個電池包殼體零部件項目,且有防撞梁、門檻梁、 副車架、電池包箱體等多個產品項目在研,行業影響力持續提升。
募資夯實輕量化產品競爭力,提前布局一體壓鑄。2021Q3,公司發行可轉債 13.5 億 元,其中 9.7 億元用於高性能鋁合金汽車零部件項目,新增新能源汽車傳動系統殼體產能 234 萬件、新能源汽車電池系統部件產能 57 萬件和新能源汽車車身部件產能 50 萬件;3.8 億元用於汽車輕量化鋁型材精密加工項目,新增新能源汽車傳動系統殼體產能 62 萬件、 新能源汽車電池系統部件產能 95 萬件。我們認為,本次發行可轉債有助於公司在汽車輕 量化領域產能繼續實現爬坡,行業龍頭地位進一步鞏固。此外,公司提前布局一體壓鑄, 將在未來三年內向海天金屬引進型號 1300T-4500T、6600T 和 8800T 的多套冷室壓鑄島, 為公司長期保持鋁製汽車零部件領域優勢提早鋪墊。
客戶拓展順利,鑄鍛、型材等鋁合金新產品放量。公司自 2013 年便成為特斯拉的一 級供應商,當前特斯拉為公司第一大客戶,2021 年貢獻銷售收入 12.1 億元,同比 70.6%。 除特斯拉外,采埃孚、長城汽車、寧德時代等客戶的持續放量也對公司營收和業績的增長 有較大貢獻。公司不斷開拓新產品,擠出產品新獲大眾 MEB 平台電池包零部件產品的定 點,新能源電池包業務已取得寧德時代、億緯鋰能、賽科利等多個客戶項目。同時,新產 品鑄鍛件已開始配套特斯拉、理想、福特、采埃孚和寶馬等客戶,未來業績增量料將穩步 提升。
立中集團
公司是輕合金新材料及汽車輕量化材料領域全球供應商。立中集團主營中間合金、再 生鑄造鋁合金材料和鋁合金車輪產品三大業務,各業務板塊均為細分行業龍頭,也是行業 內唯一一家擁有熔煉設備研發製造、再生鑄造鋁合金研發製造、功能中間合金研發製造、 車輪模具研發製造、車輪產品設計和生產工藝技術研究製造完整產業鏈的公司。此外公司 持續多元布局鋰電新材料、免熱合金領域。未來隨著一體壓鑄成型產品的市場需求逐步釋 放,公司的免熱處理合金有望實現規模化生產,進一步提升公司的綜合競爭實力和盈利水 平。
立中免熱合金產品兼顧高強、高韌性與低成本優勢,先發優勢富集。2021 年中報披 露,立中集團研發的 LDHM-02 免熱處理合金材料已獲得相關專利,並形成批量供貨。實 現了大尺寸、薄壁、結構複雜和熱處理易變形的汽車結構件「以鋁代鋼」材料替代,特別適 用於新能源汽車保護鋰電池免受外界碰撞和擠壓的電池承載件以及汽車「以鋁代鋼」一體壓 鑄成型車身等應用場景。根據立中集糰子公司申請中的最新相關專利《一種高強韌免熱處 理鋁合金材料及製備方法》,公司該專利開發的鋁合金材料屈服強度達 130Mpa,抗拉強度 達到 250Mpa,伸長率大於 10%,滿足客戶使用需求。相較於同類產品立中產品擁有綜合 的優異性能表現,兼顧高強、高韌性與低成本優勢。立中免熱合金產品先發優勢富集,有 望在一體壓鑄材料端拔得頭籌,並推進應用再生料於免熱材料的研發,助力未來成本進一 步突破,有望持續引領技術先進性、市場份額與量產性價比優勢。
立中、文燦強強聯合,助力立中免熱合金市場化應用和快速推廣。雙方合作共同開發 大型一體化鋁鑄件的免熱處理材料,其中立中負責材料配方的研發,文燦股份負責研發應 用工藝條件。雙方合作互為獨家,但有排除條款:(1)雙方協議生效前已配套客戶除外, (2)汽車主機廠(含汽車主機廠系統內投資的鑄造廠)生產在系統內使用除外,(3)雙 方共同認可,共同確認的也可以排除在外,未來立中與整車廠商合作可能仍存。強強聯合 助力立中集團客戶結構多元化且範圍進一步拓寬。立中集團通過獨家協議共享文燦優質客 戶資源且被優先推薦,目前立中已拓展客戶疊加未來潛在的文燦客戶資源,公司一體壓鑄 客戶資源獨佔鰲頭,護航立中產品加速量產保障較高市場份額。
(本文僅供參考,不代表我們的任何投資建議。如需使用相關信息,請參閱報告原文。)
精選報告來源:【未來智庫】。未來智庫 - 官方網站

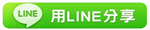
※AR行業專題報告:消費級AR賽道持續預熱,國內廠商有望獲益
※導彈行業專題報告:補庫存疊加實戰化訓練,精確制導武器快速發展